Cum se îmbunătățește măsurile procesului de turnare a ratei de sferoidizare
Nivelul de sferoidizare a pieselor turnate din fontă obișnuită din grafit sferoidal este necesar pentru a atinge nivelul 4 sau mai mare (adică rata de sferoidizare este de 70%), rata de sferoidizare realizată de turnătoria generală este de aproximativ 85%. În ultimii ani, odată cu dezvoltarea producției de fontă nodulară, în special în industriile cu cerințe ridicate pentru producția de turnare a energiei eoliene și calitatea turnării, este necesar ca nivelul de sferoidizare să atingă nivelul 2, adică rata de sferoidizare atinge peste 90%. Compania autorului a analizat și îmbunătățit procesul de sferoidizare și inoculare utilizat în QT400-15, precum și agentul de sferoidizare și inoculant, astfel încât rata de sferoidizare a fontei nodulare a ajuns la mai mult de 90%.
1. Procesul de producție original
Procesul de producție original:
- Echipamentul de topire adoptă un cuptor cu frecvență intermediară de 2.0 T și un cuptor cu frecvență industrială de 1.5 T;
- Compoziția lichidului de fier brut QT400-15 este ω (C) = 3.75% ~ 3.95%, ω (Si) = 1.4% ~ 1.7%, ω (Mn) ≤0.40%, ω (P) ≤0.07%, ω ( S)) ≤0.035%;
- Agentul de sferoidizare utilizat în tratamentul de sferoidizare este de 1.3% până la 1.5% aliaj RE3Mg8SiFe;
- Inoculantul utilizat în tratamentul de inoculare este 0.7% ~ 0.9% aliaj 75SiFe-C. Tratamentul sferoidizant adoptă două metode de bătaie și spălare:
În primul rând, se produce 55% ~ 60% din fier, apoi se efectuează sferoidizarea, apoi se adaugă inoculant și apoi se adaugă restul lichidului de fier.
Datorită metodei tradiționale de sferoidizare și inoculare, rata de sferoidizare detectată de un singur bloc de testare cu o grosime de 25 mm este în general de aproximativ 80%, adică nivelul de sferoidizare este al treilea.
2. Planul de testare pentru îmbunătățirea ratei de sferoidizare
Pentru a crește rata de sferoidizare, s-a îmbunătățit procesul original de sferoidizare și inoculare. Principalele măsuri sunt: creșterea cantității de agent sferoidant și inoculant, purificarea fierului topit și tratamentul desulfurant. Rata de sferoidizare este încă testată cu un singur bloc de testare cu pană turnată de 25 mm. Planul specific este următorul:
- (1) Analizați motivul ratei scăzute de sferoidizare a procesului original. S-a crezut că cantitatea de agent de sferoidizare a fost mică, astfel încât cantitatea de agent de sferoidizare adăugată a crescut de la 1.3% la 1.4% la 1.7%, dar rata de sferoidizare nu a îndeplinit cerințele. . (2) O altă presupunere este că rata scăzută de sferoidizare poate fi cauzată de o gestație slabă sau de scăderea fertilității. Prin urmare, experimentul a crescut doza de inoculare de la 0.7% la 0.9% la 1.1%, iar rata de sferoidizare nu a îndeplinit cerințele.
- (3) Continuați să analizați și să credeți că există mai multe incluziuni în fierul topit și elementele de interferență cu sferoidizare ridicată pot fi cauza ratei scăzute de sferoidizare. Prin urmare, se efectuează purificarea la temperatură ridicată a fierului topit. Temperatura de purificare la temperatură ridicată este în general controlată la 1500 ± 10 ° C, dar rata sa de sferoidizare nu a depășit 90%.
- (4) Cantitatea mare de ω (S) consumă serios doza de sferoidizare și accelerează declinul sferoidizării. Prin urmare, tratamentul de desulfurare este crescut pentru a reduce cantitatea originală de lichid de fier ω (S) de la 0.035% la mai puțin de 0.020%, dar rata de sferoidizare este de asemenea atinsă doar la 86%. Rezultatele testelor celor patru scheme de mai sus sunt prezentate în tabelul 1. Structura și proprietățile mecanice ale blocului de testare în formă de pană nu au îndeplinit cerințele.
