Controlul procesului de producție a fierului vermicular
În comparație cu fierul gri, rezistența la tracțiune a fierului vermicular este mărită cu cel puțin 70%, modulul de elasticitate este mărit cu 35%, iar rezistența la oboseală este aproape dublată. În comparație cu aliajul de aluminiu, rezistența și rigiditatea fierului vermicular sunt de două ori mai mari, iar rezistența la oboseală este de două ori mai mare. Aceste caracteristici ale fierului vermicular oferă posibilitatea motorului de a îmbunătăți raportul putere / greutate și de a crește presiunea cilindrului. Creșterea presiunii cilindrilor este cheia performanței optime a motorului diesel cu injecție directă de nouă generație. Pentru a face față aplicării pe scară largă a fierului vermicular, industria turnătoriei se pregătește în mod activ, investind intens și reconstruind noi procese pentru a face producția de fier vermicular stabilă și fiabilă.
Pentru motoarele cu fier vermicular de la prototip la producția în serie, factorul decisiv este riscul de calitate. Pentru fierul vermicular de înaltă calitate, zona stabilă este foarte mică, doar în intervalul de 0.008% conținut de magneziu. O cantitate de urme, cum ar fi o pierdere de 0.001% magneziu, va produce grafit în fulgi, ceea ce va face ca proprietățile mecanice să scadă cu 25% până la 40%. Acest articol descrie un sistem de control al proceselor bazat pe metode de analiză termică. Sistemul măsoară pierderea de magneziu și reglează starea fierului topit online pentru a preveni generarea de grafit în fulgi. Această metodă de control online de măsurare și ajustare reduce volatilitatea în procesul de producere a fierului vermicular până la cel mai mic punct și elimină fundamental riscul de calitate cauzat de producerea fierului vermicular.
Cererea de putere mare, cuplu ridicat, emisii reduse de evacuare și consum redus de combustibil continuă să crească. Acest lucru îi obligă pe proiectanții motoarelor diesel de mare putere să mărească presiunea maximă de aprindere, ceea ce mărește foarte mult sarcina termică și sarcina mecanică a motorului. Sarcina termică și sarcina mecanică cresc în același timp, astfel încât motoarele convenționale din fontă și fontă din aliaj (CrMo) utilizate în prezent au atins sau au depășit limita superioară de utilizare a acestora. Producătorii de motoare au nevoie de materiale cu rezistență mai mare și o rezistență mai bună la căldură.
Fierul vermicular a devenit rapid materialul preferat pentru oameni. Îmbunătățește foarte mult fiabilitatea blocului de cilindri, a chiulasei și a garniturii de cilindri a noii generații de motoare pentru camioane. Pentru a obține cea mai bună combinație a diferitelor proprietăți (cum ar fi proprietățile de turnare, proprietățile de prelucrare, conductivitatea termică și proprietățile mecanice), aceste piese trebuie realizate cu o rată de sferoidizare de la 0% la 20% (rata de strecurare de 80% la 100% ) Fabricat din fier vermicular. Dacă rata de sferoidizare depășește 20%, aceasta va provoca o serie de factori nefavorabili. De exemplu, cantitatea de contracție este prea mare, iar piesele cu forme complexe, cum ar fi chiulase sunt deosebit de predispuse la contracție. Un alt exemplu este reducerea duratei de viață a sculei din cauza uzurii excesive în timpul prelucrării. Există, de asemenea, o scădere semnificativă a conductivității termice, provocând stres termic și așa mai departe. La celălalt capăt al fierului vermicular, apariția grafitului în fulgi va determina o scădere liniară a proprietăților mecanice, ceea ce face ca motorul să nu poată îndeplini noile cerințe. Pe scurt, pentru a satisface nevoile noii generații de motoare pentru camioane, rata de sferoidizare a fierului vermicular de înaltă rezistență trebuie să fie cuprinsă între 0% și 20% (adică rata de târâre este peste 80%, fără fulgi).
