Tehnologia de preparare a compozitului cu matrice metalică armată cu particule prin metoda turnării
Compozitele cu matrice metalică sunt materiale multifazice cu o a doua fază specială dispersată într-o matrice metalică sau din aliaj. A doua fază cu proprietăți fizice și mecanice speciale sporește foarte mult rezistența, duritatea, rezistența la uzură, rezistența la căldură și alte proprietăți ale materialului. Prin urmare, această a doua fază este numită și faza de întărire. Faza de armare este de obicei împărțită în faza de armare a particulelor și faza de armare cu fibre (mustăți). Din motive precum prețul armăturii și tehnologia compozitului, majoritatea materialelor compozite realizate prin metoda turnării sunt armate cu particule.
În ultimii ani, metoda de preparare a materialelor compozite armate cu particule s-a îmbunătățit continuu în metoda fizică de adăugare a armăturii și a fost dezvoltată sinteza reacției in situ a metodei de armare.
Indiferent ce fel de metodă de turnare a compozitului este utilizată, pentru a pregăti cu succes produse compozite cu performanțe excelente și calitate stabilă, următoarele probleme trebuie rezolvate tehnic:
- ① Selectați matricea și armătura corespunzătoare pe baza diferitelor cerințe ale materialului,
- ②Îmbunătățiți umectabilitatea matricei topite la armare,
- ③controlați distribuția rezonabilă a armăturii în matrice,
- Rezolvați problema procesului de formare a turnării cauzată de efectul particulelor de armare asupra vâscozității topiturii matricei.
Acest articol rezumă problemele menționate mai sus privind tehnologia de preparare a turnării materialelor compozite cu matrice metalică armată cu particule, pentru a promova producția de material compozit armat cu particule.
- Selectarea armăturii: Performanța matricei, armarea și combinația bună a armăturii și a matricei determină performanța materialului compozit, astfel armătura trebuie selectată în mod rezonabil în funcție de tipul de substrat și de cerințele de performanță ale materialului compozit . La selectarea unei armături, trebuie luați în considerare modulul elastic, rezistența la tracțiune, duritatea, stabilitatea termică, densitatea, punctul de topire, prețul și alți factori ai armăturii. În același timp, coeficientul de expansiune liniară și reactivitatea chimică dintre armătură și matrice ar trebui să fie potrivite. Revendicare. Matricea cu aluminiu ca componentă principală, armăturile utilizate în mod obișnuit sunt grafit, Al2O3, SiC, TiC, Al3Ti, TiB, Al3Zr etc. Cercetarea materialelor compozite cu oțel ca matricea nu este la fel de matură ca aluminiul compozite matriciale și armăturile utilizate în mod obișnuit sunt mai mature. Mai puține, în principal WC, VC, TiC, TiN, Al2O3, SiC etc. După selectarea tipului de armare, dimensiunea armăturii și fracția de volum a acesteia în matrice ar trebui, de asemenea, determinate prin experimente.
- Metode de îmbunătățire a umectabilității armăturii / matricei: îmbunătăți umectabilitatea armăturii prin topirea matricei, ajută la reducerea aglomerării armăturii, ajută la îmbunătățirea rezistenței la lipire a interfeței matrice / armare și la îmbunătățirea materialului compozit general. cuvinte, contribuie și la distribuirea uniformă a armăturii în matrice. Următoarele măsuri sunt utilizate de obicei pentru a îmbunătăți umectabilitatea topiturii matricei până la armătură.
- Tratament de acoperire a suprafeței de armare: Acoperirea unui anumit metal sau compus pe suprafața de armare prin metode precum placarea fără electrolit sau depunerea de vapori poate îmbunătăți în mod eficient umectabilitatea topiturii matricei pe corpul de armare. Studiile au arătat că acoperirea cu cupru de pe suprafața grafitului și depunerea de vapori a TiN pe suprafața particulelor de Al2O3 au îmbunătățit efectiv umectabilitatea matricei față de particulele de armare.