3. Ultimul plan de îmbunătățire adoptat
3.1 Măsuri de îmbunătățire specifice
- Materiile prime sunt fonta brută, resturi ne ruginite sau mai puțin ruginite și materiale de reîncălzire;
- Desulfurarea fierului topit brut prin adăugarea de cenușă sodică (Na2CO3) în cuptor;
- Folosiți agent de pretratare Foseco 390 pentru pre-dezoxidare în pungă;
- Tratament de sferoidizare cu Fozco Nodulizer;
- Folosind inoculare combinată cu carbură de siliciu și ferosilicon.
Controlul original al compoziției fierului topit pentru noul proces: ω (C) = (3.70% ~ 3.90%, ω (Si) = 0.80% ~ 1.20% [turnare ω (Si final) = 2.60% ~ 3.00%], ω ( Mn) ≤ 0.30%, ω (P) ≤0.05%, ω (S) ≤0.02%. Când fierul topit original ω (S) depășește 0.02%, sodă industrială este utilizată pentru desulfurare în fața cuptorului, deoarece reacția de desulfurare este o reacție endotermică, temperatura de desulfurare trebuie controlată la aproximativ 1500 ° C, iar cantitatea de sodă adăugată este controlată la 1.5% ~ 2.5% în funcție de cantitatea de ω (S) în timpul topirii în cuptor .
În același timp, pachetul de tratament sferoidizant adoptă un pachet obișnuit de tratament de tip baraj. Mai întâi, adăugați 1.7% din agentul sferoidizant al mărcii Foseco NODALLOY7RE pe partea laterală a barajului din partea de jos a ambalajului, aplatizați și compactați și utilizați 0.2% carbură de siliciu pulbere și 0.3% mici. , și după tamponare, este acoperit cu un fier sub presiune și se adaugă 75% inoculant Foseke 0.3 pe cealaltă parte a oalei de fier topit. La bătaia fierului, 390% ~ 55% din volumul total de fier topit este mai întâi spălat. După finalizarea reacției de sferoidizare, se adaugă 60% inoculant 1.2SiFe-C și fierul topit rămas este spălat și zgura este turnată.
3.2 Rezultatele testelor
Compoziția fierului topit original înainte și după desulfurare, proprietățile mecanice și structura metalografică a blocului de testare în formă de pană de 25 mm, și metoda de evaluare a ratei de sferoidizare în structura metalografică sunt detectate automat de sistemul de analiză a imaginii .
4. Analiza rezultatelor
4.1 Influența elementelor principale asupra ratei de sferoidizare
- C, Si: C poate promova grafitizarea și reduce tendința gurii albe, dar o cantitate mare de ω (C) va face CE prea mare și va provoca cu ușurință plutirea grafitului, controlată în general la 3.7% ~ 3.9%. Si poate întări capacitatea de grafitizare și poate elimina cementita. Când se adaugă Si ca inoculant, poate reduce foarte mult capacitatea de răcire a fierului topit. Pentru a îmbunătăți efectul de inoculare, cantitatea de ω (Si) din fierul topit original a fost redusă de la 1.3% la 1.5% la 0.8% până la 1.2%, iar cantitatea de ω (Si final) a fost controlată de la 2.60% la 3.00%.
- Mn: În timpul procesului de cristalizare, Mn crește tendința fontei de a se răci și favorizează formarea de carburi (FeMn) 3C. În procesul de transformare eutectoidă, Mn reduce temperatura de transformare a eutectoidului, stabilizează și rafinează perlita. Mn nu are mare influență asupra ratei de sferoidizare. Datorită influenței materiilor prime, în general se controlează ω (Mn) <0.30%.
- P: Când ω (P) <0.05%, este solubil în Fe și este dificil să se formeze un eutectic cu fosfor, care are un efect redus asupra ratei de sferoidizare a fierului ductil.
- S: S este un element de desferoidizare. S consumă Mg și RE în agentul de sferoidizare în timpul reacției de sferoidizare, împiedicând grafitizarea și reducând rata de sferoidizare. Zgura sulfuroasă se va întoarce la sulf înainte ca fierul topit să se solidifice, consumând din nou elemente sferoidizante, accelerând declinul sferoidizării și afectând în continuare rata de sferoidizare. Pentru a obține o rată ridicată de sferoidizare, cantitatea de ω (S) din fierul brut ar trebui redusă la mai puțin de 0.02%.
4.2 Tratamentul de desulfurare
După ce sarcina este topită, luați probe și analizați compoziția chimică. Când cantitatea de ω (S) este mai mare de 0.02%, este necesară desulfurarea.
