Motivele pentru un conținut excesiv de carbon în producția de piese turnate din spumă
- Selecție nerezonabilă a materialelor de turnare. La selectarea materialului de turnare alb, unul este conținutul ridicat de carbon; cealaltă este densitatea matriței albe este prea mare. Ca rezultat, modelul de turnare are un conținut ridicat de carbon în timpul descompunerii termice în timpul procesului de turnare, iar faza lichidă și conținutul de carbon fără ceață al turnării în timpul procesului de umplere a turnării este ridicat, rezultând o creștere a probabilității de carburare a turnarea oțelului.
- Alegeți spumă sau margele pre-expandate cu conținut redus de carbon pentru a face piese turnate. În prezent, spuma de polistiren EPS produsă intern are un conținut de carbon de 92%; rășina copolimeră de stiren metil metacrilat STMMAC are un conținut de carbon de 69.6%; polimetilmetacrilatul expandabil EPMMA are un conținut de carbon de 60.0%; Utilizarea materialului EPS pentru realizarea matriței de turnare va crește conținutul de carbon al oțelului topit cu 0.1% până la 0.3% în timpul procesului de turnare. Când EPMMA sau STMMA sunt utilizate pentru producerea matriței de turnare, turnarea este cauzată de materialul matriței în timpul procesului de turnare. Creșterea carbonului este mai mică de 0.05%.
- Alegeți densitatea adecvată a spumei pentru a face modelul de turnare. Atunci când asigurați cerințele tehnice ale temperaturii de fabricare a modelului și nu există alte defecte cauzate de calitatea spumei în timpul producției și turnării turnării, cu cât densitatea spumei modelului de turnare este mai mică și cu cât este mai mică spuma, cu atât este mai bună reduce carburarea turnării.
- Îmbunătățiți calitatea producției modelelor de turnare. Atunci când modelul de turnare poate fi realizat în ansamblu, acesta nu trebuie realizat în combinație, iar suprafața de lipire a modelului de turnare trebuie redusă la minimum. Când efectuați lipirea modelului, este necesar să vă asigurați că suprafața de lipire a modelului este netedă și plană, reduceți cantitatea de adeziv utilizată pentru lipire și reduceți cantitatea de produse de descompunere termică a lipiciului pentru a reduce conținutul de carbon al produse de descompunere.
- Folosiți adezivi cu conținut scăzut de carbon sau fără carbon. Adică, adezivul special pentru turnarea și lipirea sub presiune negativă trebuie utilizat pentru lipirea combinată a modelelor, în loc de adezivi obișnuiți de calitate scăzută, cu conținut ridicat de carbon pentru lipire. Și atunci când modelul este combinat și lipit, atunci când se asigură temperatura de lipire și rezistența de lipire a adezivului, cantitatea de adeziv trebuie redusă la minimum pentru a reduce produsele de descompunere termică ale adezivului.
- Alegeți și determinați un sistem de închidere rezonabil. Pentru proiectarea procesului de turnare a pieselor turnate, este necesar să se facă piesele turnate să aibă efectul de a accelera gazificarea materialelor plastice spumate în timpul procesului de turnare și să minimizeze și să eșaloneze timpul de contact și de reacție al fazelor lichide și solide în termic. produse de descompunere, reducând sau evitând astfel Carburarea turnării.
