Metoda de alimentare a firelor Procesul de tratare a fierului ductil
Prin producția efectivă, metoda de perforare și metoda de alimentare sunt utilizate pentru a produce fierul ductil și sunt analizate caracteristicile celor două procese. Prin comparație, performanța cuprinzătoare a pieselor turnate produse prin metoda de alimentare este mai stabilă decât cea a metodei de perforare; iar procesul de hrănire este sferoidizat. Pentru a împărtăși unele dintre experiențele din acesta.
1. Prezentare generală
După cum știm cu toții, puntea este o componentă importantă a vehiculului și este direct legată de siguranța vehiculului. Carcasa osiei este una dintre componentele cheie ale osiei. Performanța materialului carcasei osiei determină în mod direct capacitatea de încărcare a vehiculului. În prezent, carcasele pentru osii din industria camioanelor grele sunt, în general, împărțite în două categorii: carcase pentru osii ștanțate și sudate și carcase pentru osii turnate, iar carcasele pentru osii turnate pot fi împărțite în carcase pentru osii din oțel și carcase pentru osii din fontă.
Carcasa osiei turnate a ocupat întotdeauna poziția principală a carcasei osiei camioanelor grele datorită greutății portante ridicate și a costului redus de producție. Datorită mediului de lucru dur al carcasei osiei și a lucrărilor pe termen lung sub sarcină dinamică, acest lucru necesită cerințe ridicate pentru proprietățile materiale ale carcasei axei. În timp ce asigură rezistența, trebuie să obțină și o plasticitate și o rezistență mai mari pentru a se adapta la carcasa osiei. Caracteristicile muncii.
Știm că pentru fonta nodulară, procesul de sferoidizare este o verigă cheie în producția de fontă nodulară, iar calitatea tratamentului de sferoidizare afectează în mod direct calitatea fontei nodulare. La început, procesul de sferoidizare pe care l-am folosit a fost procesul de sferoidizare a metodei rush-in. Deși această metodă este simplă și ușor de utilizat, are multe neajunsuri, cum ar fi: randament scăzut din aliaj; fum mare și mediu de lucru slab; reacție Cantitatea de zgură produsă în acel moment este mare; efectul tratamentului este ușor afectat de factori externi, ceea ce duce la fluctuații ale calității pieselor turnate și adesea sferoidizare necalificată. Aceste fluctuații de calitate vor afecta performanța carcasei osiei și vor afecta chiar și siguranța vehiculului.
Procedeul de tratament sferoidizant al metodei de alimentare cu sârmă a fost aplicat la producția de fontă. A început în anii 1980 în străinătate. Deși producția internă de fontă nodulară a început să aplice această tehnologie târziu, tehnologia a fost popularizată și utilizată rapid în țară și este utilă pentru îmbunătățirea producției de grafit nodular. Efectul de stabilitate al calității fontei este evident.
2. Procesul de sferoidizare a sârmei de alimentare
Principiul de bază al procesului de sferoidizare care alimentează firul este de a înfășura o anumită compoziție de agent de sferoidizare sub formă de pulbere și inoculant prin pielea de oțel și de a o trimite în pachetul de tratament sferoidizant la o anumită viteză prin echipament, astfel încât sferoidizarea din partea de jos a pachetul va detona. Pentru a atinge scopul tratamentului de inoculare a sferoidizării.
În prezent, procesul de sferoidizare cu alimentare cu sârmă pe care îl adoptăm este: reglați compoziția chimică la cerințele procesului, încălziți până la 1510-1520 ℃ și lăsați să stea nemișcat, temperatura de filetare este de 1480 ~ 1500 ℃, puterea de fier este de 2 t și temperatura tratamentului sferoidizant este de 1420 1450 1370 ℃. Temperatura de turnare este de 1380 ~ 0.1 ℃. Rata de inoculare cu debitul este de XNUMX%.
Lungimea liniei de sferoidizare este de 39-46m, ajustată în funcție de conținutul de sulf al fierului topit original. Cu cât este mai mare conținutul de sulf, cu atât mai lungă trebuie adăugată linia de sferoidizare și invers. Lungimea liniei de inoculare este de 32m.
3. Procesul de sferoidizare a firului de alimentare îmbunătățește calitatea pieselor turnate
După mai mult de un an de producție, calitatea carcaselor noastre pe osie a fost îmbunătățită semnificativ în comparație cu înainte. Mai ales stabilitatea compoziției, metalografiei și proprietăților mecanice a fost mult îmbunătățită.