Indiferent dacă se folosește sau nu controlul procesului de producție depinde de producția anuală a produsului, de complexitatea produsului și de gama admisibilă de modificări în structura metalografică. Așa cum se arată în Figura 1, piesele relativ simple, cu volum redus, cum ar fi matrițele pentru lingouri, pot fi produse în general prin metode de turnare convenționale. Controlul procesului nu este în general necesar și nu este rentabil din punct de vedere economic. Atunci când producția anuală a componentelor crește, cum ar fi țevile de eșapament, manșoanele manivelelor și consolele, ar trebui să fie logic să introducem controlul procesului. Deși acest tip de produs are o producție anuală mare, tonajul anual al turnării nu este ridicat. Cerințele structurii metalografice nu sunt foarte stricte, permițând rata de sferoidizare să fie de până la 50%. În plus, datorită cantității mici de prelucrare a unor astfel de piese, creșterea titanului care poate fi adăugată în producție poate permite extinderea gamei controlabile. Pentru acest tip de produs, metodele convenționale de turnare și instruirea strictă sunt în general competente pentru producția de fier vermicular. Dar, din perspectiva controlului calității, controlul proceselor ar trebui să fie mai sigur. În mod similar, controlul procesului oferă, de asemenea, o garanție pentru producția de blocuri mari de motoare marine și chiulase. Deși dimensiunea mare și cantitatea redusă de producție sunt favorabile fabricării produselor, pierderile economice cauzate de produsele care depășesc standardul sunt suficiente pentru a adăuga un set de sisteme de control al procesului.
Produsele care au cea mai mare nevoie de control al procesului sunt blocurile de cilindri ale motorului auto, chiulasele și discurile de frână cu producție anuală mare, complexitate ridicată și cerințe tehnice stricte. Volumul anual de producție și tonajul anual al acestor produse sunt foarte mari. Sunt de dimensiuni complexe, solicită structura metalografică și tind să producă cavități de contracție. Aceste produse nu trebuie să prezinte riscuri de calitate, altfel pierderea va fi foarte gravă.
Cerințele stricte privind performanța blocului motorului, chiulasei și scaunului cilindrului au pus bazele pentru producerea specificațiilor produsului. Pentru a obține cele mai bune performanțe cuprinzătoare de turnabilitate, prelucrabilitate și proprietăți mecanice, rata de sferoidizare trebuie să fie cuprinsă între 0% și 20% în toate părțile cheie ale componentei. Mai important, grafitul cu fulgi trebuie evitat în mod absolut pentru a preveni deteriorarea pieselor cauzate de slăbiciunea locală. Pentru a obține o bună aditivitate mecanică, carburile libere trebuie reduse la minimum. Prin urmare, titanul nu trebuie adăugat niciodată. În cele din urmă, din punct de vedere al producției, turnătoria are nevoie de un proces stabil și fiabil pentru a asigura cea mai mică rată de deșeuri cauzată de structura metalografică. Producătorii din industria auto necesită asigurarea calității, iar 100% din piesele turnate trebuie să îndeplinească cerințele metalografice. Producția pe scară largă și fiabilă de blocuri de cilindri, chiulase și scaune de cilindri necesită o analiză precisă și o ajustare online a fierului topit pentru a elimina fluctuațiile procesului înainte de turnare.
Stabilitatea fierului vermicular
Motivul pentru care fierul compactat nu este utilizat în cantități mari pentru a produce piese complexe (cum ar fi blocurile motorului) se datorează faptului că zona stabilă a fierului compactat este prea mică pentru a se asigura că nu există niciun risc în producție. În general vorbind, această zonă stabilă se întinde doar pe suprafața de 0.008% magneziu, așa cum se arată în Figura 2. Dimensiunea și poziția platformei în zona stabilă variază în funcție de produs. De fapt, gama de magneziu disponibilă este mai mică decât aceasta. Deoarece la fiecare 5 minute, magneziul activ va arde 0.001%. Punctul inițial de turnare a fierului topit trebuie să fie suficient de departe de punctul de cotitură ascuțit al fierului compactat până la fierul gri pentru a se asigura că nu apare grafit în fulgi în partea finală turnată. Când se adaugă magneziu la fierul topit, grafitul în fulgi va apărea în aproximativ 15 minute.
