Procesul de producție al tamburului de frână pentru camion
Tamburul de frână este o parte de securitate, se referă la siguranța vieții și a bunurilor umane și, în același timp, este o parte vulnerabilă și consumabilă. Cererea pieței este deosebit de mare.
În prezent, producția anuală internă este de aproximativ 10 milioane sau mai mult. Deoarece structura produsului este relativ simplă, modelarea mașinii și modelarea manuală sunt ușor de utilizat și există turnătorii care produc tamburi de frână în aproape toate părțile țării. Mai multe companii mari pe care le-am vizitat produc tamburi de frână pe o linie de asamblare mecanizată, cu o producție anuală de aproximativ un milion.
Am fost și la câteva companii mici cu o producție anuală de zeci de mii. Există, de asemenea, un parc industrial într-un oraș din județul Longyao, Hebei, unde peste o sută de turnătorii produc intens tamburi de frână pentru automobile; producția de tamburi de frână în întregul district ar trebui să fie mai mare de un milion. Doar că tamburile de frână produse de companiile mari sunt în general furnizate către fabrici de osii interne sau exportate în străinătate, în timp ce majoritatea tamburilor de frână produse de companiile mici sunt furnizate pieței pieselor de schimb și post-vânzare. Calitatea și credibilitatea produselor sale sunt greu de acceptat de fabricile obișnuite de osii. Potrivit acestor companii, am văzut și am învățat, datorită structurilor de produse diferite și a obiectivelor de aprovizionare diferite, procesele de producție sunt diferite, dar, în general, problema calității Există încă multe care nu îndeplinesc cerințele de calitate ale tamburilor de frână auto. Prin urmare, cred că este necesar să discutați și să cercetați procesul de producție a tamburilor de frână cu dvs. și să faceți schimb de experiență unul cu celălalt. Următoarele se bazează pe experiența și înțelegerea mea. Situație, profitați de această ocazie pentru a face schimb de opinii cu dvs., vă rog să mă corectați dacă este greșit.
Cerințe de calitate pentru tamburi de frână pentru camion
Deoarece fonta gri are o conductivitate termică bună, absorbție la șoc, rezistență la uzură, performanță excelentă la turnare și costuri reduse de fabricație, aproape toate tamburile de frână ale autovehiculelor sunt fabricate din fontă gri, iar clasele sunt HT200 și HT250.
În țara mea există un singur standard din fontă gri, care este JB / T9439-2010 și nu există un standard special din fontă gri pentru tamburele de frână ale automobilului. Nu există o descriere a fontei gri speciale în standardul mașinii. În lume, doar Societatea Americană pentru Testare și Materiale ASTMA159-83 (reexaminată în 1993) a formulat standarde special pentru piesele din fier gri pentru automobile. Există 3 categorii de fontă listate pentru tamburul de frână în funcție de capacitatea sa de încărcare. În același timp, cerințele de calitate pentru tamburele de frână din standardul de fontă gri pentru mașinile electrice ale Societății Americane a Inginerilor Automobile SAEJ431 sunt practic aceleași ca ASTMA159-83. În prezent, majoritatea țărilor noastre și a țărilor străine se referă la standardele americane de tambur de frână. Standardul din fabrică este dat pe desenul sau standardul de acceptare. Nivelul unui standard reflectă nivelul său de măiestrie și calitate. Doar standardele la nivel înalt pot produce produse de înaltă calitate.
Următoarele introduc pe scurt standardele americane menționate mai sus și cerințele de calitate ale unor companii străine bune pe tamburi de frână și introduce următoarele pentru referință
Proprietăți mecanice
Calitate | Rezistența la tracțiune (MPa) | Duritate (HB) |
G2500a |
175 |
170-229 |
G3500b |
245 |
207-255 |
G3500c |
245 |
207-255 |
Compoziție chimică
Calitate | Total C |
Si |
Mn |
P |
s |
Alte elemente de aliere |
G2500a |
≥ 3.40 |
1.60-2.10 |
0.60-0.90 |
≤ 0.15 |
≤ 0.12 |
După cum este necesar |
G3500b |
≥ 3.40 |
1.30-1.80 |
0.60-0.90 |
≤ 0.15 |
≤ 0.12 |
|
G3500c |
≥ 3.50 |
1.30-1.80 |
0.60-0.90 |
≤ 0.15 |
≤ 0.12 |
Notă:
- C total este o cerință obligatorie și trebuie garantat
- Alte elemente precum Cr, Cu, Sn sunt utilizate în principal pentru a asigura proprietăți mecanice și duritate.