- Alegeți și determinați temperatura adecvată de turnare și viteza de turnare a turnării. Datorită diferitelor forme ale aceleiași turnări, cum ar fi procesul de turnare, temperatura reală de umplere a turnării este complet diferită atunci când oțelul topit este turnat la aceeași temperatură. Dacă temperatura de turnare este crescută, va crește și viteza de turnare, ceea ce va duce la descompunerea termică mai rapidă a modelului de turnare și nu va fi ușor de completat gazificarea, ceea ce va crește cantitatea de produse de descompunere termică în faza lichidă. În același timp, deoarece diferența dintre oțelul topit și model este mică, faza lichidă este După ce a fost stoarsă din spațiu, produsele de descompunere termică sunt adesea stoarse între stratul de acoperire model și metalul topit, sau rece colțuri sau colțuri moarte unde curge oțelul topit, determinând creșterea suprafeței de contact, concentrația de carbon și cantitatea de carburare vor crește, de asemenea. În același timp, acordați o atenție deosebită faptului că, dacă procesul de turnare este nerezonabil, temperatura de turnare a oțelului topit este prea mare și viteza de turnare este prea rapidă, va provoca accidente de producție, cum ar fi gazarea și pulverizarea înapoi.
- Produsul ignifug este adăugat la model pentru a preveni crăparea și arderea modelului la temperatură ridicată, astfel încât să nu producă sau să producă mai puțini produse solide care conțin carbon. Cum ar fi adăugarea de ignifugă 0.5% la 3% parafină clorurată, trifosfat, eter pentabromodifenilic, trioxid de antimoniu, etc. În același timp, adăugați 0.2% la 0.5% peroxid de dibenzoil, peroxid de dilauroil etc. gaz, reducând astfel condițiile și condițiile de carburare în timpul procesului de turnare.
- În procesul de periere a stratului de acoperire tipar, se pot adăuga materiale anti-carburare. Unii catalizatori anti-carburare, cum ar fi sarea de metal alcalin și pulberea de calcar, sunt adăugați în procesul de preparare a stratului de acoperire, astfel încât modelul poate descompune suficient gaz CO și CO2 pentru a absorbi carbonul din stratul de acoperire după turnare, prevenind astfel turnarea din carbon impregnat; sau adăugarea unui oxidant la acoperire pentru a promova transformarea gazului C și H2 după descompunerea termică a modelului în gaz neutru, astfel încât C și H după descompunerea termică pot reduce penetrarea în turnare, provocând creșterea carbonului sau fragilitatea hidrogenului .
După analizarea și rezumarea diferitelor cauze posibile ale conținutului excesiv de carbon în producția de piese turnate din oțel cu conținut scăzut de carbon în spuma pierdută, proiectarea procesului de producție și parametrii tehnici ai producției pieselor turnate din oțel cu conținut scăzut de carbon în spuma pierdută au fost modificate și ajustate pentru a crea un Condițiile rezonabile și fiabile ale tehnologiei de turnare a oțelului cu emisii scăzute de carbon stabilesc modul de funcționare a producției sistemului, astfel încât să se asigure cerințele tehnice pentru producția de produse calificate de turnare din oțel cu emisii scăzute de carbon folosind spumă pierdută.
La ajustarea setărilor parametrilor tehnici ai procesului de control al operației de producție pentru producția de piese turnate din oțel cu emisii reduse de carbon în producția de spumă pierdută, următoarele puncte ar trebui să fie acordate o atenție specială:
- Atunci când se utilizează topirea cu frecvență intermediară, este necesar să se controleze cu strictețe calculul de dozare și operațiile efective de dozare, selecție a materialelor și alimentarea de topire a oțelului carbon. Deoarece calculul ingredientelor este cheia pentru a se asigura că oțelul topit cu compoziție calificată și cel mai mic gaz și incluziuni sunt topite pentru a produce produse de turnare din oțel de înaltă calitate. Acuratețea ingredientelor, selecția și hrănirea este garanția fundamentală pentru calitatea produselor de turnare. Prin urmare, trebuie realizat un sistem strict de subinspecție pentru resturile reciclate. În special, este necesar să se îndepărteze resturile de oțel aliat și resturile de materiale neclare pentru a se asigura că compoziția ingredientelor de topire îndeplinește cerințele parametrilor tehnici ai procesului de turnare, care este prima prioritate în funcționarea și controlul producției de piese turnate din oțel carbon în spuma pierdută.
