7 Întrebări frecvente în domeniul fabricării matriței
Care este factorul principal care afectează prelucrabilitatea materialului?
Compoziția chimică a oțelului este foarte importantă. Cu cât compoziția aliajului din oțel este mai mare, cu atât este mai dificilă prelucrarea. Când conținutul de carbon crește, performanța de tăiere a metalului scade.
Structura oțelului este, de asemenea, foarte importantă pentru performanța de tăiere a metalelor. Diferite structuri includ: forjate, turnate, extrudate, laminate și prelucrate. Forjările și piesele turnate au suprafețe foarte dificile de prelucrat.
Duritatea este un factor important care afectează performanța de tăiere a metalelor. Regula generală este că cu cât oțelul este mai greu, cu atât este mai greu de prelucrat. Oțelul de mare viteză (HSS) poate fi utilizat pentru prelucrarea materialelor cu o duritate de până la 330-400HB; acoperirea cu oțel de mare viteză + TiN poate prelucra materiale cu o duritate de până la 45HRC; iar pentru materialele cu o duritate de 65-70HRC, trebuie să utilizați carbură cimentată, ceramică, cermete și nitrură de bor cubică (CBN).
Incluziunile nemetalice au, în general, un efect negativ asupra duratei de viață a sculei. De exemplu, Al2O3 (alumina), care este o ceramică pură, este foarte abrazivă.
Ultimul este stresul rezidual, care poate cauza probleme de performanță la tăierea metalelor. De multe ori se recomandă efectuarea unui proces de ameliorare a stresului după prelucrarea brută.
Care sunt caracteristicile de tăiere a fontei?
În general vorbind, este:
Cu cât duritatea și rezistența fontei sunt mai mari, cu atât performanțele de tăiere a metalelor sunt mai mici și durata de viață scăzută a lamelor și a tăietorilor este mai mică. Majoritatea tipurilor de fontă utilizate în producția de tăiere a metalelor au, în general, performanțe bune de tăiere a metalelor. Performanța de tăiere a metalelor este legată de structură, iar fonta perlitică mai dură este, de asemenea, mai dificil de prelucrat. Fonta cu grafit fulg și fonta maleabilă au proprietăți excelente de tăiere, în timp ce fonta ductilă este destul de proastă.
Principalele tipuri de uzură întâlnite la prelucrarea fontei sunt: uzura prin abraziune, aderență și difuzie. Abraziunea este cauzată în principal de carburi, particule de nisip și piei turnate dure. Uzura de legătură cu muchia încorporată are loc la o temperatură și viteză de tăiere scăzute. Partea de ferită din fontă este cea mai ușor de sudat pe lamă, dar acest lucru poate fi depășit prin creșterea vitezei de tăiere și a temperaturii.
Pe de altă parte, uzura prin difuzie este dependentă de temperatură și apare la viteze mari de tăiere, mai ales atunci când se utilizează calități de fontă de înaltă rezistență. Aceste clase au o rezistență ridicată la deformare, ceea ce duce la temperaturi ridicate. Această uzură este legată de interacțiunea dintre fontă și unealta de tăiere, ceea ce face ca unele fonte să fie prelucrate cu unelte de tăiere ceramice sau cu nitrură de bor cubică (CBN) la viteze mari pentru a obține o durată de viață bună și o calitate a suprafeței.
În general, proprietățile tipice ale sculelor necesare pentru prelucrarea fontei sunt: duritate termică ridicată și stabilitate chimică, dar este, de asemenea, legată de proces, piesa de prelucrat și condițiile de tăiere; muchia de tăiere trebuie să aibă rezistență, rezistență la oboseală la căldură și rezistență la margine. Gradul de satisfacție al tăierii fontei depinde de modul în care se dezvoltă uzura muchiei: tăietura rapidă înseamnă că fisurile și crăpăturile fierbinți determină ruperea prematură a muchiei de tăiere, deteriorarea piesei, calitatea slabă a suprafeței, ondularea excesivă etc. , echilibrul și muchiile ascuțite sunt ceea ce necesită în general efort.