- G2500a este utilizat în camioanele cu sarcini medii, G3500b este utilizat în camioanele pentru vehicule grele, iar G3500c este utilizat în camioanele super-grele.
Microstructură
Calitate | Tip grafit | Shi Chang | Hipokeimenon |
G2500a |
A |
2-4 |
Perlită lamelară, ferită <15% |
G3500b |
A |
3-5 |
Perlită stratificată, ferită + cementită <5% |
G3500c |
A |
3-5 |
Perlită stratificată, ferită + cementită <5% |
alte cerințe legate de
În plus față de acceptarea proprietăților mecanice, a durității și a metalografiei, producătorii străini și OEM-urile interne prezintă deseori cerințe de compacitate în condițiile tehnice ale tamburilor de frână furnizate.
Dacă există găuri de contracție, porozitate de contracție, pori, incluziuni de nisip sau alte defecte de turnare în piesele turnate, acestea nu sunt dense. Aceste defecte pot fi verificate prin raze X sau prin metode anatomice. Dacă defectele sunt mai mici decât cele specificate în tabelul următor, acesta poate fi acceptat. Depășirea reglementărilor sale va fi considerată resturi. Desigur, dacă defectul a fost expus în timpul prelucrării, în general nu este acceptat.
- ASTME446-98 Calitatea internă a tamburului de frână este nivelul defectului testat la X.
- Zona densă avansată, gradul de primire este A3, B3, C2
- În general zonă densă, nivelul de recepție este A3, B4, C3
- Notă: A înseamnă stomate, A3 înseamnă că nivelul de acceptare al stomatelor este 3
- B reprezintă nisip și incluziunile B4 reprezintă nivelul de acceptare a incluziunilor de nisip este nivelul 4
- C înseamnă porozitatea de contracție C3 înseamnă porozitatea de contracție nivelul de acceptare este 3
Moduri de avarie și cauze ale tamburilor de frână
Defecțiunea tamburului de frână în timpul utilizării este în principal fisurare și abraziune, dar din datele statistice reflectate în reclamațiile și reclamațiile clienților, aceasta este în principal prima. Adică, majoritatea tamburilor de frână defecte sunt sub uzură normală sau chiar ușoară, adică au crăpat și nu pot fi utilizate. Următoarele sunt resturile returnate de o fabrică în 2014. Se poate vedea clar din imagine că una până la mai multe fisuri longitudinale sunt generate în tamburul de frână. Fisurile transversale apar în cea mai mare parte la colțurile rotunjite ale flanșei, cunoscute în mod obișnuit ca picătură superioară.
Din analiza eșecului părților eșuate, se concluzionează că există trei motive principale pentru eșec:
- Proprietățile mecanice ale corpului de turnare sunt mai mici decât cerințele normale
- Există defecte de turnare în interiorul turnării, în special porozitatea de contracție la colțurile rotunjite ale flanșei.
- Mașina este grav supraîncărcată, frânează frecvent și este pulverizată cu apă în timpul procesului de frânare, iar proprietățile mecanice și metalografia acestor piese defecte sunt verificate pentru a îndeplini cerințele produsului.