Punctul de plecare nu trebuie să fie prea aproape de partea dreaptă a platformei stabile (conținut ridicat de magneziu), altfel va provoca formarea unei cantități mari de grafit sferoidal în partea mai subțire și partea de răcire rapidă.
În plus față de zona mică a platformei disponibile, zona platformei este mereu în mișcare. Dacă conținutul de oxigen activ și sulf este mare, vor consuma mai mult magneziu activ și întreaga platformă se va deplasa spre dreapta (conținut ridicat de magneziu). În schimb, dacă conținutul activ de oxigen și sulf este scăzut, platforma se va deplasa spre stânga (conținut scăzut de magneziu). Modificările în compoziția materiilor prime, puritatea, gradul de oxidare și umiditate etc., fac imposibilă controlul fierului vermicular cu o gamă fixă de compoziție chimică.
Deși conversia de la fierul vermicular la fierul gri trebuie doar să reducă magneziul activ cu 0.001%, arderea magneziului nu face ca întreaga parte să devină grafit în fulgi. Când magneziul activ nu este suficient, grafitul formează mai întâi fulgi și se extinde spre exterior pe măsură ce se solidifică, iar magneziul se lasă și se concentrează la capătul frontal al interfeței solid-lichid. Dacă cantitatea inițială de magneziu activ este adecvată, grafitul vermicular se va forma la limita eutecticii, așa cum se arată în Figura 3. Grafitul fulg apare mai întâi ca pete de grafit fulgi împrăștiate. Spre deosebire de orice grafit obișnuit, aceste pete izolate de grafit sunt dificil de detectat cu ultrasunete. Probabilitatea ca acestea să fie scanate cu ultrasunete nu este mare.
Sensibilitatea magneziului la fierul vermicular poate fi arătată în Figura 4: Într-o tonă de oală fierbinte de metal, adăugați doar 10 grame de magneziu, petele de grafit de fulgi dispersate în proba de testare Φ25 pot fi complet transformate în grafit vermicular. Rezistența la tracțiune a barei de testare cu pete de grafit fulg este de numai 300 MPa, în timp ce rezistența la tracțiune a aceleiași bare de testare cu fluaj complet atinge 450 MPa.
Inoculantul este, de asemenea, foarte sensibil la platforma stabilă a fierului vermicular, așa cum se arată în Figura 5: adăugarea a 80 de grame de inoculant la o tonă de fier topit va crește rata de sferoidizare în bara de test Φ25 de la 3% la 21%. Cantitatea de inoculare este mare, iar nucleul de cristal este mult, ceea ce este favorabil formării grafitului sferic. Acest lucru ridică platforma de fier vermiculară în direcția ratei ridicate de sferoidizare. Rata scăzută de inoculare face ca platforma să se deplaseze în jos. Numeroși factori, cum ar fi temperatura de supraîncălzire a fierului topit, timpul de păstrare, compoziția chimică a materiilor prime, tipul de inoculant și cantitatea de inoculare, vor afecta poziția platformei de fier vermicular.
Cea mai esențială cerință a oricărei tehnologii de control al procesului este măsurarea și analiza precisă a stării fierului topit. Pentru fierul vermicular, controlul fiabil al producției necesită măsurarea simultană a punctului critic al magneziului activ din tranziția fluaj-cenușă, gradul de ardere ulterioară a magneziului și gradul de inoculare.
Proba de analiză termică de 200 de grame se obține prin introducerea sondei Xinte în fierul topit după sferoidizare și inoculare. În timpul procesului de inserție de trei secunde, peretele sondei și fierul topit ating o stare de echilibru termic. Diferit de ceașca de probă convențională pentru analiză termică, acest eșantionator cu pereți subțiri nu numai că garantează același volum de eșantion de fiecare dată, dar evită și oxidarea fierului topit care se revarsă în paharul de probă. Măsurarea supraîncălzirii este mai precisă, deoarece nu există un fenomen precum condensul violent în analiza termică convențională.