Care sunt procedurile principale și comune de prelucrare în fabricarea matrițelor?
Procesul de tăiere trebuie împărțit în cel puțin 3 tipuri de procese:
Prelucrare brută, semifinisare și finisare și, uneori, chiar super finisare (în principal aplicații de tăiere cu viteză mare). Frezarea reziduală este desigur pregătită pentru finisare după procesul de semifinare. În fiecare proces, ar trebui depuse eforturi pentru a lăsa o marjă uniform distribuită pentru următorul proces, ceea ce este foarte important. Dacă direcția și volumul de lucru al căii sculei rareori se schimbă rapid, durata de viață a sculei poate fi extinsă și mai previzibilă. Dacă este posibil, procesul de finisare trebuie efectuat pe o mașină-unealtă dedicată. Acest lucru va îmbunătăți precizia geometrică și calitatea matriței într-un timp mai scurt de depanare și asamblare.
Ce fel de instrumente ar trebui utilizate în aceste procese diferite?
Proces de prelucrare dur: freză cu lamă rotundă, freză cu bile și freză cu o rază mare a arcului nasului.
Proces de semifinisare: freză cu pânză rotundă (freză cu pânză rotundă cu un diametru de 10-25 mm), freză cu capăt cu bile.
Proces de finisare: freză cu lamă rotundă, freză cu capăt cu bile.
Proces de frezare reziduală: freză cu pânză rotundă, freză cu capăt cu bile, freză verticală.
Este foarte important să optimizați procesul de tăiere prin selectarea unei combinații de dimensiuni speciale de scule, geometrii și calități, precum și parametri de tăiere și strategii de frezare adecvate.
Pentru instrumentele cu productivitate ridicată care pot fi utilizate, consultați catalogul C-1102: 1 pentru fabricarea matriței
Există unul dintre cei mai importanți factori în procesul de tăiere?
Unul dintre cele mai importante obiective ale procesului de tăiere este de a crea o doză de prelucrare uniform distribuită pentru fiecare sculă din fiecare proces. Aceasta înseamnă că trebuie folosite scule de diferite diametre (de la mari la mici), în special în operații de degroșare și semifinare. Criteriul principal în orice moment ar trebui să fie cât mai aproape de forma finală a matriței în fiecare proces.
Furnizarea de cote de prelucrare distribuite uniform pentru fiecare sculă asigură o productivitate constantă și ridicată și un proces de tăiere sigur. Când ap / ae (adâncimea axială de tăiere / adâncimea radială de tăiere) nu se modifică, viteza de tăiere și viteza de avans pot fi, de asemenea, menținute constant la un nivel ridicat. În acest fel, acțiunile mecanice și modificările sarcinii de lucru pe muchia de tăiere sunt mici, astfel încât căldura și oboseala generate sunt, de asemenea, mai mici, crescând astfel durata de viață a sculei. Dacă procesele ulterioare sunt niște procese de semi-finisare, în special toate procesele de finisare, se poate efectua prelucrare fără pilot sau procesare parțială fără pilot. Cota de prelucrare constantă a materialelor este, de asemenea, standardul de bază pentru aplicațiile de tăiere de mare viteză.
Un alt efect benefic al dozei constante de prelucrare este micul efect advers asupra șinelor de ghidare a mașinii-unelte, șuruburilor cu bile și rulmenților axului.
De ce frezele cu lame rotunde sunt cea mai obișnuită alegere pentru instrumentele de degroșare a matriței?
Dacă se folosește o freză pătrată cu umăr pentru frezarea brută a cavității, o cantitate mare de alocare de tăiere în trepte va fi eliminată în prelucrarea semifinisării. Acest lucru va schimba forța de tăiere și va determina îndoirea sculei. Rezultatul este de a lăsa un nivel de prelucrare inegal pentru finisare, afectând astfel precizia geometrică a matriței. Dacă utilizați o freză pătrată (cu inserție triunghiulară) cu nasul mai slab, aceasta va produce efecte de tăiere imprevizibile. Inserțiile triunghiulare sau diamantate vor produce, de asemenea, forțe de tăiere radiale mai mari și, deoarece numărul muchiilor tăietoare ale inserțiilor este mic, acestea sunt instrumente de degroșare mai puțin economice.
