Prelucrarea prin tăiere a pieselor din metalurgia pulberilor (P / M)
Utilizarea procesului de metalurgie a pulberilor (P / M) pentru fabricarea pieselor pentru sistemele de alimentare auto continuă să crească. Piesele fabricate prin procesul P / M au multe avantaje importante și unice. Structura poroasă reziduală lăsată intenționat în aceste părți este bună pentru auto-lubrifiere și izolare fonică. Aliaje complexe care sunt dificil sau imposibil de fabricat prin procesul tradițional de turnare pot fi produse prin utilizarea tehnologiei P / M. Părțile fabricate prin această tehnologie au de obicei o capacitate de procesare redusă sau deloc, ceea ce le face mai ieftine și mai puține deșeuri în materiale. Din păcate, în spatele atracției acestor caracteristici, piesele P / M sunt greu de prelucrat.
Deși una dintre intențiile inițiale ale industriei P / M este de a elimina toate prelucrările, acest obiectiv nu a fost încă atins. Cele mai multe piese pot fi „aproape de forma finală” și au nevoie de finisaje.
Cu toate acestea, în comparație cu piesele turnate și forjate, o cantitate mică de material care trebuie îndepărtată din piesele P / M este un material tipic rezistent la uzură.
Structura poroasă este una dintre caracteristicile care fac ca piesele p / M să aibă o gamă largă de utilizări, dar durata de viață a sculei va fi deteriorată și de structura poroasă. Structura poroasă poate stoca ulei și sunet, dar duce și la tăiere micro-intermitentă. Când se deplasează înainte și înapoi de la gaură la particulele solide, vârful sculei este impactat continuu, ceea ce poate duce la deformarea foarte mică a fracturii de oboseală și colapsul marginii fine de-a lungul muchiei tăietoare. Pentru a înrăutăți lucrurile, particulele sunt de obicei foarte dure. Chiar dacă duritatea macro a materialului măsurat este cuprinsă între 20 și 35 de grade, dimensiunea particulelor componentului este de până la 60 de grade. Aceste particule dure provoacă o uzură severă și rapidă a marginilor. Multe piese p / M sunt tratabile termic, iar duritatea și rezistența materialului sunt mai mari după tratament termic. În cele din urmă, datorită tehnologiei de sinterizare și tratament termic și a gazelor utilizate, suprafața materialului va conține oxizi și / sau carburi dure și rezistente la uzură.
Performanța pieselor P / M
Majoritatea proprietăților pieselor P / M, inclusiv prelucrarea, sunt legate nu numai de compoziția chimică a aliajului, ci și de nivelul de porozitate al structurii poroase. Porozitatea multor părți structurale este de până la 15% ± 20%. Porozitatea pieselor utilizate ca dispozitive de filtrare poate ajunge până la 50%. La celălalt capăt al seriei, porozitatea părților forjate sau a șoldului este de doar 1% sau mai puțin. Aceste materiale devin deosebit de importante în aplicațiile auto și aeronave, deoarece pot atinge niveluri mai ridicate de rezistență.
Rezistența la tracțiune, rezistența și ductilitatea aliajului P / M vor crește odată cu creșterea densității, iar prelucrarea poate fi, de asemenea, îmbunătățită, deoarece porozitatea este dăunătoare vârfului sculei.
Creșterea nivelului de porozitate poate îmbunătăți performanța de izolare fonică a pieselor. Oscilația de amortizare a pieselor standard este redusă semnificativ în piesele P / M, ceea ce este foarte important pentru mașinile-unelte, conductele de aer condiționat și instrumentele pneumatice. Porozitatea ridicată este necesară și pentru angrenajele autolubrifiante.
Dificultăți în prelucrare
Deși unul dintre obiectivele dezvoltării continue a industriei P / M este de a elimina prelucrarea și una dintre principalele atracții ale procesului P / M este că este necesară doar o cantitate mică de procesare, multe părți au nevoie în continuare de post-tratament pentru a obține precizie mai mare sau finisare mai bună a suprafeței. Din păcate, prelucrarea acestor piese este extrem de dificilă. Majoritatea problemelor întâmpinate sunt cauzate de porozitate. Porozitatea duce la microoboseala marginii de tăiere. Marginea de tăiere se taie în mod constant în și în afară. Trece între particule și găuri. Impactul mic repetat duce la mici fisuri pe muchia de tăiere.