Așa cum se arată în Figura 6a, sonda Xinte este realizată din tablă de oțel întinsă presată. Este practic un container sferic. Peretele subțire de oțel care conține fierul topit are un strat de izolație asemănător unui balon. Grosimea stratului de izolație este îngroșată simetric în funcție de direcția înălțimii pentru a asigura o disipare uniformă a căldurii și răcirea către împrejurimi, iar apa de fier din zz din acesta este aproape de solidificarea unui corp sferic. Există două termocupluri de tip N în tubul de protecție din sondă. Termocuplul poate fi extras după fiecare măsurare și utilizat în mod repetat de mai mult de 100 de ori. Una dintre cele două termocupluri este situată în partea de jos a containerului, iar cealaltă este situată în centrul termic al containerului. Deoarece recipientul este sferic și este suspendat liber (acest lucru este diferit de ceașca de probă convențională pentru analiză termică care se sprijină pe un suport de absorbție a căldurii), fierul topit generează un flux uniform de căldură în recipient, așa cum se arată în Figura 6b. Acest flux de căldură face ca fierul topit să fie schimbat continuu în recipient, formând o partiție de flux în partea de jos a sondei.
Pentru a imita pierderea naturală a fierului topit în timpul turnării, există un strat pe peretele sondei care reacționează cu magneziul activ. Fierul topit curge de-a lungul peretelui acoperit condus de fluxul de căldură. După reacție, conținutul de magneziu al fierului topit scade și se acumulează în compartimentul de la baza recipientului. Direct vorbind: termocuplul din centrul sondei măsoară fierul topit nereacționat, care este starea inițială de turnare; termocuplul din partea de jos măsoară starea după terminarea turnării. Formularea acoperirii reactive este foarte specială. Trebuie să se asigure cu exactitate că fierul topit acumulat în compartiment este cu 0.003% mai puțin activ decât fierul topit central. Prin urmare, dacă conținutul inițial de magneziu este prea aproape de punctul de cotitură cu cenușă târâtoare, fierul topit din compartiment va genera fier gri, care va fi măsurat de termocuplul din această zonă. În acest fel, la începutul turnării, atelierul poate adăuga mai mult magneziu pentru a compensa inevitabila pierdere arsă de magneziu.
Dacă termocuplul din partea de jos prezintă o curbă de fier vermiculară, indică faptul că conținutul inițial de magneziu este suficient de mare încât să nu existe grafit în fulgi după terminarea turnării.
Figura 7 este o diagramă de eroziune în secțiune transversală a sondei Xinte după măsurarea eșantionului. În figură, puteți vedea clar zona de partiție, zona principală de eșantionare și tubul de protecție al termocuplului. Deoarece magneziul activ este redus cu 0.003%, în zona de separare se formează matrice de grafit și ferită în formă de D. Mărimea zonei de grafit cu fulgi din partea inferioară reflectă direct conținutul inițial de magneziu din zona principală a eșantionului. Mărimea acestei zone poate fi calculată din căldura degajată în partea de jos. Coeficientul de regresie a varianței dintre eliberarea de căldură și dimensiunea partiției depășește 0.9, ceea ce dovedește că relația dintre cele două este foarte strânsă. Căldura eliberată este obținută prin integrarea în timp a curbei de răcire. Această metodă de măsurare a stării fierului topit la curent și la sfârșitul turnării în același timp asigură precizia conținutului de magneziu înainte de turnare.
Deoarece fierul vermicular este foarte sensibil la agenții sferoidizanți și inoculanți, este imposibil pentru turnătorii să folosească metodele de tratament excesive utilizate în producția de fier gri și fier ductil. Așa cum se arată în Figura 8, datorită sensibilității sale, fierul vermicular este stabil numai într-o fereastră pătrată, nu doar în zona platformei de magneziu. Un proces fiabil de producere a fierului vermicular trebuie să controleze sferoidizarea și inocularea de la început până la sfârșit pentru a se asigura că structura metalografică îndeplinește obiectivul.