- Surfactanți suplimentari: conform rapoartelor, adăugarea de blocuri de magneziu în timp ce se adaugă grafit sau pulbere de siliciu la topitura de aluminiu poate îmbunătăți umectabilitatea lichidului de aluminiu la armătură. Cercetările din ultimii ani au arătat, de asemenea, că, pe lângă Mg, Ca, RE, elementele metalelor alcaline și elementele din grupa VI și grupa VIa au toate efectul de a îmbunătăți umectabilitatea aluminiului topit pe armături precum Al2O3 și SiC.
- Tratamentul termic al armăturii: Tratamentul termic pentru îndepărtarea uleiului și apei de pe suprafața particulelor de armare poate crește energia de suprafață a armăturii și poate crește umectabilitatea topiturii până la armătură. Cineva a pregătit materiale compozite grafit / aluminiu folosind pulbere de grafit tratată termic fără acoperire de cupru. Metoda de tratare a încălzirii este: încălzirea pulberii de grafit la aproximativ 600 ° C timp de 8 ore pentru a activa suprafața, apoi răcirea și reîncălzirea la 200 ° C înainte de a adăuga lichidul de aluminiu pentru a îndepărta umezeala. Unii oameni au folosit, de asemenea, metoda de încălzire a armăturii pentru a îmbunătăți umectabilitatea armăturii și a matricei pentru a produce materiale compozite.
- Tratament cu ultrasunete de înaltă energie al topiturii: cineva a pregătit material compozit SiC / ZA27 cu tratament ultrasunet de mare energie al topiturii. Studiul consideră că efectul de cavitație produs de ultrasunetele cu energie ridicată atunci când se propagă în topitură curăță suprafața particulelor armate, crește tensiunea superficială a particulelor și, în același timp, reduce tensiunea superficială a topiturii și îmbunătățește semnificativ relația dintre particulele de SiC și topirea ZA27. Umectabilitate.
- Sinteza reacțiilor in-situ ale armării: aplicarea tehnologiei de sinteză a reacțiilor in-situ pentru a pregăti un aliaj principal care conține particule de armare și apoi adăugarea acestui aliaj principal la matrița topită pentru a pregăti tehnologia materialelor compozite a devenit un punct fierbinte în cercetarea materialelor compozite in ultimii ani. Metoda de sinteză a reacțiilor in situ adaugă de obicei niște metale pure, aliaje, compuși sau substanțe sărate la aliajul principal, iar armarea este obținută prin reacții chimice între aditivi sau între aditivi și componentele aliajului principal. Deoarece armătura este generată de reacția in situ, suprafața este curată și fără poluare, iar stabilitatea termică este bună, ceea ce rezolvă bine problema umectabilității armăturii prin topirea matricei, iar armătura și matricea sunt foarte ferm combinat cu un efect mai bun de întărire. Unii oameni de știință au amestecat pulberile de Al, Ti și C într-o anumită proporție și apoi le-au presat în bucăți mici. Bucățile mici au fost sinterizate sub vid într-un cuptor de difuzie la temperatură înaltă pentru a obține un aliaj master TiC / Al, iar compozitul TiC / 2618 a fost preparat din aliajul principal. material. Alții au pregătit cu succes materiale compozite cu distribuție uniformă a particulelor armate și proprietăți excelente prin sinteza reacției in situ.
- Tehnologia de control al distribuției armăturilor: Controlul distribuției armăturilor în matrice și oferirea unui joc deplin consolidării efective a matricei este garanția fundamentală pentru pregătirea produselor compozite care îndeplinesc anumite cerințe de performanță.
- Metoda de control a distribuției neuniforme a armăturilor: Pentru materialele rezistente la uzură / reducătoare de uzură, suprafața de lucru trebuie să aibă performanțe ridicate la uzură, în timp ce părțile rămase au proprietăți mecanice cuprinzătoare mai bune pentru a asigura că suprafața de lucru este susținut în mod eficient.
