Cercetări privind sistemul de închidere a matriței turnate sub presiune
Turnarea sub presiune este unul dintre mijloacele importante pentru formarea metalelor neferoase. În timpul procesului de turnare sub presiune, datorită diferitelor stări de curgere ale metalului topit în cavitate, pot apărea fenomene nedorite, cum ar fi bariere la rece, tipare, pori și segregare. Pentru a preveni aceste fenomene nedorite, este destul de necesar să se controleze fluxul de metal topit în cavitate. Cheia controlului fluxului de metal topit în cavitate constă în cercetarea și proiectarea sistemului de turnare sub presiune.
Procesul de producție al matrițelor turnate sub presiune
Procesul CAD / CAE / CAM / CAT al fabricarea matrițelor turnate sub presiune.
Proiectarea sistemului de turnare a matriței turnate sub presiune
În cercetarea sistemului de turnare sub presiune, poziția și forma porții sunt factori importanți pentru a controla starea de curgere și direcția de umplere a soluției. În primul rând, concentrați-vă pe locația porții și forma alergătorului, proiectați poarta, alergătorul, sacul de zgură, jgheabul de preaplin și conducta de evacuare; apoi utilizați software-ul CAE pentru a analiza fluxul soluției în interiorul cavității. Poziția și dimensiunea canalului interior și a porții interioare au o influență decisivă asupra metodei de umplere.
Proiectarea Porții Interioare
Când setați poarta pe produsul finit, acesta se efectuează de obicei conform următoarei proceduri:
- Formula de calcul a zonei secțiunii transversale a porții: A = U / (vt): volumul produsului (cIn.) : A: Zona secțiunii transversale a porții (cm2) / v: Viteza soluției de aluminiu a porții (cm / s) / T: Umplere timp (uri)
- Calculați aria secțiunii transversale a porții interioare.
- În funcție de secțiunea transversală a porții interioare, setați forma porții și apoi setați poziția porții și proiectați inițial poziția jgheabului de curgere și a sacului de zgură.
- Faceți diferite scheme de porți (de obicei micșorați mai întâi zona secțiunii transversale a canalului interior și extindeți-o atunci când este necesar după test) și faceți date 3D.
- Efectuați analize CAE (adică analize de flux) pe baza datelor 3D produse.
- Evaluează rezultatele analizei.
- Dacă după evaluare există fenomene nefavorabile, planul ar trebui îmbunătățit, iar apoi analiza CAE ar trebui efectuată până când se obține un plan mai satisfăcător.
Proiectarea sistemelor de evacuare și de evacuare
Poarta interioară trebuie setată într-o poziție în care metalul topit curge cel mai bine în cavitate, evacuarea este umplută și toate colțurile cavității pot fi umplute cu metal topit. Utilizați o poartă internă ori de câte ori este posibil. Dacă sunt necesare mai multe porți interne, trebuie avut grijă ca fluxul de metal topit să nu interfereze unul cu celălalt sau să se întâlnească în cavitate fără a se dispersa (adică ghidarea fluxului de metal pentru a curge într-o direcție) pentru a evita convergența metal topit în vortexul cavității.
Când dimensiunea turnare sub presiune este mare, uneori este imposibil să obțineți secțiunea transversală necesară a alergătorului de la un singur alergător, deci trebuie folosiți alergători multipli. Cu toate acestea, trebuie remarcat faptul că reglajul jgheabului interior ar trebui să asigure că metalul topit este ghidat să curgă numai într-o singură direcție, astfel încât să se evite curenții turbionari atunci când metalul topit din cavitate fuzionează.
Fluxul de metal topit trebuie să se întoarcă cât mai puțin posibil în cavitate, astfel încât metalul topit să poată ajunge în partea cu pereți groși a turnării sub presiune.
Debitul metalului topit trebuie să fie cât mai scurt și uniform posibil.
Zona secțiunii transversale a canalului interior este redusă treptat spre canalul interior pentru a reduce antrenarea gazelor, ceea ce este benefic pentru a îmbunătăți compactitatea turnării sub presiune. Suprafața interioară ar trebui să fie tranziționată ușor în timpul procesului de curgere, pentru a evita cât mai mult posibil rotirea bruscă și impactul de curgere.
Atunci când există mai multe cavități, aria secțiunii transversale a alergătorului trebuie redusă în secțiuni în funcție de raportul de volum al fiecărei cavități.
Aerul din cavitate și gazul volatilizat al lubrifiantului trebuie împinse către canelura de evacuare de către metalul topit care curge, și apoi să scape din cavitate din canelura de evacuare. În special, fluxul de metal topit nu ar trebui să lase gazul în gaura oarbă și să blocheze canalul de evacuare prematur.
Fluxul de metal nu ar trebui să formeze un șoc termic la slaba disipare a căldurii. Pentru piesele turnate cu nervuri, metalul ar trebui să curgă în direcția nervurilor cât mai mult posibil.