Primele două cauze ale defecțiunilor ar trebui îmbunătățite de cei dintre noi care producem tamburi de frână. Stabilizați și îmbunătățiți calitatea tamburului de frână. Voi discuta cu dvs. mai detaliat mai jos. În ceea ce privește al treilea motiv al eșecului, suntem neputincioși, bazându-ne în principal pe guvernarea de către stat a utilizării ilegale a vehiculelor supraîncărcate. Din punctul de vedere al revendicărilor, o mare parte din aceasta este cauzată de o astfel de utilizare ilegală. Cu toate acestea, responsabilitatea este în general transferată la turnătorie. Din câte știu, mai multe companii care produc tamburi de frână au susținut un raport de pretenții de aproximativ 3%. În fiecare an sunt milioane de despăgubiri. De fapt, acest tip de responsabilitate ar trebui să fie suportat de proprietarul mașinii. Tamburile de frână exportate din țara noastră în țări străine reflectă în general bine. Aproape niciodată nu există despăgubiri sau chiar reclamații. Tamburele de frână ale autoturismelor și mașinilor transportate în zone simple reflectă, de asemenea, bine. Doar câteva zone montane, zone miniere și produse individuale au o durată de viață scăzută, toate fiind cauzate de suprasolicitarea internă gravă, frânarea frecventă de urgență și pulverizarea apei pentru a răci tamburul de frână în timpul procesului de frânare. În acest caz, toată energia cinetică este convertită în sarcina termică a tamburului de frână, care poate fi măsurată până la 800 ℃ -850 ℃. Acest lucru poate fi găsit și din examinarea macroscopică și metalografică a fisurii de eșec. Acest tip de turnare este macroscopic alb și luminos. Metalografic, este grafit + martensit + bainit. Toate acestea sunt produse prin stingerea austenitei după transformarea la temperaturi ridicate. Prin urmare, tamburul de frână eșuează sub acțiunea stresului de îndoire, a stresului termic și a rezistenței la forța de frânare mecanică în loc de fisurare convențională. Acesta poate fi un mod de eșec în stil chinezesc.
1. Procesul de producție al tamburului de frână
Procesul de producție al tamburilor de frână se concentrează în principal pe două aspecte. Una este modalitatea de a asigura proprietățile sale mecanice și structura metalografică pentru a satisface cerințele produsului. Dar cum să-i reduc defectele de turnare. Mai ales defectele interne ale pieselor cheie. În ceea ce privește reducerea defectelor de turnare, astăzi mă voi concentra asupra modului de a reduce defectele sale de contracție, deoarece este principalul tip de deșeuri și unul dintre principalele motive pentru eșec.
Primul aspect este în principal de a oferi o calitate metalurgică mai bună a fierului topit. Al doilea aspect este de a afla mijloacele tehnologice adecvate producătorului.
În prezent, materialele tamburilor de frână pentru camioane domestice sunt toate HT250, așa că mă voi concentra asupra mai multor aspecte la care trebuie să se acorde atenție în topirea și procesul HT250 utilizat la producerea tamburilor de frână.
Inițial, dacă ar fi nevoie să îndeplinim doar proprietățile mecanice ale HT250 și cerințele structurii metalografice, nu ar exista nicio dificultate. Cu toate acestea, HT250 utilizat în tamburi de frână trebuie să asigure proprietăți mecanice, duritate și structură metalografică sub conținut ridicat de carbon, ceea ce pune unele dificultăți pentru unii producători mici și chiar unii mari. Ei au propus că, dacă conținutul de carbon al produsului trebuie să fie mai mare de 3.40%, fără a adăuga Cr, Cu, Sn și alte elemente de aliere, este dificil să se garanteze performanța. Dar realitatea lor este de a economisi costurile și, în general, adaugă doar Cr și Sn pentru a asigura rezistența la perlit și la tracțiune. Cu toate acestea, dacă cantitatea adăugată este mică, rezistența și duritatea nu vor fi atinse și, dacă cantitatea adăugată este mare, va exista o cantitate excesivă de cementită în metalografie.
Și într-o dilemă. În cele din urmă, pentru a măsura avantajele și dezavantajele, majoritatea adoptă metoda de reducere a conținutului de carbon pentru a îndeplini cerințele de proprietăți mecanice și duritate. Desigur, până acum, deși standardul ASTM a făcut reglementări stricte privind conținutul de C, fabricile chineze nu l-au implementat. Chiar și unii clienți străini nu au cerut în mod uniform ca conținutul de carbon să fie mai mare de 3.4% sau mai mare. De exemplu, mulți clienți pe care îi cunosc, cerințele lor pentru compoziția chimică a tamburilor de frână sunt după cum urmează:
Numele clientului |
C |
Si |
Mn |
P |
s |
Cr |
Cu |
Sn |
TurciaADR ltd |
3.2-3.4 |
2.0-2.4 |
0.7-1.0 |
≤ 0.2 |
≤ 0.1 |
0.15-0.4 |
0.15-0.5 |
≤ 0.12 |
Hyundai 250D |
3.1-3.8 |
1.5-2.5 |
0.4-0.9 |
≤ 0.2 |
≤ 0.1 |
0.15-0.4 |
0.15-0.5 |
≤ 0.12 |
Cu toate acestea, creșterea conținutului total de carbon se bazează științific și este tendința generală, deoarece doar un conținut ridicat de carbon poate garanta o cantitate mare de grafit și poate avea o conductivitate termică și o rezistență termică la oboseală mai bune. Reglementările obligatorii făcute de Statele Unite trebuie să aibă baza sa științifică. Pentru noi, ar trebui să avem și capacitatea de a produce proprietăți mecanice calificate, duritate și structură metalografică sub premisa unui conținut ridicat de carbon.