Pe de altă parte, inserția rotundă poate fi frezată în diverse materiale și în toate direcțiile. Dacă se folosește, tranziția între traseele de unelte adiacente este mai ușoară și poate lăsa, de asemenea, o prelucrare mai mică și mai uniformă pentru semi-finisare. marjă. Una dintre caracteristicile lamelor rotunde este că grosimea așchiilor pe care le produc este variabilă. Acest lucru le permite să utilizeze rate de alimentare mai mari decât majoritatea celorlalte inserții.
Unghiul de intrare al inserției rotunde este schimbat de la aproape zero (tăiere foarte superficială) la 90 de grade, iar acțiunea de tăiere este foarte netedă. La adâncimea maximă de tăiere, unghiul de intrare este de 45 de grade. Când tăiați de-a lungul unui perete drept cu un cerc exterior, unghiul de intrare este de 90 de grade. Acest lucru explică, de asemenea, de ce rezistența sculei cu lame rotunde este mare - sarcina de tăiere crește treptat. Degroșarea și semi-degroșarea trebuie să utilizeze întotdeauna freze cu lame rotunde, cum ar fi CoroMill200 (vezi catalogul de fabricație a matrițelor C-1102: 1) ca primă alegere. La tăierea pe 5 axe, inserțiile rotunde sunt foarte potrivite, mai ales că nu are restricții.
Folosind o bună programare, frezele cu inserție rotundă pot înlocui în mare măsură frezele cu bile. Lama rotundă cu curgere mică este combinată cu unghiul de greutate fin, unghiul pozitiv de greblare și geometria de tăiere ușoară și poate fi, de asemenea, utilizat pentru semi-finisare și unele procese de finisare.
Care este viteza efectivă de tăiere (ve) și de ce este întotdeauna foarte importantă pentru calculul de bază al vitezei efective de tăiere pe diametrul efectiv de productivitate ridicată.
Deoarece avansul de masă depinde de viteza de rotație la o anumită viteză de tăiere, dacă viteza efectivă nu este calculată, avansul de masă va fi calculat incorect.
Dacă diametrul nominal al sculei (Dc) este utilizat la calcularea vitezei de tăiere, atunci când adâncimea de tăiere este mică, viteza efectivă sau efectivă de tăiere este mult mai mică decât viteza calculată. Cum ar fi sculele rotunde CoroMill200 (în special în gama de diametre mici), frezele cu bile, frezele cu rază mare a arcului nasului și frezele de capăt CoroMill390 și alte unelte (pentru aceste scule, consultați fabricația matrițelor Sandvik Coromant. Eșantion C-1102: 1 ). Ca urmare, viteza de alimentare calculată este, de asemenea, mult mai mică, ceea ce reduce grav productivitatea. Mai important, condițiile de tăiere ale sculei sunt mai mici decât capacitățile sale și domeniul de aplicare recomandat.
Vă rugăm să păstrați sursa și adresa acestui articol pentru reimprimare:7 Întrebări frecvente în domeniul fabricării matriței
Minghe Compania de turnare sub presiune sunt dedicate fabricării și furnizează piese de turnare de calitate și de înaltă performanță (gama de piese turnate sub presiune din metal include în principal Turnare sub presiune cu perete subțire,Hot Cast casting sub presiune,Turnare sub presiune în cameră rece), Serviciu rotund (Serviciu de turnare sub presiune,Prelucrare Cnc,Fabricarea mucegaiului, Tratament de suprafață). Orice cerință personalizată de turnare sub presiune din aluminiu, magneziu sau turnare sub presiune din Zamak / zinc și alte cerințe de turnare sunt binevenite să ne contacteze.