- Alegeți spumă sau margele pre-expandate cu conținut redus de carbon pentru a face piese turnate. În prezent, spuma de polistiren EPS produsă intern are un conținut de carbon de 92%; rășina copolimer stiren metil metacrilat STMMAC are un conținut de carbon de 69.6%; polimetilmetacrilatul expandabil EPMMA are un conținut de carbon de 60.0%; Utilizarea materialului EPS pentru realizarea matriței de turnare va crește conținutul de carbon al oțelului topit cu 0.1% până la 0.3% în timpul procesului de turnare. Când materialul EPMMA sau STMMA este utilizat pentru producerea matriței de turnare, turnarea este cauzată de materialul matriței în timpul procesului de turnare Creșterea carbonului este mai mică de 0.05%.
- Alegeți densitatea adecvată a spumei pentru a face modelul de turnare. Atunci când asigurați cerințele tehnice ale temperaturii de fabricare a modelului și nu există alte defecte cauzate de calitatea spumei în timpul producției și turnării turnării, cu cât densitatea spumei modelului de turnare este mai mică și cu cât este mai mică spuma, cu atât este mai bună reduce carburarea turnării.
- Îmbunătățiți calitatea producției modelelor de turnare. Atunci când modelul de turnare poate fi realizat în ansamblu, acesta nu trebuie realizat în combinație, iar suprafața de lipire a modelului de turnare trebuie redusă la minimum. Când efectuați lipirea modelului, este necesar să vă asigurați că suprafața de lipire a modelului este netedă și plană, reduceți cantitatea de adeziv utilizată pentru lipire și reduceți cantitatea de produse de descompunere termică a lipiciului pentru a reduce conținutul de carbon al produse de descompunere.
- Folosiți adezivi cu conținut scăzut de carbon sau fără carbon. Adică, lipiciul special pentru turnare și lipire sub presiune negativă trebuie utilizat pentru combinația de modele, în loc de lipici obișnuit de calitate scăzută, cu conținut ridicat de carbon pentru lipire. Și atunci când modelul este combinat și lipit, atunci când se asigură temperatura de lipire și rezistența de lipire a adezivului, cantitatea de adeziv trebuie redusă la minimum pentru a reduce produsele de descompunere termică ale adezivului.
- Alegeți și determinați un sistem de închidere rezonabil. Pentru proiectarea procesului de turnare a pieselor turnate, este necesar să se facă piesele turnate să aibă efectul de a accelera gazificarea materialelor plastice spumate în timpul procesului de turnare și să minimizeze și să eșaloneze timpul de contact și de reacție al fazelor lichide și solide în termic. produse de descompunere, reducând sau evitând astfel Carburarea turnării.
- Alegeți și determinați temperatura adecvată de turnare și viteza de turnare a turnării. Datorită diferitelor forme ale aceleiași turnări, cum ar fi procesul de turnare, temperatura reală de umplere a turnării este complet diferită atunci când oțelul topit este turnat la aceeași temperatură. Dacă temperatura de turnare este crescută, va crește și viteza de turnare, ceea ce va duce la descompunerea termică mai rapidă a modelului de turnare și nu va fi ușor de completat gazificarea, ceea ce va crește cantitatea de produse de descompunere termică în faza lichidă. În același timp, deoarece spațiul dintre oțelul topit și model este mic, lichidul După ce a fost stors din spațiu, produsele de descompunere termică sunt adesea stoarse între stratul de acoperire model și metalul topit, sau colțurile reci sau colțurile moarte în care curge oțelul topit, determinând creșterea suprafeței de contact, concentrația de carbon și cantitatea de carburare vor crește, de asemenea. În același timp, acordați o atenție deosebită faptului că, dacă procesul de turnare este nerezonabil, temperatura de turnare a oțelului topit este prea mare și viteza de turnare este prea rapidă, va provoca accidente de producție, cum ar fi gazarea și pulverizarea înapoi.