Compararea structurii metalografice Selectați aceeași poziție a turnării pentru a lustrui și observa structura metalografică. Imaginea metalografică făcută este prezentată în Figura 2. Comparativ cu metoda de perforare, bilele de grafit ale turnării produse prin metoda de alimentare sunt mai mult și mai subțiri, iar rotunjimea este mai bună.
4. Avantajele procesului de sferoidizare a firului de alimentare
Conform comparației noastre reale de producție, procesul de sferoidizare cu alimentare cu fir are multe avantaje față de procesul de sferoidizare a metodei de perforare.
- Îmbunătățirea mediului de producție la fața locului. Când agentul sferoidizant reacționează cu fierul topit, se generează o cantitate mare de fum și lumină puternică, ceea ce înrăutățește mediul de lucru la fața locului; atunci când metoda de alimentare a sârmei este utilizată pentru sferoidizare, stația de procesare Există un capac pentru a acoperi punga de sferoidizare, iar capacul este conectat la sistemul de îndepărtare a prafului din stația de procesare, astfel încât fumul este procesat de sistemul de îndepărtare a prafului de a fi eliberat direct în atelier.
- Cantitatea de aliaj adăugată este redusă, iar costul de producție este redus. După calcul, procesarea a 1t de metodă de alimentare cu fier topit poate economisi aproximativ 78 de yuani în costul materiei prime decât metoda impulsului. Conform capacității anuale de producție de 10,000 de tone de carcasă a osiei din fontă ductilă a fabricii noastre, economia anuală este Costul este de 780,000 de yuani, iar beneficiile sunt considerabile.
- Realizați automatizarea locurilor de muncă și reduceți intensitatea forței de muncă a lucrătorilor. Când se desfășoară procesul de sferoidizare, pregătirile preliminare ale lucrătorilor sunt greoaie, inclusiv cântărirea agentului sferoidizant și inoculant, adăugarea agentului sferoidizant și inoculant în pungă și sunt necesare operații de tamponare și acoperire; cantitatea adăugată de liniile de sferoidizare și inoculare a metodei de alimentare a firului se adaugă automat prin dulapul de comandă, ceea ce reduce o mulțime de muncă.
- Calitatea sferoidizării este stabilă, iar efectul de sferoidizare este mai bun. Conform statisticilor, de la utilizarea procesului de sferoidizare cu alimentare cu fir în 2013, rata de trecere a sferoidizării este de peste 99.5%, în timp ce rata de trecere a procesului de sferoidizare este de numai 95.%.
5. Cum să alegeți corect parametrii procesului de alimentare a sferoidizării firului
În producția efectivă, modul de selectare corectă a parametrilor procesului de alimentare a firului necesită un anumit număr de teste pentru verificare. Am suferit multe ajustări ale procesului de la începutul organizării testului până la producția de masă formală. Următoarele vor împărtăși experiența noastră cu colegii.
Pentru a selecta corect parametrii procesului de alimentare a sferoidizării firului, trebuie să acordați atenție următoarelor aspecte:
- (1) Alegerea sârmei cu miez Unele experiențe străine nu recomandă utilizarea sârmei cu miez mare. Conținutul de Mg este prea mare, reacția de sferoidizare este intensă, Mg arde mult și cantitatea de zgură este mare. În general, se recomandă selectarea unui conținut de Mg de aproximativ 30% și utilizarea unui fir de inoculare cu conținut de Ba, care poate preveni în mod eficient declinul inoculării. Parametrii principali ai firului cu miez folosit de compania noastră sunt: grosimea învelișului exterior din oțel este de 0.4 mm, iar diametrul firului de miez este de 13 mm. Înainte de utilizare, verificați dacă aspectul firului cu miez trebuie să fie rotund și fără crăpături, scurgeri de pulbere etc. În producția efectivă, este necesar să se regleze în funcție de temperatura de tratament și de înălțimea fierului topit. În general, cu cât temperatura de tratament este mai mare, cu atât este mai mare înălțimea fierului topit și viteza de alimentare a firului este mai mare. În plus. Unele materiale au introdus, de asemenea, o metodă convenabilă și fezabilă de măsurare a vitezei optime de alimentare a firului: măsurați mai întâi înălțimea fierului topit în punga de procesare și apoi alimentați manual mașina de sârmă, astfel încât firul de bază să atingă doar suprafața lichidului, apoi goliți ghișeul, mașina de alimentare cu sârmă manuală efectuează alimentarea cu sârmă. Când auziți sunetul de răspuns „braț”, verificați imediat lungimea de alimentare. Dacă această lungime este practic egală cu înălțimea fierului topit, viteza ar trebui să fie adecvată. După verificare, am selectat viteza de alimentare de 30m / min.