Indiferent de cât de mult efort se face, oricât de strictă este gestionarea, fluctuația fierului topit este întotdeauna inevitabilă. Să nu mai vorbim despre cât de corecte știu oamenii despre tratamentul fierului topit, metodele de tratament într-un singur pas, cum ar fi metoda sandwich, nu pot garanta că fiecare tratament va intra în fereastra îngustă de fier vermicular. Numeroase variabile de producție, cum ar fi raportul de amestecare, temperatura cuptorului, timpul de menținere, gradul de preîncălzire a oalei de fier topit, viteza de filetare, poziția de filetare a fierului topit (măsurarea în interiorul sau exteriorul), greutatea fierului topit, starea pungii din aliaj, agentul sferoidizant conținutul real de magneziu de (PeSiMg), dispunerea aliajelor din fiecare strat în metoda sandwich și acoperirea deșeurilor de fier vechi etc. vor afecta toate absorbția magneziului. În plus față de acești factori, conținutul de oxigen activ și sulf activ va schimba, de asemenea, dimensiunea și poziția ferestrei de fier vermicular. Modificările în timpul de ședere al fierului topit în oală, timpul de transport și timpul de turnare vor schimba timpul de ardere disponibil.
Cu toate acestea, cei mai imprevizibili factori de fluctuație sunt erorile operatorilor sau diferențele dintre diferiți operatori datorită obiceiurilor de lucru diferite.
În producția de masă pe scară largă, singura modalitate sigură este de a măsura caracteristicile de solidificare a fierului topit după tratament. În acest fel, diferiți factori care afectează dimensiunea, poziția și absorbția aliajelor ferestrei de fier vermicular au fost măsurate, analizate și luate în considerare în mod cuprinzător. Apoi se poate adăuga cantitatea adecvată de magneziu și inoculant. Fiecare oală de fier topit este turnată după ce a fost actualizată la o stare ideală. Această metodă de control al procesului de măsurare și reglare în doi pași minimizează variabilitatea producției și elimină complet riscul de grafit fulg în turnare.
Controlul procesului de producție a fierului vermicular cu oală din metal fierbinte
Așa cum se arată în Figura 9, controlul procesului începe cu analiza termică a fierului topit după tratamentul inițial de sferoidizare și inoculare. Conform rezultatului analizei, mașina de alimentare a firului afișează automat lungimea firului care trebuie adăugat cu magneziu și inoculant și așteaptă ca operatorul să îl pornească. Când linia de alimentare este finalizată, oala este trimisă imediat la linia de turnare. Întregul proces de măsurare și reglare durează aproximativ trei minute. În această perioadă, atelierul poate efectua tratamente convenționale de pre-turnare, cum ar fi îndepărtarea zgurii. Acest lucru asigură continuitatea liniei de turnare.
Din punct de vedere operațional, fierul topit brut nu conține magneziu, iar capacitatea sa de incubație este, de asemenea, foarte limitată. După sferoidizare și inoculare, magneziul și inoculanții mănâncă mai întâi oxigenul activ și sulful din fierul topit, iar apoi „sar” fierul topit într-o anumită poziție de pe tablă. În exemplul din Figura 10, indicele de magneziu și indicele de inoculare a fierului topit sunt 65 și, respectiv, 45. Deoarece parametrii principali de schimbare ai producției de umbre sunt prezentați în fierul topit după măsurare și tratament, rezultatele analizei termice reflectă în mod direct starea actuală a fierului topit. Nu mai rămâne decât să adăugați cantitatea adecvată de magneziu și inoculant pentru a ridica fierul topit din poziția sa actuală la punctul de plecare necesar. În exemplul din Figura 10, se adaugă mai întâi șapte unități de cabluri de magneziu și apoi se adaugă 23 de unități de cabluri inoculante. Relația corespunzătoare dintre unitatea index și lungimea cablului este calibrată în funcție de produs și atelier și este compilată în program. Pe baza experienței anterioare a aproape 100,000 de piese turnate din fier vermicular, cantitatea medie de cablu de magneziu adăugată este de 5 metri pe tonă. Acesta conține 12 grame de magneziu pe metru și calculat la o rată de absorbție de 50%, cantitatea de magneziu adăugată pe tonă de fier topit este de doar 30 de grame. Deoarece cantitatea de adăugare este foarte mică și principalele modificări au avut loc deja în tratamentul inițial, ajustarea este foarte eficientă și fiabilă. După reglare, nu este nevoie să faceți analize termice.