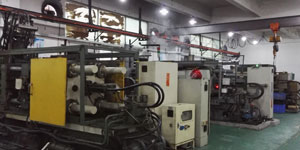
Sub controlul ISO9001 și TS 16949, toate procesele sunt efectuate prin sute de mașini avansate de turnare sub presiune, mașini cu 5 axe și alte facilități, variind de la blastere la mașini de spălat Ultra Sonic. Minghe nu numai că are echipamente avansate, dar are o echipă de ingineri cu experiență, operatori și inspectori pentru a face realitatea designul clientului.
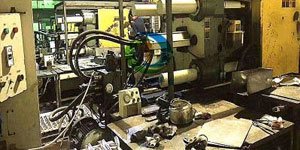
Producător contract de piese turnate sub presiune. Capacitățile includ piese de turnare sub presiune din aluminiu cu cameră rece de la 0.15 lbs. la 6 lbs., schimbare rapidă configurată și prelucrare. Serviciile cu valoare adăugată includ lustruire, vibrare, debavurare, sablare, vopsire, placare, acoperire, asamblare și scule. Materialele lucrate includ aliaje precum 360, 380, 383 și 413.
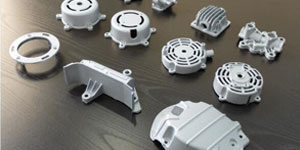
Asistență la proiectarea turnării sub presiune din zinc / servicii de inginerie simultană. Producător personalizat de piese turnate sub presiune din zinc. Pot fi fabricate piese turnate în miniatură, piese turnate sub presiune înaltă, piese turnate multi-glisante, piese turnate convenționale, piese turnate sub formă de unități și piese turnate independente și piese turnate sigilate în cavitate. Piesele turnate pot fi fabricate în lungimi și lățimi de până la toleranță de +/- 24 in.
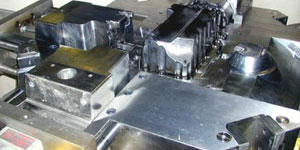
Producător certificat ISO 9001: 2015 de magneziu turnat sub presiune, capabilitățile includ turnare sub presiune cu magneziu de înaltă presiune de până la 200 tone cameră fierbinte și 3000 tone cameră rece, proiectare scule, lustruire, turnare, prelucrare, vopsire cu pulbere și lichide, QA complet cu capacități CMM , asamblare, ambalare și livrare.
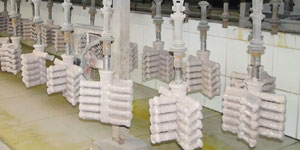
Certificat ITAF16949. Serviciul de turnare suplimentar include investiții de turnătorie,turnare cu nisip,Turnarea gravitației, Pierdere spumă turnare,Turnare centrifugă,Turnarea în vid,Turnare permanentă a matriței, .Capacitățile includ EDI, asistență tehnică, modelare solidă și procesare secundară.
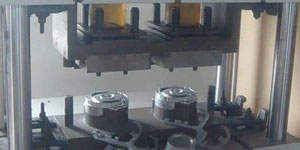
Industrii de turnare Părți Studii de caz pentru: Mașini, biciclete, aeronave, instrumente muzicale, ambarcațiuni, dispozitive optice, senzori, modele, dispozitive electronice, carcase, ceasuri, mașini, motoare, mobilier, bijuterii, jiguri, telecomunicații, iluminat, dispozitive medicale, dispozitive fotografice, Roboți, sculpturi, echipamente de sunet, echipamente sportive, scule, jucării și multe altele.
Ce vă putem ajuta să faceți în continuare?
∇ Accesați pagina principală pentru China turnare sub presiune
→Piese de turnare-Aflați ce am făcut.
→ Ralated Tips About Servicii de turnare sub presiune
By Producător de turnare sub presiune Minghe | Categorii: Articole utile |Material Etichete: Turnare din aluminiu, Turnarea zincului, Turnarea cu magneziu, Turnare cu titan, Turnare din oțel inoxidabil, Turnare din alamă,Turnarea bronzului,Distribuirea videoclipului,Istoricul companiei,Turnare din aluminiu | Comentarii dezactivate