Prin urmare, astfel de produse care trebuie consolidate local necesită distribuirea armăturii într-o anumită gamă lângă suprafața de lucru a produsului. Există mai multe metode frecvent utilizate:
- Metoda de pre-armare: Metoda de pre-armare este una dintre metodele principale pentru prepararea materialelor compozite întărite la suprafață prin metoda aditivă. Este o aplicație a tehnologiei de modificare a suprafeței metodei de infiltrație turnată în prepararea materialelor compozite. Potrivit în principal pentru prepararea produselor compozite rezistente la uzură. Metoda specifică este: așezați armătura sub formă de bloc de vopsea sau pastă pe partea în care produsul trebuie întărit, apoi turnați-l în lichidul din aliaj de matrice. Lichidul din aliaj de matrice pătrunde în spațiul corpului de armare prin efectul sifonului capilar și presiunea lichidului din aliaj și se solidifică Apoi, se formează un produs compozit întărit la suprafață în care corpul de armare și matricea sunt strâns combinate. Oamenii de știință au făcut cercetări aprofundate cu privire la această tehnologie și consideră că cheia tehnologiei compozite de suprafață pre-armată constă în: dimensiunea adecvată a particulelor de armare și o bună umectare a armăturii prin topirea matricei; Selection selectarea și acoperirea liantului, procesul de preparare și periere a pastei, control controlul temperaturii de turnare și procesul de turnare; metoda de armare presetată are caracteristicile procesului simplu, cost redus și efect excelent. Este o tehnologie compozită de suprafață care a fost aplicată cu succes în prezent și are o perspectivă de aplicație foarte largă.
- Metoda de control centrifugal: Pe baza diferenței de greutate specifică a armăturii și a topiturii matricei, metoda de realizare a armăturii într-o distribuție de segregare în gradient de-a lungul direcției radiale cu ajutorul forței centrifuge se numește metoda de control centrifugal. O direcție importantă de dezvoltare a materialelor compozite cu gradient. Cineva a folosit o metodă de control centrifugă pentru a prepara un material compozit grafit / aluminiu cu o distribuție în gradient a grafitului. Oamenii de știință, turnarea centrifugă din aliaj de Al-Fe, au obținut țeava turnată compusă cu gradient de auto-generare în care faza primară de Fe este distribuită de-a lungul gradientului radial. Materialul compozit gradient auto-generat din aliaj de Al-Fe turnat cu centrifugă metalică acoperit cu nisip a subliniat: s Pe măsură ce crește numărul armăturilor, gradientul de distribuție a armăturilor în direcția radială scade treptat, iar gama de distribuție în direcția radială se extinde treptat ; În intervalul 0 ~ 2000r / min, odată cu creșterea vitezei de rotație, gradientul de distribuție a armăturii de-a lungul direcției radiale crește treptat, în timp ce domeniul de distribuție în direcția radială scade treptat.
- Metoda de control a agitării electromagnetice: Oamenii de știință au aplicat o agitare electromagnetică puternică de curent alternativ la topirea aliajului (Mg2Si) 20Al80 în timpul procesului de solidificare pentru a prepara un material compozit cu gradient îmbogățit în Mg2Si pe suprafața exterioară. Conform analizei, atunci când se efectuează agitare electromagnetică, metalul topit va fi supus forței electromagnetice direcționate către axă în câmpul magnetic alternativ. Datorită conductivității scăzute a armăturii (nașterea Mg2Si), aceasta nu este practic afectată de forța electromagnetică direcționată către axă, în timp ce forța electromagnetică exercitată asupra topiturii este relativ mare, rezultând un câmp de forță neechilibrat în jurul armăturii și armătura este supusă Forței de stoarcere exercitată de topirea metalului departe de centrul arborelui se deplasează spre exterior în direcția radială, obținându-se astfel un material compozit degradat cu o suprafață exterioară îmbogățită și întărită. Studiul a subliniat că cu cât este mai mare tensiunea curentului alternativ trifazat aplicat de agitatorul electromagnetic, cu atât este mai mare forța de forfecare între interfața lichid / solid și topitură și cu atât este mai ușor să fie împinse particulele Mg2Si primare la suprafața exterioară a specimenului și stratul de segregare Cu cât este mai gros.