Aceste fisuri de oboseală cresc până când marginea de tăiere se prăbușește. Acest tip de margine de micro-ciobire este de obicei foarte mic și de obicei prezintă uzură normală abrazivă.
Porozitatea reduce, de asemenea, conductivitatea termică a pieselor P / M, ceea ce duce la o temperatură ridicată pe muchia de tăiere și provoacă uzura și deformarea craterului. Structura poroasă conectată intern oferă o cale pentru evacuarea fluidului de tăiere din zona de tăiere. Acest lucru poate provoca fisuri fierbinți sau deformări, în special la foraj.
Creșterea suprafeței cauzată de structura poroasă internă duce, de asemenea, la oxidare și / sau carbonizare în timpul tratamentului termic. Așa cum am menționat anterior, acești oxizi și carburi sunt duri și rezistente la uzură.
Structura poroasă dă, de asemenea, eșecul citirii durității piesei, ceea ce este extrem de important. Atunci când duritatea macro a unei piese P / M este măsurată intenționat, aceasta include factorul de duritate al găurii. Structura poroasă duce la prăbușirea structurii și dă impresia greșită a părților relativ moi. Particulele sunt mult mai dure. După cum s-a descris mai sus, diferența este dramatică.
Existența incluziunilor în părțile PM este, de asemenea, dezavantajoasă. În timpul prelucrării, aceste particule vor fi trase în sus de la suprafață și se vor forma zgârieturi sau zgârieturi pe suprafața piesei atunci când este frecată în fața sculei. Aceste incluziuni sunt de obicei mari, lăsând găuri vizibile pe suprafața piesei.
Diferența conținutului de carbon duce la incoerența prelucrării. De exemplu, conținutul de carbon al aliajului fc0208 variază de la 0.6% la 0.9%. Un lot de materiale cu un conținut de 0.9% carbon sunt relativ dure, rezultând o durată de viață scăzută a sculei. Celălalt lot de materiale cu un conținut de carbon de 0.6% au o durată de viață excelentă a sculei. Ambele aliaje se încadrează în domeniul permis.
Problema finală de prelucrare este legată de tipul de tăiere care are loc pe partea P / M. Deoarece piesa este aproape de forma finală, adâncimea de tăiere este de obicei foarte mică. Acest lucru necesită o tăiere liberă. Acumularea de așchii pe muchia de tăiere duce adesea la micro așchiere.
Tehnologie de procesare
Pentru a depăși aceste probleme, sunt aplicate mai multe tehnologii (unice industriei). Structura poroasă de suprafață este adesea etanșată prin infiltrare. De obicei este necesară tăierea suplimentară gratuită. Recent, s-au folosit tehnici îmbunătățite de producere a pulberilor concepute pentru a crește curățenia pulberii și a reduce oxizii și carburile în timpul tratamentului termic.
Structura poroasă de suprafață închisă este realizată prin infiltrare de metal (de obicei cupru) sau polimer. S-a speculat că infiltrarea acționează ca un lubrifiant. Majoritatea datelor experimentale arată că avantajul real constă în închiderea structurii poroase a suprafeței și astfel prevenirea microobosirii marginii tăietoare. Reducerea zgomotului îmbunătățește durata de viață a sculei și finisarea suprafeței. Cea mai dramatică utilizare a infiltrării arată o creștere cu 200% a duratei de viață a sculei atunci când structura poroasă este închisă.
Se știe că aditivi precum MNS, s, MoS2, MgSiO3 și BN cresc viața sculei. Acești aditivi îmbunătățesc prelucrabilitatea, facilitând separarea așchiilor de piesa de prelucrat, spargerea așchiilor, prevenirea acumulării așchiilor și ungerea muchiei de tăiere. Creșterea cantității de aditivi poate îmbunătăți prelucrarea, dar poate reduce rezistența și rezistența.
Tehnologia de atomizare a pulberii pentru a controla sinterizarea și tratarea termică a gazelor din cuptor face posibilă producerea de pulbere și piese curate, ceea ce minimizează apariția incluziunilor și a carburilor de oxid de suprafață.