Trebuie evitat ca metalul topit să spele direct piesele și nucleele matriței ușor deteriorate. Când este inevitabil, ar trebui să fie setată o zonă de izolare pe molie pentru a evita șocul termic.
În general, cu cât canalul interior este mai larg și mai gros, cu atât este mai mare riscul unui flux neuniform. În același timp, încercați să nu folosiți porți excesiv de groase; evitați deformarea atunci când tăiați porțile.
Epuizarea cavității
Jgheabul de preaplin este utilizat pentru a îndepărta metalul topit pulverizat inițial în timpul turnării și pentru a face temperatura matriței coerentă. Canelura de curgere a lichidului este setată în poziția în care matrița este ușor de conținut gaz și este utilizată pentru gazele de eșapament pentru a îmbunătăți starea de curgere a metalului topit și a ghida metalul topit în toate colțurile cavității pentru a obține o suprafață de turnare bună. . Canelura de evacuare este conectată la partea din față a canelurii de preaplin și a sacului de zgură sau direct conectată la cavitate.
Aria secțiunii transversale totale a fantei de evacuare ar trebui să fie aproximativ echivalentă cu aria secțiunii transversale a canalului interior.
Poziția canelurii de evacuare pe suprafața de despărțire este determinată în funcție de starea de curgere a metalului topit în cavitate. Șanțul de evacuare este cel mai bine să fie „nu drept”, ci „curbat” pentru a preveni metalul topit să stropească și să rănească oamenii. Adâncimea canelurii de evacuare de pe suprafața de despărțire este de obicei de 0.05 mm-0.15 mm; adâncimea canelurii de evacuare din cavitate este de obicei 0.3 mm ~ 0.5 mm; adâncimea canelurii de evacuare de pe marginea matriței este de obicei de 0.1 mm ± 0.15 mm; Lățimea fantei de evacuare este în general de 5 mm ~ 20 mm.
Spațiul de evacuare dintre știftul de ejecție și tija de împingere este foarte important pentru evacuarea cavității, de obicei controlat la 0.01 mm-0.02 mm sau mărit până când nu se produc bavuri.
Eșapamentul cu miez fix este, de asemenea, o metodă eficientă de evacuare. De obicei, un spațiu de 0.05 mm-0.08 mm este controlat la periferia miezului, astfel încât gâtul de poziționare a miezului să fie deschis cu o lățime a fantei de evacuare și grosime de 1 mm-2 mm, iar gazul din cavitate să fie deschis din fantă de evacuare de-a lungul gâtului. Se descarcă din fundul cavității. Rugozitatea fantei de evacuare nu trebuie neglijată. Ar trebui să mențină un grad ridicat de netezime pentru a evita blocarea vopselei lipite de murdărie în timpul utilizării, ceea ce va afecta evacuarea.
Evaluarea analizei fluxului și contramăsuri
În procesul de proiectare a matriței, fluxul metalic ar trebui lăsat să curgă într-o direcție cât mai mult posibil. După ce fluxul este analizat, când curenții turbionari se găsesc în cavitate, unghiul sau dimensiunea plumbului porții interioare ar trebui modificat pentru a elimina starea curentului turbionar.
Când metalul topit se întâlnește, lăsați metalul topit să curgă în continuare pentru o anumită distanță înainte de a opri fluxul; prin urmare, un jgheab de preaplin și o pungă de zgură ar trebui adăugate în afara cavității la joncțiune pentru a permite compușilor topiți de metal topit și aer să curgă în jgheabul de preaplin și punga de zgură; lăsați metalul topit ulterior să fie curat și la temperatura camerei.
Când viteza de umplere a diferitelor părți este diferită, grosimea sau lățimea porții interioare ar trebui să fie ajustată (crește treptat dacă este necesar) pentru a atinge obiectivul de aceeași viteză de umplere, dar ar trebui realizată prin lărgirea canalului interior cât mai mult pe cat posibil.
După analiza debitului, se găsește partea întârziată de umplere și se poate adăuga și un canal interior. Pentru piesele de turnare sub presiune cu pereți subțiri, trebuie selectat un timp de umplere mai scurt pentru turnare sub presiune; prin urmare, timpul de umplere ar trebui redus prin creșterea suprafeței secțiunii transversale a canalului interior pentru a obține o calitate mai bună a suprafeței.
Pentru piesele turnate cu pereți groși care necesită compactitate ridicată, este necesar să se asigure o aerisire eficientă. Pentru turnarea sub presiune trebuie utilizat un timp mediu de umplere. Prin urmare, secțiunea transversală a canalului interior trebuie ajustată pentru a obține timpul de umplere corespunzător și pentru a obține o calitate mai bună a suprafeței și o calitate internă.
Pe scurt, în procesul de proiectare a matriței turnate sub presiune, trebuie acordată atenție evitării multor fenomene nedorite. Chiar și în epoca de astăzi, când sunt disponibile metode de analiză CAE, în stadiul incipient al proiectării sprue-urilor, experiența rezumată este considerată mai întâi în sistemul de porți, combinată organic, analizată, îmbunătățită și actualizată, ceea ce este obligat să obțină un efect multiplicator cu jumătate din efort.