Principiul desulfurării cenușii sodice este: puneți o anumită cantitate de cenușă sodică în oală, folosiți fluxul de fier topit pentru a spăla și amesteca, cenușa sodică se descompune la temperatură ridicată, formula de reacție este Na2CO3 = Na2O + CO2 ↑: Na2O generat este în fierul topit din nou Sulfurarea și formarea Na2S, (Na2O) + [FeS] = (Na2S) + (FeO).
Na2CO3 separă și rezolvă CO2, provocând o agitație violentă a fierului topit, care promovează procesul de desulfurare. Zgura de sodă este ușor să curgă și să plutească rapid, iar timpul de reacție de desulfurare este foarte scurt. După desulfurare, zgura trebuie îndepărtată la timp, altfel va reveni la sulf. 4.3 Tratament de pre-deoxidare, tratament de sferoidizare și tratament de inoculare Agentul de pretratare Foseke 390 joacă rolul tratamentului de pre-deoxidare în pungă și, în același timp, mărește nucleul de nucleație a grafitului și numărul de sfere de grafit pe unitatea de suprafață și poate, de asemenea, crește rata de absorbție a Mg. Îmbunătățiți semnificativ capacitatea de a rezista recesiunii și creșteți rata de sferoidizare. Inoculantul Fochke conține ω (Si) = 60% ~ 70%, ω (Ca) = 0.4% ~ 2.0%, ω (Ba) = 7% ~ 11%, din care Ba poate prelungi timpul efectiv de incubație. Este selectat gradul NODALLOY7RE al Nodulizatorului Fozco, iar its (Si) = 40% ~ 50%, ω (Mg) = 7.0% ~ 8.0%, ω (RE) = 0.3% ~ 1.0%, ω (Ca) = 1.5 % ~ 2.5%, ω (Al) <1.0%. Deoarece fierul topit suferă tratamente de desulfurare și pre-deoxidare, elementele care consumă nodulizatori în fierul topit sunt foarte reduse, astfel încât un nodulizator cu o cantitate mică de ω (RE) este selectat pentru a reduce deteriorarea morfologiei grafitului sferoidal ; Principalul element de acțiune este Mg; Ca și Al pot juca un rol în întărirea incubației. Folosind tratamentul de inoculare combinat cu carbură de siliciu și ferosilicon, punctul de topire al carburii de siliciu este de aproximativ 1600 ° C, iar nucleul cristalului de grafit este crescut în timpul solidificării, iar dozele mari de ferosilicon sunt utilizate pentru inoculare, ceea ce poate preveni scăderea sferoidizării.
5 Concluzie
În producția de fontă nodulară feritică, când este necesară o rată de sferoidizare mai mare de 90%, pot fi adoptate următoarele măsuri:
- (1) Alegeți o încărcare de înaltă calitate pentru a reduce elementele de de-sferoidizare din încărcare.
- (2) Alegeți un agent sferoidizant cu o cantitate redusă de ω (RE) pentru a reduce efectul deteriorării RE asupra morfologiei grafitului sferoidal.
- (3) Conținutul de ω (S) al fierului topit original ar trebui să fie mai mic de 0.020%, ceea ce poate reduce consumul de nodulizatori, în special elementele nodulizate consumate prin sulfurarea secundară a zgurii sulfurate.
- (4) Pre-dezoxidați fierul topit, creșteți numărul de sfere de grafit pe unitate de suprafață, creșteți rata de sferoidizare, îmbunătățiți foarte mult capacitatea de a rezista recesiunii și extindeți timpul efectiv de incubație.
- (5) Reduceți cantitatea de ω (Si) în fierul topit original, creșteți cantitatea de agent sferoidant, inoculant și diferiți agenți de pretratare și întăriți tratamentul de inoculare.
Vă rugăm să păstrați sursa și adresa acestui articol pentru reimprimare: Cum se îmbunătățește măsurile procesului de turnare a ratei de sferoidizare
Minghe Compania de turnare sub presiune sunt dedicate fabricării și furnizează piese de turnare de calitate și de înaltă performanță (gama de piese turnate sub presiune din metal include în principal Turnare sub presiune cu perete subțire,Hot Cast casting sub presiune,Turnare sub presiune în cameră rece), Serviciu rotund (Serviciu de turnare sub presiune,Prelucrare Cnc,Fabricarea mucegaiului, Tratament de suprafață). Orice cerință personalizată de turnare sub presiune din aluminiu, magneziu sau turnare sub presiune din Zamak / zinc și alte cerințe de turnare sunt binevenite să ne contacteze.