Material scule
Cele mai utilizate instrumente din industria P / M sunt acele materiale care sunt rezistente la uzură, rezistente la fisuri la margini și fără așchii în condiții de finisare bună a suprafeței. Aceste caracteristici sunt utile pentru orice operațiune de prelucrare, în special pentru piesele P / M. Materialele pentru scule incluse în această categorie sunt sculele de nitrură de bor cubică (CBN), cermetele neacoperite și acoperite și carburile cimentate sinterizate acoperite îmbunătățite.
Instrumentele CBN sunt atractive datorită durității ridicate și rezistenței la uzură. Acest instrument a fost utilizat de mai mulți ani în prelucrarea oțelului și fontei cu o duritate Rockwell de 45 sau mai mare. Cu toate acestea, datorită proprietăților unice ale aliajului P / M și diferenței semnificative între micro-duritate și macro-duritate, instrumentele CBN pot fi utilizate pentru piesele P / M cu o duritate Rockwell de 25. Parametrul cheie este duritatea particulelor. Când duritatea particulelor depășește Rockwell 50 de grade, instrumentele CBN sunt disponibile indiferent de valoarea durității macro. Limita evidentă a acestor instrumente este lipsa lor de rezistență. În caz de tăiere intermitentă sau porozitate ridicată, este necesară armarea muchiilor, incluzând șanfrenarea negativă și tăierea grea. Tăierea ușoară simplă poate fi realizată cu tăișul tăiat.
Există mai multe materiale CBN care sunt eficiente. Materialul cu cea mai bună rezistență este compus în principal din întreg CBN. Au o rezistență excelentă, deci pot fi folosite pentru degroșare. Limitările lor sunt de obicei legate de finisajul suprafeței. Este în mare măsură determinată de particulele CBN individuale care alcătuiesc instrumentul. Când particulele cad de pe muchia de tăiere, acestea vor afecta suprafața materialului piesei de prelucrat. Cu toate acestea, nu este atât de grav ca instrumentul pentru particule fine să cadă de pe o particulă.
Materialul CBN utilizat de obicei are un conținut ridicat de CBN și o dimensiune medie a particulelor. Lama de finisare CBN are granulație fină, iar conținutul de CBN este redus. Acestea sunt cele mai eficiente atunci când este necesară tăierea ușoară și finisarea suprafeței sau când aliajul procesat este deosebit de dur.
În multe aplicații de tăiere, durata de viață a sculei este independentă de tipul de material. Cu alte cuvinte, orice material CBN poate obține o durată de viață similară. În aceste cazuri, selectarea materialelor se bazează în principal pe cel mai mic cost al fiecărei muchii de tăiere. O lamă rotundă are o suprafață CBN întreagă și poate oferi patru sau mai multe muchii tăietoare, ceea ce este mai ieftin decât patru lame CBN incrustate.
Atunci când duritatea pieselor P / M este mai mică decât Rockwell la 35 de grade, iar duritatea particulelor se află în raza de acțiune, cermet este de obicei una dintre alegeri. Cermetele sunt foarte dure, pot preveni în mod eficient acumularea de cipuri și pot rezista la viteze mari. În plus, deoarece cermetele au fost întotdeauna utilizate pentru prelucrarea de mare viteză și finisare a oțelului și a oțelului inoxidabil, ele au de obicei caneluri geometrice ideale, potrivite pentru piese aproape de formate.
Cermetele de astăzi sunt complicate în metalurgie, cu până la 11 elemente de aliere. De obicei sunt sinterizate din particule TiCN și adeziv Ni Mo. TiCN oferă duritate, rezistență la acumulare de cipuri și stabilitate chimică, care sunt importante pentru utilizarea cu succes a cermetelor. În plus, aceste instrumente au de obicei un conținut ridicat de adeziv, ceea ce înseamnă că au o rezistență bună. Într-un cuvânt, au toate caracteristicile procesării eficiente a aliajului P / M. Mai multe tipuri de cermete sunt eficiente, la fel ca și carbura de tungsten cimentată sinterizată, cu cât este mai mare conținutul de liant, cu atât este mai bună rezistența.