- Produsul ignifug este adăugat la model pentru a preveni crăparea și arderea modelului la temperatură ridicată, astfel încât să nu producă sau să producă mai puțini produse solide care conțin carbon. Cum ar fi adăugarea de ignifugă 0.5% la 3% parafină clorurată, trifosfat, eter pentabromodifenilic, trioxid de antimoniu, etc. În același timp, adăugați 0.2% la 0.5% peroxid de dibenzoil, peroxid de dilauroil etc. gaz, reducând astfel condițiile și condițiile de carburare în timpul procesului de turnare.
- În procesul de periere a stratului de acoperire tipar, se pot adăuga materiale anti-carburare. Unii catalizatori anti-carburare, cum ar fi sarea de metal alcalin și pulberea de calcar, sunt adăugați în procesul de preparare a stratului de acoperire, astfel încât modelul poate descompune suficient gaz CO și CO2 pentru a absorbi carbonul din stratul de acoperire după turnare, prevenind astfel turnarea din carbon impregnat; sau adăugarea unui oxidant la acoperire pentru a promova transformarea gazului C și H2 după descompunerea termică a modelului în gaz neutru, astfel încât C și H după descompunerea termică pot reduce penetrarea în turnare, provocând creșterea carbonului sau fragilitatea hidrogenului .
După analizarea și rezumarea diferitelor cauze posibile ale conținutului excesiv de carbon în producția de piese turnate din oțel cu conținut scăzut de carbon în spuma pierdută, proiectarea procesului de producție și parametrii tehnici ai producției pieselor turnate din oțel cu conținut scăzut de carbon în spuma pierdută a fost modificată și ajustată pentru a crea un Condițiile rezonabile și fiabile ale tehnologiei de turnare a oțelului cu emisii scăzute de carbon stabilesc modul de funcționare a producției sistemului, astfel încât să se asigure cerințele tehnice pentru producția de produse calificate de turnare din oțel cu emisii scăzute de carbon folosind spumă pierdută. La ajustarea setărilor parametrilor tehnici ai procesului de control al operației de producție pentru producția de piese turnate din oțel cu emisii reduse de carbon în producția de spumă pierdută, următoarele puncte ar trebui să fie acordate o atenție specială:
- Atunci când se utilizează topirea cu frecvență intermediară, este necesar să se controleze cu strictețe calculul de dozare și operațiile efective de dozare, selecție a materialelor și alimentarea de topire a oțelului carbon. Deoarece calculul ingredientelor este cheia pentru a se asigura că oțelul topit cu compoziție calificată și cel mai mic gaz și incluziuni sunt topite pentru a produce produse de turnare din oțel de înaltă calitate. Acuratețea ingredientelor, selecția și hrănirea este garanția fundamentală pentru calitatea produselor de turnare. Prin urmare, trebuie realizat un sistem strict de subinspecție pentru resturile reciclate. În special, este necesar să se îndepărteze resturile de oțel aliat și resturile de materiale neclare pentru a se asigura că compoziția ingredientelor de topire îndeplinește cerințele parametrilor tehnici ai procesului de turnare, care este prima prioritate în funcționarea și controlul producției de piese turnate din oțel carbon în spuma pierdută.
- Alegeți spumă sau margele pre-expandate cu conținut redus de carbon pentru a face piese turnate. În prezent, spuma de polistiren EPS produsă intern are un conținut de carbon de 92%; rășina copolimer stiren metil metacrilat STMMAC are un conținut de carbon de 69.6%; polimetilmetacrilatul expandabil EPMMA are un conținut de carbon de 60.0%; Utilizarea materialului EPS pentru realizarea matriței de turnare va crește conținutul de carbon al oțelului topit cu 0.1% până la 0.3% în timpul procesului de turnare. Când materialul EPMMA sau STMMA este utilizat pentru producerea matriței de turnare, turnarea este cauzată de materialul matriței în timpul procesului de turnare Creșterea carbonului este mai mică de 0.05%.