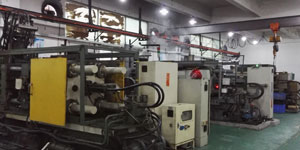
Sub controlul ISO9001 și TS 16949, toate procesele sunt efectuate prin sute de mașini avansate de turnare sub presiune, mașini cu 5 axe și alte facilități, variind de la blastere la mașini de spălat Ultra Sonic. Minghe nu numai că are echipamente avansate, dar are o echipă de ingineri cu experiență, operatori și inspectori pentru a face realitatea designul clientului.
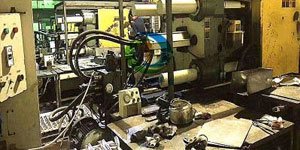
Producător contract de piese turnate sub presiune. Capacitățile includ piese de turnare sub presiune din aluminiu cu cameră rece de la 0.15 lbs. la 6 lbs., schimbare rapidă configurată și prelucrare. Serviciile cu valoare adăugată includ lustruire, vibrare, debavurare, sablare, vopsire, placare, acoperire, asamblare și scule. Materialele lucrate includ aliaje precum 360, 380, 383 și 413.
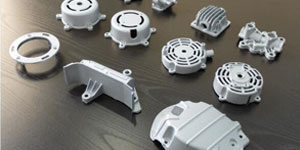
Asistență la proiectarea turnării sub presiune din zinc / servicii de inginerie simultană. Producător personalizat de piese turnate sub presiune din zinc. Pot fi fabricate piese turnate în miniatură, piese turnate sub presiune înaltă, piese turnate multi-glisante, piese turnate convenționale, piese turnate sub formă de unități și piese turnate independente și piese turnate sigilate în cavitate. Piesele turnate pot fi fabricate în lungimi și lățimi de până la toleranță de +/- 24 in.
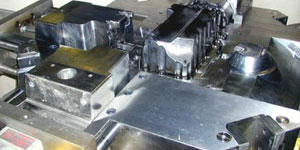
Producător certificat ISO 9001: 2015 de magneziu turnat sub presiune, capabilitățile includ turnare sub presiune cu magneziu de înaltă presiune de până la 200 tone cameră fierbinte și 3000 tone cameră rece, proiectare scule, lustruire, turnare, prelucrare, vopsire cu pulbere și lichide, QA complet cu capacități CMM , asamblare, ambalare și livrare.
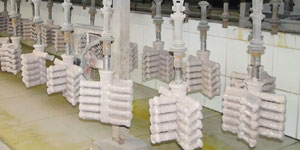
Certificat ITAF16949. Serviciul de turnare suplimentar include investiții de turnătorie,turnare cu nisip,Turnarea gravitației, Pierdere spumă turnare,Turnare centrifugă,Turnarea în vid,Turnare permanentă a matriței, .Capacitățile includ EDI, asistență tehnică, modelare solidă și procesare secundară.
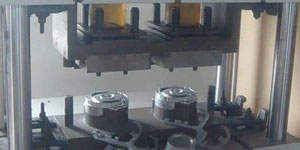
Industrii de turnare Părți Studii de caz pentru: Mașini, biciclete, aeronave, instrumente muzicale, ambarcațiuni, dispozitive optice, senzori, modele, dispozitive electronice, carcase, ceasuri, mașini, motoare, mobilier, bijuterii, jiguri, telecomunicații, iluminat, dispozitive medicale, dispozitive fotografice, Roboți, sculpturi, echipamente de sunet, echipamente sportive, scule, jucării și multe altele.
Ce vă putem ajuta să faceți în continuare?
∇ Accesați pagina principală pentru China turnare sub presiune
→Piese de turnare-Aflați ce am făcut.
→ Ralated Tips About Servicii de turnare sub presiune
By Producător de turnare sub presiune Minghe | Categorii: Articole utile |Material Etichete: Turnare din aluminiu, Turnarea zincului, Turnarea cu magneziu, Turnare cu titan, Turnare din oțel inoxidabil, Turnare din alamă,Turnarea bronzului,Distribuirea videoclipului,Istoricul companiei,Turnare din aluminiu | Comentarii dezactivate