O dezvoltare relativ nouă cunoscută este că depunerea chimică a vaporilor la temperatură medie (mtcvd) oferă, de asemenea, un avantaj pentru industria P / M. Mtcvd păstrează toată rezistența la uzură și rezistența la uzură a craterelor din depunerea tradițională de vapori chimici (CVD), dar îmbunătățește și rezistența în mod obiectiv. Creșterea rezistenței provine în principal din scăderea fisurilor. Acoperirea este depusă la temperatură ridicată și apoi răcită în cuptor. Acoperirea conține fisuri atunci când instrumentul atinge temperatura camerei din cauza dilatării termice inconsistente. Similar cu zgârieturile de pe sticla plană, aceste fisuri reduc rezistența muchiei tăietoare. Temperatura mai mică de depunere a mtcvd duce la o frecvență mai mică a fisurilor și la o rezistență mai bună a muchiei de tăiere.
Când substratul de acoperire CVD și acoperire mtcvd au aceleași caracteristici și pansament de margine, diferența de duritate a acestora poate fi demonstrată. Atunci când este utilizat în aplicații în care este necesară rezistența la margini, performanța acoperirii mtcvd este mai bună decât cea a acoperirii CVD. Prin analiză, la prelucrarea pieselor P / M cu structură poroasă, rezistența la margine este importantă. Acoperirea Mtcvd este mai bună decât acoperirea CVD.
Stratul de depunere fizică prin vapori (PVD) este mai subțire și mai puțin rezistent la uzură decât stratul mtcvd sau CVD. Cu toate acestea, acoperirea PVD poate rezista la un impact semnificativ în timpul aplicării. Acoperirea PVD este eficientă atunci când tăierea este uzată abraziv, CBN și cermetele sunt prea fragile și necesită o finisare excelentă a suprafeței.
De exemplu, muchia de tăiere a carburii cimentate C-2 poate fi prelucrată fc0205 la o viteză de linie de 180 m / min și o viteză de avans de 0.15 mm / rotație. După prelucrarea a 20 de piese, acumularea cipului poate provoca colapsul micro. Când se folosește acoperirea cu nitrură de titan PVD (TIN), acumularea de așchii este restrânsă și durata de viață a sculei este prelungită. Când se folosește acoperirea cu staniu pentru acest test, caracteristicile de uzură abrazivă ale pieselor P / M sunt de așteptat să fie mai eficiente cu acoperirea cu TiCN. TiCN are aproape aceeași rezistență la acumulare de cip ca staniu, dar este mai dur și mai rezistent la uzură decât staniu.
Structura poroasă este importantă și afectează prelucrabilitatea aliajului fc0208. Când structura poroasă și caracteristicile se schimbă, diferite materiale pentru scule oferă avantaje corespunzătoare. Când densitatea este scăzută (6.4 g / cm3), duritatea macro este scăzută. În acest caz, carbură cimentată acoperită cu mtcvd oferă cea mai bună durată de viață a sculei. Micul oboseala tăieturii este foarte importantă, iar rezistența muchiei este foarte importantă. În acest caz, o lamă de cermet de rezistență bună asigură o durată de viață maximă a sculei.
Atunci când se produce același aliaj cu o densitate de 6.8 g / cm3, uzura abrazivă devine mai importantă decât fisura de margine. În acest caz, acoperirea mtcvd oferă cea mai bună durată de viață a sculei. Carbura cimentată acoperită cu PVD este utilizată pentru a testa cele două tipuri de piese extrem de dure și se rupe când atinge muchia de tăiere.
Când viteza crește (viteza liniară depășește 300 de metri pe minut), cermetele și chiar cermetele acoperite vor produce uzura craterelor. Carbura cimentată acoperită este mai potrivită, mai ales atunci când rezistența de tăiere a carburii cimentate acoperite este bună. Acoperirea Mtcvd este deosebit de eficientă pentru carbură cimentată cu zonă bogată în cobalt.
Cermetele sunt utilizate cel mai frecvent în strunjire și plictiseală. Carburile cimentate acoperite cu PVD sunt ideale pentru prelucrarea firelor, deoarece se pot aștepta viteze mai mici și o atenție sporită la acumulare.
Vă rugăm să păstrați sursa și adresa acestui articol pentru reimprimare:Prelucrarea prin tăiere a pieselor din metalurgia pulberilor (P / M)
Compania Minghe Casting este dedicată producției și furnizează piese de turnare de calitate și de înaltă performanță (gama de piese turnate sub presiune din metal include în principal Turnare sub presiune cu perete subțire,Hot Cast casting sub presiune,Turnare sub presiune în cameră rece), Serviciu rotund (Serviciu de turnare sub presiune,Prelucrare Cnc,Fabricarea mucegaiului, Tratament de suprafață). Orice cerință personalizată de turnare sub presiune din aluminiu, magneziu sau turnare sub presiune din Zamak / zinc și alte cerințe de turnare sunt binevenite să ne contacteze.