Prin practica internă a producției de fontă de înaltă rezistență cu conținut ridicat de carbon de-a lungul anilor, ar trebui spus că s-a acumulat multă experiență de succes și s-a obținut un consens în tehnologie. Acest lucru a pus o bază bună pentru producția noastră de tamburi de frână, iar situația reală este, de asemenea, adevărată. Calitatea tamburilor de frână produse de multe întreprinderi mari a reușit să îndeplinească în mod stabil cerințele clienților. Aceste tehnologii, pe scurt, iau drumul fontei sintetice. Tehnologia adoptată se bazează pe proporția ridicată de resturi de oțel adăugate, folosind un reîncărcător pentru a crește reîncărcarea, creșterea sulfului în fierul topit, incubația bună și fierul topit la temperatură suficient de ridicată. Recent, s-a propus pretratarea fierului topit. Am vorbit deja mult despre acest aspect și am publicat multe articole. Nu o voi repeta. Vreau doar să combin turnarea specifică a tamburului de frână și să prezint câteva comentarii pentru referință
2. În ceea ce privește problema concepției
Scopul inoculării fierului lichid al tamburului de frână este același cu cel al producerii altor piese din fontă de înaltă calitate. Ar trebui să se asigure în principal că nu apare cementită sau cantitatea totală de ferită și carbură nu depășește 5% pentru a asigura o formă bună de grafit. (În general, se stipulează că un grafit ar trebui să fie mai mare de 80%. Grafitul B, D, E să nu fie mai mare de 20%) pentru a asigura proprietăți mecanice bune și, în același timp, pentru a îmbunătăți prelucrarea, în practica de producție a griului fonta, inocularea sa este în general de 0.2 Între% -0.6%. Ceea ce vreau să le reamintesc tuturor în acest moment este, vă rugăm să acordați atenție fertilității și să controlați fertilitatea. Deoarece în mintea celor mai mulți tehnicieni și muncitori la turnare la fața locului, cei mai mulți dintre ei sunt preocupați de modul de îmbunătățire a efectului de inoculare, de creșterea miezului de grafit și de modul de utilizare a inoculanților eficienți. Producția de fontă gri este, de asemenea, aceeași cu producția de fontă ductilă. Folosește mai multe inoculări și folosește cât mai mulți inoculanți posibil, ignorând efectul inoculării asupra proprietăților de contracție a fontei gri. Și uitați că cavitățile de contracție și porozitatea au reprezentat o mare parte din produsele reziduale ale tamburului de frână și nu există nicio legătură între produsele reziduale de contracție și defectarea anormală a tamburului de frână.
Știm cu toții că, pe lângă tambururile de frână uzate produse de diverse fabrici, multe piese turnate calificate din depozit au găuri de contracție și defecte de contracție, iar majoritatea tehnicienilor producătorului opresc doar măsurile pentru rezolvarea porozității de contracție. Reduceți temperatura de turnare și îmbunătățiți designul sistemului de turnare. Sunt aici doar să le spun tuturor. O mai mare atenție și control trebuie acordate procesului de incubație a tamburului de frână.
Mulți oameni au realizat acum că inocularea poate favoriza porozitatea contracției. În intervalul de echivalent carbon de 3.9-4.3%, dimensiunea pieselor turnate inoculate este întotdeauna mai mare decât cea a pieselor turnate sterile. Piesele turnate infertile nu au porozitate de contracție, dar piesele turnate inoculate produc retragere slăbită. Prin urmare, la producerea tamburilor de frână, este necesar să se controleze cantitatea de inoculare care să nu fie prea mare. În condiția de a vă asigura că nu apare cementită și de a asigura performanța de prelucrare, încercați să adăugați cât mai puțin inoculant și nu excesiv dacă este suficient. Punctul cheie este de a face bine cu inocularea fluxului. Nu luați două, trei sau chiar patru gestații în timpul procesului.