- Metoda de control pentru distribuția uniformă a armăturii: Pentru materialul compozit armat general, distribuția uniformă a armăturii în matrice este foarte importantă. Consolidarea agitării topiturii este mijlocul fundamental pentru atingerea obiectivului de omogenizare a armăturii. Iată câteva metode eficiente de amestecare:
- Agitare mecanică: Agitarea mecanică este cea mai tradițională metodă de agitare a topiturii. Datorită limitării materialului lamelor agitatorului, există puține exemple de metode de agitare mecanică utilizate în aliajele de oțel. Acordați atenție amestecării mecanice a topiturii: choose Alegeți în mod rezonabil materialul și forma lamei agitatorului: lama agitatorului este direct în contact cu topitura, ceea ce poate provoca cu ușurință poluarea aliajului. Pentru aliajele neferoase, ar trebui utilizate lame neferoase sau lame de oțel trebuie acoperite cu un strat exterior (cum ar fi un strat de argilă albă). Și direcția de rotație a lamei trebuie selectată în funcție de densitatea particulelor armăturii. MixingBun amestec: Adâncimea de imersie a lamelor agitatorului trebuie controlată corespunzător pentru a produce un vortex stabil. Agitarea tijei de agitare sau a lamelor de agitator necorespunzătoare va crește probabilitatea ca armătura să fie respinsă de topitură, deteriorând astfel distribuția armăturii în matrice. ③Timp de amestecare: După adăugarea armăturii, timpul de agitare trebuie să fie cât mai lung posibil, iar timpul de așteptare pentru turnare după agitare trebuie să fie cât mai scurt posibil. Există un brevet american pentru „un dispozitiv pentru amestecarea particulelor solide într-un lichid”, care afirmă că materialul compozit produs de acest dispozitiv „depășește defectele comune ale materialelor compozite întărite cu particule și are un timp de amestecare scurt, o productivitate ridicată și cost scăzut."
- Agitarea gazului: amestecarea topiturii cu o cantitate mare de gaz generată de fluxul extern de gaz sau de reacția topirii poate atinge și scopul de a distribui uniform armătura în topitură. Oamenii de știință au folosit o cantitate mare de gaz generat de reacția in situ pentru a agita topitura și au preparat compozite Al3Zr (p). Al2O3 (p) / A356 și (TiB2 + TiAl3) / AlSi6Cu4 cu întăriri uniform distribuite.
- Tratament cu ultrasunete de înaltă energie: Oamenii de știință adaugă particule de SiC la suprafața topirii aliajului ZA27 la 600 ° C și tratează topitura cu ultrasunete de înaltă energie timp de 60-90 de ani pentru a obține o suspensie de topire a particulelor și distribuția totală a particulelor (ca -cast) se obține. Material compozit SiCp / ZA27 uniform. Studiul consideră că atenuarea cu amplitudine finită a ultrasunetelor de mare energie din topitură determină un anumit gradient de presiune sonoră în topitură să formeze un jet de fluid, care părăsește direct fața finală a cornului cu ultrasunete și se formează în întregul topit. Circulația (adică efectul curentului acustic), viteza curentului acustic poate atinge de 10 până la 103 ori viteza de convecție a topiturii. În timp ce fluxul sonor îndepărtează impuritățile de pe suprafața particulelor de întărire, acesta trimite și particulele în partea adâncă a topiturii și le face dispersate uniform.