În tratamentul inițial, starea după tratament trebuie să fie mai mică decât poziția inițială de turnare, astfel încât, chiar dacă toți factorii care sunt benefici pentru absorbția magneziului și a inoculantului ating valoarea optimă, fierul topit va ajunge doar la starea inițială de turnare . Cu excepția faptului că nu se tratează excesiv, fierul topit după tratament nu se află în starea fierului gri și a fierului alb. Pentru a face procesul de turnare mai eficient, indicele de magneziu și indicele de inoculare al fiecărei oale de fier topit sunt afișate în diagrama bloc a procesului. Conform tendinței în schimbare a diagramei bloc, operatorul poate regla cantitatea de fier topit adăugată la următoarea oală. Valoarea echivalentă a carbonului este afișată și pe ecran. Aceste date au fost editate și stocate în jurnalul de producție, astfel încât să poată fi urmărite și cuprinzătoare și să îndeplinească și cerințele de asigurare a calității.
Deși analiza termică și ajustările ulterioare pot asigura producția de fier vermicular, se recomandă ca probele să fie prelevate din cupa de spumă a turnării finale pentru analiză. Comparativ cu inspecția convențională a calității, acest rezultat al analizei termice poate oferi analize online și clasifica piesele turnate, dacă este necesar. Simularea pierderii de magneziu în sondă face ca această tehnică de inspecție „nedistructivă” să fie mai eficientă decât metodele metalografice și cu ultrasunete. Deoarece această metodă măsoară o dimensiune mai mare a eșantionului, detectează, de asemenea, modul în care fierul topit se va solidifica în următoarele 10-15 minute.
În concluzie
Alegerea sistemului de control al procesului depinde de produs și de procesul de turnare. La turnarea produselor complexe, cum ar fi capacul motorului din fier vermicular și cilindrul, sistemul trebuie să controleze simultan conținutul de magneziu și inoculant, astfel încât să se afle într-o fereastră foarte îngustă de la începutul până la sfârșitul turnării. Rata de sferoidizare trebuie să fie cuprinsă între 0% și 20% (rata de strângere 80% până la 100%) pentru a asigura cea mai bună turnabilitate, aditivitate mecanică și alte performanțe cuprinzătoare și cea mai bună funcție de utilizare. Pete de grafit fulgi trebuie eliminate complet pentru a preveni defectele și slăbiciunile locale.
Punctul de plecare al oricărui sistem de control al procesului este măsurarea corectă și eficientă a stării fierului topit. Producția fiabilă de fier vermicular la scară largă trebuie să aibă metode de control fezabile pentru a elimina modificările procesului și erorile de funcționare umane. Cel mai eficient mod de a elimina modificările procesului este de a efectua analize termice pe fierul topit după sferoidizare și inoculare. Conform rezultatelor analizei termice, înainte de turnare se adaugă o cantitate exactă de magneziu și inoculant. Această metodă de măsurare și reglare on-line asigură stabilitatea liniei de producție a turnării și elimină diferitele riscuri generate de producția de fier vermicular la scară largă.
Vă rugăm să păstrați sursa și adresa acestui articol pentru reimprimare: Controlul procesului de producție a fierului vermicular
Minghe Compania de turnare sub presiune sunt dedicate fabricării și furnizează piese de turnare de calitate și de înaltă performanță (gama de piese turnate sub presiune din metal include în principal Turnare sub presiune cu perete subțire,Hot Cast casting sub presiune,Turnare sub presiune în cameră rece), Serviciu rotund (Serviciu de turnare sub presiune,Prelucrare Cnc,Fabricarea mucegaiului, Tratament de suprafață). Orice cerință personalizată de turnare sub presiune din aluminiu, magneziu sau turnare sub presiune din Zamak / zinc și alte cerințe de turnare sunt binevenite să ne contacteze.