3. În ceea ce privește etanșeitatea matriței
Cavitatea de contracție internă și porozitatea pieselor turnate din fier și contracția suprafeței pieselor turnate sunt în mare parte afectate de matriță. După turnarea fierului topit în matriță, volumul cavității va muta peretele matriței sub presiunea statică și căldura fierului topit, ceea ce va face ca volumul matriței să devină mai mare, iar dimensiunea turnării va fii în afara toleranței și greutatea va crește. Mărimea deformării depinde de compactitatea matriței de nisip, de materialul de turnare și de parametrii de performanță ai nisipului. Unii oameni din străinătate au făcut cercetări în acest domeniu. Extrag tamburul de frână din linia de producție a matriței, măsoară dimensiunea și cântăresc greutatea acestuia. Rezultatele au arătat că greutatea fiecărei probe fluctuează foarte mult. După cum se arată în figura de mai jos, greutatea tamburului de frână variază de la 162 de lire sterline la 173 de lire sterline, iar diferența maximă este de 11 lire sterline (1 lira este de 453 de grame). Linia de turnare a tamburului de frână de încercare este mașina de turnare sub presiune. Această diferență de greutate indică faptul că calitatea matriței fluctuează. Matrița moale cu impact asupra nisipului a produs o umflare severă a nisipului. Pentru matrițele cu compactitate bună, umflarea este foarte ușoară, iar dimensiunea pieselor turnate este precisă. Au descoperit că tamburul de frână cu umflături severe are contracție în interior, iar calitatea tamburului de frână cu greutate normală este normală. Prin urmare, au folosit această metodă simplă de inspecție pentru a evalua contracția internă a tamburului de frână prin cântărire înainte de a fi transportată la prelucrare și au crezut că contracția tamburului de frână a fost cauzată de mișcarea matriței. Prin urmare, îmbunătățirea rigidității matriței devine o măsură importantă pentru a evita contracția și slăbirea tamburului de frână.
Utilizarea tamburilor de frână acoperite cu nisip de tip fier pentru a produce tamburi de frână promovate acum în China nu are defecte de contracție datorită caracteristicilor sale. O întreprindere de mari dimensiuni din Shanxi care adoptă acest proces pentru a produce tamburi de frână. Au existat trei linii semi-mecanizate de acoperire cu nisip de tip fier, cu mai mult de 430 tamburi de frână Nissan. Rata randamentului procesului este de 90%, iar rata de calificare a produsului este stabilă la 98%. A patra linie de acoperire cu nisip de tip fier este în prezent instalată.
O fabrică din Nanyang, provincia Henan, folosește nisip de rășină pentru a produce tamburi de frână Beiben cu injecție superioară și fără tehnologie de ridicare, cu calitate stabilă și fără contracție.
În unele fabrici, distanța dintre piston și tamburul de frână este prea aproape, care este de 40 mm. Nisipul de turnare aici este dificil de zdrobit, astfel încât găurile de contracție și porozitatea sunt adesea produse aici. Distanța este schimbată la 60-80mm, porozitatea de contracție Este mult mai ușoară.
Unele fabrici mici lovesc mai întâi nisipul în ansamblu, apoi folosesc o tijă de oțel pentru a introduce molidul pentru a face întregul matriță chiar mai strâns și ușor de lovit, reflectând că contracția turnării nu este gravă.
Vă rugăm să păstrați sursa și adresa acestui articol pentru reimprimare: Procesul de producție al tamburului de frână pentru camion
Minghe Compania de turnare sub presiune sunt dedicate fabricării și furnizează piese de turnare de calitate și de înaltă performanță (gama de piese turnate sub presiune din metal include în principal Turnare sub presiune cu perete subțire,Hot Cast casting sub presiune,Turnare sub presiune în cameră rece), Serviciu rotund (Serviciu de turnare sub presiune,Prelucrare Cnc,Fabricarea mucegaiului, Tratament de suprafață). Orice cerință personalizată de turnare sub presiune din aluminiu, magneziu sau turnare sub presiune din Zamak / zinc și alte cerințe de turnare sunt binevenite să ne contacteze.