- Selectarea cantității de alimentare a firului Cantitatea adecvată de alimentare a firului este de a alimenta firul cel mai puțin miez sub premisa asigurării efectului de sferoidizare. Cantitatea de alimentare cu sârmă trebuie determinată în funcție de volumul de prelucrare al fierului topit, de temperatura de prelucrare și de conținutul de sulf al fierului topit. Conform cerințelor noastre originale privind conținutul de sulf topit de fier și cerințele procesului produsului, combinate cu verificarea experimentală, în condiția asigurării conținutului rezidual de magneziu, lungimea liniei de sferoidizare este de 39-46 m, iar lungimea liniei de inoculare este de 32 m.
- Alegerea temperaturii de prelucrare Temperatura de prelucrare ar trebui să fie redusă cât mai mult posibil cu premisa asigurării temperaturii de turnare. Cu cât temperatura de procesare este mai scăzută, cu atât este mai mare rata de absorbție a magneziului și consumul mai mic de sârmă cu miez. Conform testelor de producție propriu-zise, timpul de la începutul tratamentului de sferoidizare până la începutul turnării este de 4 până la 5 minute, timp în care scăderea temperaturii este de 40 până la 50 ° C, iar timpul de reacție sferoidant este de 80 până la 90 de secunde. Deoarece procesul de sferoidizare trebuie să fie răsturnat, stabilim temperatura de procesare la 1410 ~ 1450 ℃, limita superioară este luată atunci când temperatura camerei este mai mică de 5 ℃ și limita inferioară atunci când temperatura camerei este mai mare de 25 ℃.
- Selectarea conținutului de magneziu rezidual în fierul topit după tratament. Conținutul rezidual de magneziu trebuie rezervat pentru o anumită cantitate de conținut de magneziu, în funcție de caracteristicile turnării. La început, am controlat conținutul rezidual de magneziu la 0.03% până la 0.06%, dar după verificarea efectivă a producției, este mai potrivit să controlăm conținutul rezidual de magneziu la 0.05% până la 0.06%, deoarece am constatat că atunci când magneziul rezidual este mai mic de 0.04%, grafitul său Rotunjimea mingii este puțin mai proastă. Când este mai mare de 0.07%, cementita este predispusă să apară, iar tendința de contracție a fierului topit devine mai mare.
- Rezolvarea problemei blocării sârmei în timpul utilizării Fenomenul blocării sârmei va apărea în timpul procesului de transport al sârmei cu miez, ceea ce va face ca întregul pachet de fier topit să fie casat. În acest scop, am luat următoarele măsuri: una este instalarea unui inel de oțel deasupra tamburului de sârmă, așa cum se arată în Figura 5, care poate reduce îndoirea firului central și îl poate face să intre fără probleme în mecanismul de ghidare; a doua este conectarea celor două bobine. Când sudați, după sudare, lustruiți umflăturile mai mari pentru a preveni blocarea firului în timpul procesului de transport; în al treilea rând, evitați îndoirile cu diametrul mai mic de 1m în conducta de transport sau traseul sârmei cu miez pentru a împiedica transportul sârmei cu miez S-au produs scurgeri de pulbere sau blocaje în timpul procesului
6 Concluzie
- Procesul de sferoidizare a metodei de alimentare cu sârmă are o cantitate redusă de adăugare a aliajului, o rată ridicată de absorbție a Mg și poate reduce în mod eficient fumul și poluarea puternică a luminii în atelier, creând beneficii economice și ecologice bune pentru întreprinderile de turnătorie.
- Procesul de sferoidizare a metodei de alimentare a firului poate reduce în mod eficient rata de eșec a sferoidizării, poate îmbunătăți calitatea fontei nodulare, poate îmbunătăți proprietățile sale mecanice complete și poate spori competitivitatea pe piață a întreprinderii.
- Fiecare turnătorie ar trebui să selecteze parametrii de proces corespunzători pentru sferoidizarea firelor în funcție de propriile condiții de producție și cerințele procesului de produs, combinate cu experiența de producție a colegilor.
Procesul de sferoidizare a liniei de alimentare poate îmbunătăți semnificativ stabilitatea calității fontei nodulare, reduce costurile de producție, îmbunătățește mediul de producție și reduce intensitatea forței de muncă a lucrătorilor. Aceasta este tendința recentă de dezvoltare a procesului de sferoidizare.