Vă rugăm să păstrați sursa și adresa acestui articol pentru reimprimare:Cercetări privind sistemul de închidere a matriței turnate sub presiune
Minghe Compania de turnare sub presiune sunt dedicate fabricării și furnizează piese de turnare de calitate și de înaltă performanță (gama de piese turnate sub presiune din metal include în principal Turnare sub presiune cu perete subțire,Hot Cast casting sub presiune,Turnare sub presiune în cameră rece), Serviciu rotund (Serviciu de turnare sub presiune,Prelucrare Cnc,Fabricarea mucegaiului, Tratament de suprafață). Orice cerință personalizată de turnare sub presiune din aluminiu, magneziu sau turnare sub presiune din Zamak / zinc și alte cerințe de turnare sunt binevenite să ne contacteze.
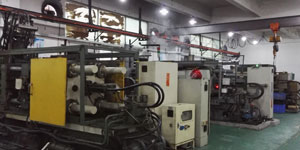
Sub controlul ISO9001 și TS 16949, toate procesele sunt efectuate prin sute de mașini avansate de turnare sub presiune, mașini cu 5 axe și alte facilități, variind de la blastere la mașini de spălat Ultra Sonic. Minghe nu numai că are echipamente avansate, dar are o echipă de ingineri cu experiență, operatori și inspectori pentru a face realitatea designul clientului.
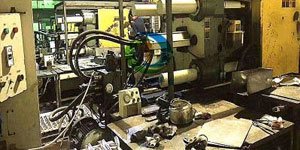
Producător contract de piese turnate sub presiune. Capacitățile includ piese de turnare sub presiune din aluminiu cu cameră rece de la 0.15 lbs. la 6 lbs., schimbare rapidă configurată și prelucrare. Serviciile cu valoare adăugată includ lustruire, vibrare, debavurare, sablare, vopsire, placare, acoperire, asamblare și scule. Materialele lucrate includ aliaje precum 360, 380, 383 și 413.
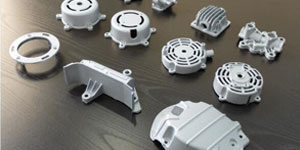
Asistență la proiectarea turnării sub presiune din zinc / servicii de inginerie simultană. Producător personalizat de piese turnate sub presiune din zinc. Pot fi fabricate piese turnate în miniatură, piese turnate sub presiune înaltă, piese turnate multi-glisante, piese turnate convenționale, piese turnate sub formă de unități și piese turnate independente și piese turnate sigilate în cavitate. Piesele turnate pot fi fabricate în lungimi și lățimi de până la toleranță de +/- 24 in.
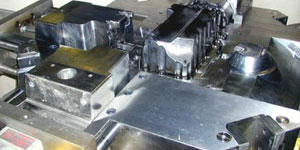
Producător certificat ISO 9001: 2015 de magneziu turnat sub presiune, capabilitățile includ turnare sub presiune cu magneziu de înaltă presiune de până la 200 tone cameră fierbinte și 3000 tone cameră rece, proiectare scule, lustruire, turnare, prelucrare, vopsire cu pulbere și lichide, QA complet cu capacități CMM , asamblare, ambalare și livrare.
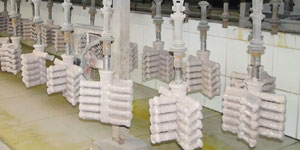
Certificat ITAF16949. Serviciul de turnare suplimentar include investiții de turnătorie,turnare cu nisip,Turnarea gravitației, Pierdere spumă turnare,Turnare centrifugă,Turnarea în vid,Turnare permanentă a matriței, .Capacitățile includ EDI, asistență tehnică, modelare solidă și procesare secundară.
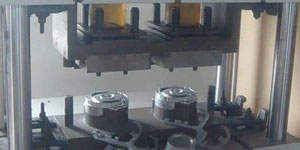
Industrii de turnare Părți Studii de caz pentru: Mașini, biciclete, aeronave, instrumente muzicale, ambarcațiuni, dispozitive optice, senzori, modele, dispozitive electronice, carcase, ceasuri, mașini, motoare, mobilier, bijuterii, jiguri, telecomunicații, iluminat, dispozitive medicale, dispozitive fotografice, Roboți, sculpturi, echipamente de sunet, echipamente sportive, scule, jucării și multe altele.
Ce vă putem ajuta să faceți în continuare?
∇ Accesați pagina principală pentru China turnare sub presiune
→Piese de turnare-Aflați ce am făcut.
→ Ralated Tips About Servicii de turnare sub presiune
By Producător de turnare sub presiune Minghe | Categorii: Articole utile |Material Etichete: Turnare din aluminiu, Turnarea zincului, Turnarea cu magneziu, Turnare cu titan, Turnare din oțel inoxidabil, Turnare din alamă,Turnarea bronzului,Distribuirea videoclipului,Istoricul companiei,Turnare din aluminiu | Comentarii dezactivate