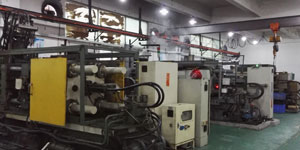
Sub controlul ISO9001 și TS 16949, toate procesele sunt efectuate prin sute de mașini avansate de turnare sub presiune, mașini cu 5 axe și alte facilități, variind de la blastere la mașini de spălat Ultra Sonic. Minghe nu numai că are echipamente avansate, dar are o echipă de ingineri cu experiență, operatori și inspectori pentru a face realitatea designul clientului.
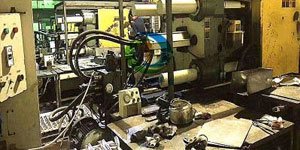
Producător contract de piese turnate sub presiune. Capacitățile includ piese de turnare sub presiune din aluminiu cu cameră rece de la 0.15 lbs. la 6 lbs., schimbare rapidă configurată și prelucrare. Serviciile cu valoare adăugată includ lustruire, vibrare, debavurare, sablare, vopsire, placare, acoperire, asamblare și scule. Materialele lucrate includ aliaje precum 360, 380, 383 și 413.
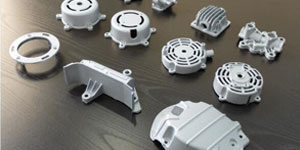
Asistență la proiectarea turnării sub presiune din zinc / servicii de inginerie simultană. Producător personalizat de piese turnate sub presiune din zinc. Pot fi fabricate piese turnate în miniatură, piese turnate sub presiune înaltă, piese turnate multi-glisante, piese turnate convenționale, piese turnate sub formă de unități și piese turnate independente și piese turnate sigilate în cavitate. Piesele turnate pot fi fabricate în lungimi și lățimi de până la toleranță de +/- 24 in.
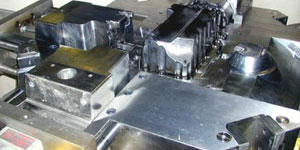
Producător certificat ISO 9001: 2015 de magneziu turnat sub presiune, capabilitățile includ turnare sub presiune cu magneziu de înaltă presiune de până la 200 tone cameră fierbinte și 3000 tone cameră rece, proiectare scule, lustruire, turnare, prelucrare, vopsire cu pulbere și lichide, QA complet cu capacități CMM , asamblare, ambalare și livrare.
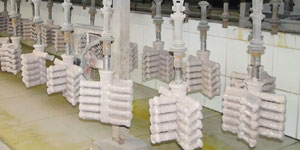
Certificat ITAF16949. Serviciul de turnare suplimentar include investiții de turnătorie,turnare cu nisip,Turnarea gravitației, Pierdere spumă turnare,Turnare centrifugă,Turnarea în vid,Turnare permanentă a matriței, .Capacitățile includ EDI, asistență tehnică, modelare solidă și procesare secundară.
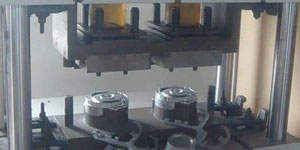
Industrii de turnare Părți Studii de caz pentru: Mașini, biciclete, aeronave, instrumente muzicale, ambarcațiuni, dispozitive optice, senzori, modele, dispozitive electronice, carcase, ceasuri, mașini, motoare, mobilier, bijuterii, jiguri, telecomunicații, iluminat, dispozitive medicale, dispozitive fotografice, Roboți, sculpturi, echipamente de sunet, echipamente sportive, scule, jucării și multe altele.
Ce vă putem ajuta să faceți în continuare?
∇ Accesați pagina principală pentru China turnare sub presiune
→Piese de turnare-Aflați ce am făcut.
→ Ralated Tips About Servicii de turnare sub presiune
By Producător de turnare sub presiune Minghe | Categorii: Articole utile |Material Etichete: Turnare din aluminiu, Turnarea zincului, Turnarea cu magneziu, Turnare cu titan, Turnare din oțel inoxidabil, Turnare din alamă,Turnarea bronzului,Distribuirea videoclipului,Istoricul companiei,Turnare din aluminiu | Comentarii dezactivate