- Caracteristici de performanță a topiturii compozite și puncte cheie ale procesului de formare: Cea mai mare diferență între topitura compusă și topitura obișnuită este introducerea particulelor solide de armare. Datorită introducerii particulelor solide, vâscozitatea topiturii compozite va crește brusc și semnificativ odată cu urmele de TiC și TiB2, provocând o schimbare bruscă a vâscozității topiturii de aluminiu. Oamenii de știință au subliniat teoria formării turnării. Vâscozitatea metalului lichid are un efect semnificativ asupra caracteristicilor de curgere ale metalului din matriță, umplerea matriței, plutirea gazului din metalul lichid și alimentarea metalului.
Pentru a obține un produs sonor, procesul de formare a unui topit compozit cu o creștere bruscă a vâscozității trebuie să facă față următoarelor două probleme:
- ①Îmbunătățiți fluiditatea topiturii și creșteți capacitatea de umplere a acesteia;
- ② Preveniți topirea de la inhalarea gazului și întăriți îndepărtarea gazului din topitură.
Manchang Gui și alții au dezvoltat un proces de turnare a presiunii diferențiale în vid, constând dintr-un ecran de filtrare și un canal. Topitura compozită este umplută direct în matriță după trecerea prin filtru. După ce metalul topit este umplut, sprue-ul are întotdeauna un efect de presiune și este în cele din urmă solidificat, astfel încât să poată alimenta turnarea. Caracteristicile acestui proces de turnare se manifestă în mod specific prin:
- EliminateEliminați esențial sursa de gaz și eliminați practic defectele porilor generate în procesul de turnare;
- ②Simplificați sistemul de turnare, greutatea sistemului de turnare și greutatea turnării sunt reduse din turnarea fără vid fără vid (5-10): 1 (0.5 ~ 1.5): 1;
- ③Depășind deficiențele fluidității slabe a topiturii compozite, poate produce piese turnate complexe compozite cu pereți subțiri.
Perspectivă
Metoda de turnare este una dintre cele mai promițătoare metode de preparare a materialelor compozite. Cercetările viitoare ar trebui să se concentreze pe următoarele aspecte:
- ① Pentru matricea de metale feroase, selectați armături pe baza cerințelor de performanță ale materialelor compozite;
- ② Elaborați metode de pregătire mai ușor de realizat și de aplicat producției industriale;
- Reduce Reduceți semnificativ costurile de material și de fabricație ale produselor compozite;
- ④ Cercetarea recuperării materialelor compozite Reutilizarea tehnologiei.
Prin urmare, se crede că metoda de turnare va face mult în producția de produse compozite rezistente la uzură și rezistente la căldură.
Materialul compozit cu matrice metalică este un material multifazic cu o a doua fază specială dispersată într-o matrice metalică sau din aliaj. A doua fază cu proprietăți fizice și mecanice speciale sporește foarte mult rezistența, duritatea, rezistența la uzură, rezistența la căldură și alte proprietăți ale materialului. Prin urmare, această a doua fază este numită și faza de întărire. Faza de armare este de obicei împărțită în faza de armare a particulelor și faza de armare cu fibre (mustăți). Din motive precum prețul armăturii și tehnologia compozitului, majoritatea materialelor compozite realizate prin metoda turnării sunt armate cu particule.
Vă rugăm să păstrați sursa și adresa acestui articol pentru reimprimare: Tehnologia de preparare a compozitului cu matrice metalică armată cu particule prin metoda turnării
Minghe Compania de turnare sub presiune sunt dedicate fabricării și furnizează piese de turnare de calitate și de înaltă performanță (gama de piese turnate sub presiune din metal include în principal Turnare sub presiune cu perete subțire,Hot Cast casting sub presiune,Turnare sub presiune în cameră rece), Serviciu rotund (Serviciu de turnare sub presiune,Prelucrare Cnc,Fabricarea mucegaiului, Tratament de suprafață). Orice cerință personalizată de turnare sub presiune din aluminiu, magneziu sau turnare sub presiune din Zamak / zinc și alte cerințe de turnare sunt binevenite să ne contacteze.