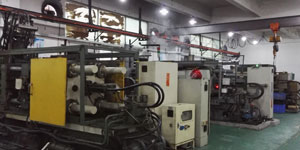
Sub controlul ISO9001 și TS 16949, toate procesele sunt efectuate prin sute de mașini avansate de turnare sub presiune, mașini cu 5 axe și alte facilități, variind de la blastere la mașini de spălat Ultra Sonic. Minghe nu numai că are echipamente avansate, dar are o echipă de ingineri cu experiență, operatori și inspectori pentru a face realitatea designul clientului.
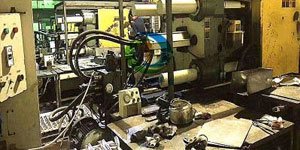
Producător contract de piese turnate sub presiune. Capacitățile includ piese de turnare sub presiune din aluminiu cu cameră rece de la 0.15 lbs. la 6 lbs., schimbare rapidă configurată și prelucrare. Serviciile cu valoare adăugată includ lustruire, vibrare, debavurare, sablare, vopsire, placare, acoperire, asamblare și scule. Materialele lucrate includ aliaje precum 360, 380, 383 și 413.
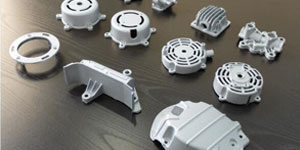
Asistență la proiectarea turnării sub presiune din zinc / servicii de inginerie simultană. Producător personalizat de piese turnate sub presiune din zinc. Pot fi fabricate piese turnate în miniatură, piese turnate sub presiune înaltă, piese turnate multi-glisante, piese turnate convenționale, piese turnate sub formă de unități și piese turnate independente și piese turnate sigilate în cavitate. Piesele turnate pot fi fabricate în lungimi și lățimi de până la toleranță de +/- 24 in.
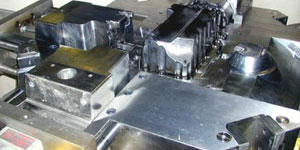
Producător certificat ISO 9001: 2015 de magneziu turnat sub presiune, capabilitățile includ turnare sub presiune cu magneziu de înaltă presiune de până la 200 tone cameră fierbinte și 3000 tone cameră rece, proiectare scule, lustruire, turnare, prelucrare, vopsire cu pulbere și lichide, QA complet cu capacități CMM , asamblare, ambalare și livrare.
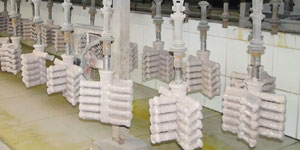
Certificat ITAF16949. Serviciul de turnare suplimentar include investiții de turnătorie,turnare cu nisip,Turnarea gravitației, Pierdere spumă turnare,Turnare centrifugă,Turnarea în vid,Turnare permanentă a matriței, .Capacitățile includ EDI, asistență tehnică, modelare solidă și procesare secundară.
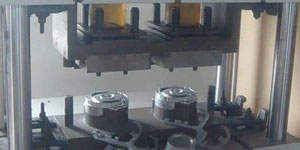
Industrii de turnare Părți Studii de caz pentru: Mașini, biciclete, aeronave, instrumente muzicale, ambarcațiuni, dispozitive optice, senzori, modele, dispozitive electronice, carcase, ceasuri, mașini, motoare, mobilier, bijuterii, jiguri, telecomunicații, iluminat, dispozitive medicale, dispozitive fotografice, Roboți, sculpturi, echipamente de sunet, echipamente sportive, scule, jucării și multe altele.
Ce vă putem ajuta să faceți în continuare?
∇ Accesați pagina principală pentru China turnare sub presiune
→Piese de turnare-Aflați ce am făcut.
→ Ralated Tips About Servicii de turnare sub presiune
By Producător de turnare sub presiune Minghe | Categorii: Articole utile |Material Etichete: Turnare din aluminiu, Turnarea zincului, Turnarea cu magneziu, Turnare cu titan, Turnare din oțel inoxidabil, Turnare din alamă,Turnarea bronzului,Distribuirea videoclipului,Istoricul companiei,Turnare din aluminiu | Comentarii dezactivate