Vă rugăm să păstrați sursa și adresa acestui articol pentru reimprimare: FProcesul de tratare a fierului ductil Metoda sârmei
Minghe Compania de turnare sub presiune sunt dedicate fabricării și furnizează piese de turnare de calitate și de înaltă performanță (gama de piese turnate sub presiune din metal include în principal Turnare sub presiune cu perete subțire,Hot Cast casting sub presiune,Turnare sub presiune în cameră rece), Serviciu rotund (Serviciu de turnare sub presiune,Prelucrare Cnc,Fabricarea mucegaiului, Tratament de suprafață). Orice cerință personalizată de turnare sub presiune din aluminiu, magneziu sau turnare sub presiune din Zamak / zinc și alte cerințe de turnare sunt binevenite să ne contacteze.
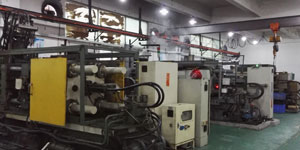
Sub controlul ISO9001 și TS 16949, toate procesele sunt efectuate prin sute de mașini avansate de turnare sub presiune, mașini cu 5 axe și alte facilități, variind de la blastere la mașini de spălat Ultra Sonic. Minghe nu numai că are echipamente avansate, dar are o echipă de ingineri cu experiență, operatori și inspectori pentru a face realitatea designul clientului.
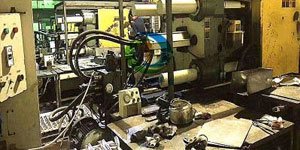
Producător contract de piese turnate sub presiune. Capacitățile includ piese de turnare sub presiune din aluminiu cu cameră rece de la 0.15 lbs. la 6 lbs., schimbare rapidă configurată și prelucrare. Serviciile cu valoare adăugată includ lustruire, vibrare, debavurare, sablare, vopsire, placare, acoperire, asamblare și scule. Materialele lucrate includ aliaje precum 360, 380, 383 și 413.
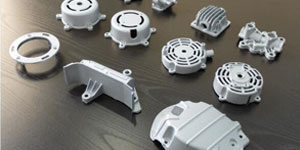
Asistență la proiectarea turnării sub presiune din zinc / servicii de inginerie simultană. Producător personalizat de piese turnate sub presiune din zinc. Pot fi fabricate piese turnate în miniatură, piese turnate sub presiune înaltă, piese turnate multi-glisante, piese turnate convenționale, piese turnate sub formă de unități și piese turnate independente și piese turnate sigilate în cavitate. Piesele turnate pot fi fabricate în lungimi și lățimi de până la toleranță de +/- 24 in.
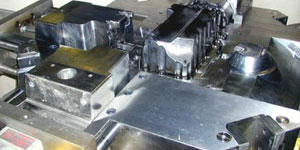
Producător certificat ISO 9001: 2015 de magneziu turnat sub presiune, capabilitățile includ turnare sub presiune cu magneziu de înaltă presiune de până la 200 tone cameră fierbinte și 3000 tone cameră rece, proiectare scule, lustruire, turnare, prelucrare, vopsire cu pulbere și lichide, QA complet cu capacități CMM , asamblare, ambalare și livrare.
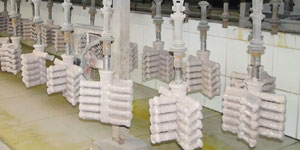
Certificat ITAF16949. Serviciul de turnare suplimentar include investiții de turnătorie,turnare cu nisip,Turnarea gravitației, Pierdere spumă turnare,Turnare centrifugă,Turnarea în vid,Turnare permanentă a matriței, .Capacitățile includ EDI, asistență tehnică, modelare solidă și procesare secundară.
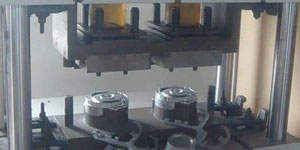
Industrii de turnare Părți Studii de caz pentru: Mașini, biciclete, aeronave, instrumente muzicale, ambarcațiuni, dispozitive optice, senzori, modele, dispozitive electronice, carcase, ceasuri, mașini, motoare, mobilier, bijuterii, jiguri, telecomunicații, iluminat, dispozitive medicale, dispozitive fotografice, Roboți, sculpturi, echipamente de sunet, echipamente sportive, scule, jucării și multe altele.
Ce vă putem ajuta să faceți în continuare?
∇ Accesați pagina principală pentru China turnare sub presiune
→Piese de turnare-Aflați ce am făcut.
→ Ralated Tips About Servicii de turnare sub presiune
By Producător de turnare sub presiune Minghe | Categorii: Articole utile |Material Etichete: Turnare din aluminiu, Turnarea zincului, Turnarea cu magneziu, Turnare cu titan, Turnare din oțel inoxidabil, Turnare din alamă,Turnarea bronzului,Distribuirea videoclipului,Istoricul companiei,Turnare din aluminiu | Comentarii dezactivate