- Alegeți densitatea adecvată a spumei pentru a face modelul de turnare. Atunci când asigurați cerințele tehnice ale temperaturii de fabricare a modelului și nu există alte defecte cauzate de calitatea spumei în timpul producției și turnării turnării, cu cât densitatea spumei modelului de turnare este mai mică și cu cât este mai mică spuma, cu atât este mai bună reduce carburarea turnării.
- Îmbunătățiți calitatea producției modelelor de turnare. Atunci când modelul de turnare poate fi realizat în ansamblu, acesta nu trebuie realizat în combinație, iar suprafața de lipire a modelului de turnare trebuie redusă la minimum. Când efectuați lipirea modelului, este necesar să vă asigurați că suprafața de lipire a modelului este netedă și plană, reduceți cantitatea de adeziv utilizată pentru lipire și reduceți cantitatea de produse de descompunere termică a lipiciului pentru a reduce conținutul de carbon al produse de descompunere.
- Folosiți adezivi cu conținut scăzut de carbon sau fără carbon. Adică, adezivul special pentru turnarea și lipirea sub presiune negativă trebuie utilizat pentru lipirea combinată a modelelor, în loc de adezivi obișnuiți de calitate scăzută, cu conținut ridicat de carbon pentru lipire. Și atunci când modelul este combinat și lipit, atunci când se asigură temperatura de lipire și rezistența de lipire a adezivului, cantitatea de adeziv trebuie redusă la minimum pentru a reduce produsele de descompunere termică ale adezivului.
- Alegeți și determinați un sistem de închidere rezonabil. Pentru proiectarea procesului de turnare a pieselor turnate, este necesar să se facă piesele turnate să aibă efectul de a accelera gazificarea materialelor plastice spumate în timpul procesului de turnare și să minimizeze și să eșaloneze timpul de contact și de reacție al fazelor lichide și solide în termic. produse de descompunere, reducând sau evitând astfel Carburarea turnării.
- Alegeți și determinați temperatura adecvată de turnare și viteza de turnare a turnării. Datorită diferitelor forme ale aceleiași turnări, cum ar fi procesul de turnare, temperatura reală de umplere a turnării este complet diferită atunci când oțelul topit este turnat la aceeași temperatură. Dacă temperatura de turnare este crescută, va crește și viteza de turnare, ceea ce va duce la descompunerea termică mai rapidă a modelului de turnare și nu va fi ușor de completat gazificarea, ceea ce va crește cantitatea de produse de descompunere termică în faza lichidă. În același timp, deoarece spațiul dintre oțelul topit și model este mic, lichidul După ce a fost stors din spațiu, produsele de descompunere termică sunt adesea stoarse între stratul de acoperire model și metalul topit, sau colțurile reci sau colțurile moarte în care curge oțelul topit, determinând creșterea suprafeței de contact, concentrația de carbon și cantitatea de carburare vor crește, de asemenea. În același timp, acordați o atenție deosebită faptului că, dacă procesul de turnare este nerezonabil, temperatura de turnare a oțelului topit este prea mare și viteza de turnare este prea rapidă, va provoca accidente de producție, cum ar fi gazarea și pulverizarea înapoi.
- Produsul ignifug este adăugat la model pentru a preveni crăparea și arderea modelului la temperatură ridicată, astfel încât să nu producă sau să producă mai puțini produse solide care conțin carbon. Cum ar fi adăugarea de ignifugă 0.5% la 3% parafină clorurată, trifosfat, eter pentabromodifenilic, trioxid de antimoniu, etc. În același timp, adăugați 0.2% la 0.5% peroxid de dibenzoil, peroxid de dilauroil etc. gaz, reducând astfel condițiile și condițiile de carburare în timpul procesului de turnare.