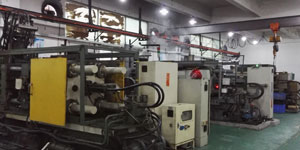
Sub controlul ISO9001 și TS 16949, toate procesele sunt efectuate prin sute de mașini avansate de turnare sub presiune, mașini cu 5 axe și alte facilități, variind de la blastere la mașini de spălat Ultra Sonic. Minghe nu numai că are echipamente avansate, dar are o echipă de ingineri cu experiență, operatori și inspectori pentru a face realitatea designul clientului.
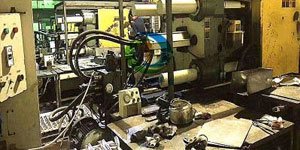
Producător contract de piese turnate sub presiune. Capacitățile includ piese de turnare sub presiune din aluminiu cu cameră rece de la 0.15 lbs. la 6 lbs., schimbare rapidă configurată și prelucrare. Serviciile cu valoare adăugată includ lustruire, vibrare, debavurare, sablare, vopsire, placare, acoperire, asamblare și scule. Materialele lucrate includ aliaje precum 360, 380, 383 și 413.
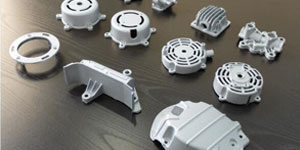
Asistență la proiectarea turnării sub presiune din zinc / servicii de inginerie simultană. Producător personalizat de piese turnate sub presiune din zinc. Pot fi fabricate piese turnate în miniatură, piese turnate sub presiune înaltă, piese turnate multi-glisante, piese turnate convenționale, piese turnate sub formă de unități și piese turnate independente și piese turnate sigilate în cavitate. Piesele turnate pot fi fabricate în lungimi și lățimi de până la toleranță de +/- 24 in.
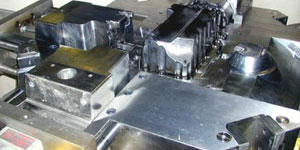
Producător certificat ISO 9001: 2015 de magneziu turnat sub presiune, capabilitățile includ turnare sub presiune cu magneziu de înaltă presiune de până la 200 tone cameră fierbinte și 3000 tone cameră rece, proiectare scule, lustruire, turnare, prelucrare, vopsire cu pulbere și lichide, QA complet cu capacități CMM , asamblare, ambalare și livrare.
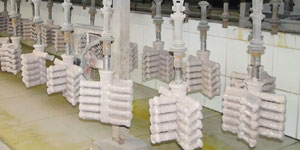
Certificat ITAF16949. Serviciul de turnare suplimentar include investiții de turnătorie,turnare cu nisip,Turnarea gravitației, Pierdere spumă turnare,Turnare centrifugă,Turnarea în vid,Turnare permanentă a matriței, .Capacitățile includ EDI, asistență tehnică, modelare solidă și procesare secundară.
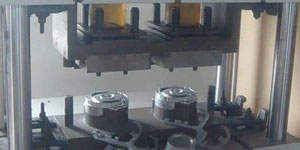
Industrii de turnare Părți Studii de caz pentru: Mașini, biciclete, aeronave, instrumente muzicale, ambarcațiuni, dispozitive optice, senzori, modele, dispozitive electronice, carcase, ceasuri, mașini, motoare, mobilier, bijuterii, jiguri, telecomunicații, iluminat, dispozitive medicale, dispozitive fotografice, Roboți, sculpturi, echipamente de sunet, echipamente sportive, scule, jucării și multe altele.
Ce vă putem ajuta să faceți în continuare?
∇ Accesați pagina principală pentru China turnare sub presiune
→Piese de turnare-Aflați ce am făcut.
→ Ralated Tips About Servicii de turnare sub presiune
By Producător de turnare sub presiune Minghe | Categorii: Articole utile |Material Etichete: Turnare din aluminiu, Turnarea zincului, Turnarea cu magneziu, Turnare cu titan, Turnare din oțel inoxidabil, Turnare din alamă,Turnarea bronzului,Distribuirea videoclipului,Istoricul companiei,Turnare din aluminiu | Comentarii dezactivate