- În procesul de periere a stratului de acoperire cu model, pot fi adăugate materiale anti-carburare. Adăugați niște catalizatori anti-carburare, cum ar fi sarea de metal alcalin și pulberea de calcar, în timpul procesului de preparare a vopselei model, astfel încât modelul să poată descompune suficient gaz CO și CO2 pentru a absorbi carbonul în stratul de vopsea după turnare, prevenind astfel turnarea de la pătrundere. Carbon; sau adăugarea unui oxidant la acoperire pentru a promova transformarea gazului C și H2 după descompunerea termică a modelului în gaz neutru, astfel încât C și H după descompunerea termică pot reduce penetrarea în turnare, provocând creșterea carbonului sau fragilitatea hidrogenului .
- Controlați strict calitatea tratamentului de reciclare a nisipului. Asigurați-vă că producția și utilizarea nisipului de turnare îndeplinesc cerințele parametrilor tehnici ai procesului, în special conținutul de praf din nisipul de turnare trebuie să fie strict controlat pentru a preveni reducerea permeabilității la aer a cutiei de nisip de turnare din cauza prafului, cauzând produsele de descompunere termică ale modelului de turnare să nu poată fi descărcate din timp în cavitatea de turnare și să mărească rata de recarburare a pieselor turnate.
- Atunci când sunt produse și turnate piese turnate din oțel cu emisii reduse de carbon, vidul balonului de turnare trebuie mărit. Cutia de nisip de turnare ar trebui să adopte structura aspirării peretelui cutiei. La turnare, aspirarea pereților cutiei poate accelera evacuarea produselor de descompunere termică către exteriorul cavității matriței, reducând astfel concentrația și timpul de contact al produselor de descompunere termică ale modelului și reducând sau evitând oțelul turnat Carburarea și depunerea carbonului a pieselor . Când dimensiunea nisipului de turnare este între 20 ochiuri și 40 ochiuri, 0.03MPa ~ 0.06MPa este adecvat la turnarea pieselor turnate din oțel. Dacă presiunea negativă este prea mare, aceasta va provoca lipirea nisipului și alte defecte la turnare.
- Pentru turnarea pieselor turnate din oțel cu conținut scăzut de carbon, metoda de turnare inferioară ar trebui utilizată cât mai mult posibil pentru a face fluxul de umplere al oțelului topit neted, iar produsele de descompunere termică ale modelului pot pătrunde lin în cavitatea sau colectorul de colectare a zgurii, astfel reducerea și reducerea descompunerii termice a modelului Timpul de reacție de contact al fazei lichide și al fazei solide din produs reduce și elimină probabilitatea creșterii carbonului. Utilizarea sistemului de turnare a ploii pentru turnarea pieselor turnate din oțel cu conținut scăzut de carbon va crește condițiile de lucru și condițiile de carburare, carburare și depunerea de carbon a pieselor turnate și va provoca defecte grave în piesele turnate și nu sunt adecvate pentru utilizare.
Vă rugăm să păstrați sursa și adresa acestui articol pentru reimprimare: Motivele pentru un conținut excesiv de carbon în producția de piese turnate din spumă
Minghe Compania de turnare sub presiune sunt dedicate fabricării și furnizează piese de turnare de calitate și de înaltă performanță (gama de piese turnate sub presiune din metal include în principal Turnare sub presiune cu perete subțire,Hot Cast casting sub presiune,Turnare sub presiune în cameră rece), Serviciu rotund (Serviciu de turnare sub presiune,Prelucrare Cnc,Fabricarea mucegaiului, Tratament de suprafață). Orice cerință personalizată de turnare sub presiune din aluminiu, magneziu sau turnare sub presiune din Zamak / zinc și alte cerințe de turnare sunt binevenite să ne contacteze.
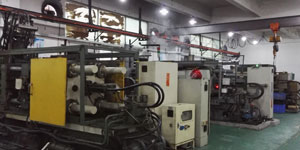
Sub controlul ISO9001 și TS 16949, toate procesele sunt efectuate prin sute de mașini avansate de turnare sub presiune, mașini cu 5 axe și alte facilități, variind de la blastere la mașini de spălat Ultra Sonic. Minghe nu numai că are echipamente avansate, dar are o echipă de ingineri cu experiență, operatori și inspectori pentru a face realitatea designul clientului.
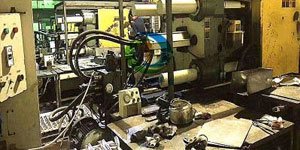
Producător contract de piese turnate sub presiune. Capacitățile includ piese de turnare sub presiune din aluminiu cu cameră rece de la 0.15 lbs. la 6 lbs., schimbare rapidă configurată și prelucrare. Serviciile cu valoare adăugată includ lustruire, vibrare, debavurare, sablare, vopsire, placare, acoperire, asamblare și scule. Materialele lucrate includ aliaje precum 360, 380, 383 și 413.
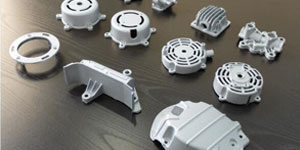
Asistență la proiectarea turnării sub presiune din zinc / servicii de inginerie simultană. Producător personalizat de piese turnate sub presiune din zinc. Pot fi fabricate piese turnate în miniatură, piese turnate sub presiune înaltă, piese turnate multi-glisante, piese turnate convenționale, piese turnate sub formă de unități și piese turnate independente și piese turnate sigilate în cavitate. Piesele turnate pot fi fabricate în lungimi și lățimi de până la toleranță de +/- 24 in.
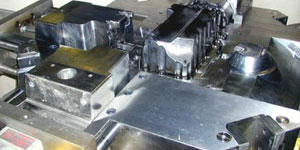
Producător certificat ISO 9001: 2015 de magneziu turnat sub presiune, capabilitățile includ turnare sub presiune cu magneziu de înaltă presiune de până la 200 tone cameră fierbinte și 3000 tone cameră rece, proiectare scule, lustruire, turnare, prelucrare, vopsire cu pulbere și lichide, QA complet cu capacități CMM , asamblare, ambalare și livrare.
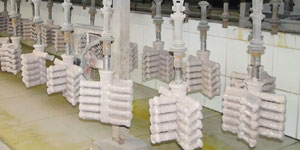
Certificat ITAF16949. Serviciul de turnare suplimentar include investiții de turnătorie,turnare cu nisip,Turnarea gravitației, Pierdere spumă turnare,Turnare centrifugă,Turnarea în vid,Turnare permanentă a matriței, .Capacitățile includ EDI, asistență tehnică, modelare solidă și procesare secundară.
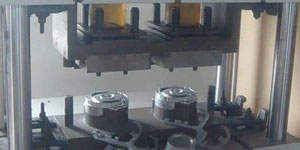
Industrii de turnare Părți Studii de caz pentru: Mașini, biciclete, aeronave, instrumente muzicale, ambarcațiuni, dispozitive optice, senzori, modele, dispozitive electronice, carcase, ceasuri, mașini, motoare, mobilier, bijuterii, jiguri, telecomunicații, iluminat, dispozitive medicale, dispozitive fotografice, Roboți, sculpturi, echipamente de sunet, echipamente sportive, scule, jucării și multe altele.
Ce vă putem ajuta să faceți în continuare?
∇ Accesați pagina principală pentru China turnare sub presiune
→Piese de turnare-Aflați ce am făcut.
→ Ralated Tips About Servicii de turnare sub presiune
By Producător de turnare sub presiune Minghe | Categorii: Articole utile |Material Etichete: Turnare din aluminiu, Turnarea zincului, Turnarea cu magneziu, Turnare cu titan, Turnare din oțel inoxidabil, Turnare din alamă,Turnarea bronzului,Distribuirea videoclipului,Istoricul companiei,Turnare din aluminiu | Comentarii dezactivate