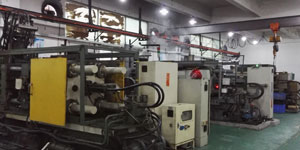
Sub controlul ISO9001 și TS 16949, toate procesele sunt efectuate prin sute de mașini avansate de turnare sub presiune, mașini cu 5 axe și alte facilități, variind de la blastere la mașini de spălat Ultra Sonic. Minghe nu numai că are echipamente avansate, dar are o echipă de ingineri cu experiență, operatori și inspectori pentru a face realitatea designul clientului.
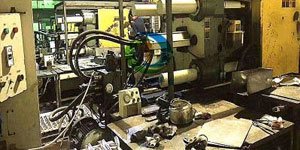
Producător contract de piese turnate sub presiune. Capacitățile includ piese de turnare sub presiune din aluminiu cu cameră rece de la 0.15 lbs. la 6 lbs., schimbare rapidă configurată și prelucrare. Serviciile cu valoare adăugată includ lustruire, vibrare, debavurare, sablare, vopsire, placare, acoperire, asamblare și scule. Materialele lucrate includ aliaje precum 360, 380, 383 și 413.
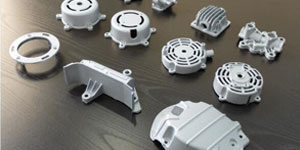
Asistență la proiectarea turnării sub presiune din zinc / servicii de inginerie simultană. Producător personalizat de piese turnate sub presiune din zinc. Pot fi fabricate piese turnate în miniatură, piese turnate sub presiune înaltă, piese turnate multi-glisante, piese turnate convenționale, piese turnate sub formă de unități și piese turnate independente și piese turnate sigilate în cavitate. Piesele turnate pot fi fabricate în lungimi și lățimi de până la toleranță de +/- 24 in.
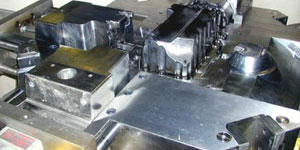
Producător certificat ISO 9001: 2015 de magneziu turnat sub presiune, capabilitățile includ turnare sub presiune cu magneziu de înaltă presiune de până la 200 tone cameră fierbinte și 3000 tone cameră rece, proiectare scule, lustruire, turnare, prelucrare, vopsire cu pulbere și lichide, QA complet cu capacități CMM , asamblare, ambalare și livrare.
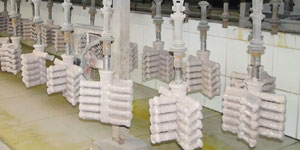
Certificat ITAF16949. Serviciul de turnare suplimentar include investiții de turnătorie,turnare cu nisip,Turnarea gravitației, Pierdere spumă turnare,Turnare centrifugă,Turnarea în vid,Turnare permanentă a matriței, .Capacitățile includ EDI, asistență tehnică, modelare solidă și procesare secundară.
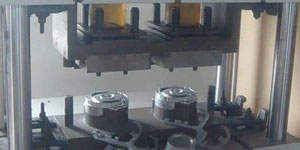
Industrii de turnare Părți Studii de caz pentru: Mașini, biciclete, aeronave, instrumente muzicale, ambarcațiuni, dispozitive optice, senzori, modele, dispozitive electronice, carcase, ceasuri, mașini, motoare, mobilier, bijuterii, jiguri, telecomunicații, iluminat, dispozitive medicale, dispozitive fotografice, Roboți, sculpturi, echipamente de sunet, echipamente sportive, scule, jucării și multe altele.
Ce vă putem ajuta să faceți în continuare?
∇ Accesați pagina principală pentru China turnare sub presiune
→Piese de turnare-Aflați ce am făcut.
→ Ralated Tips About Servicii de turnare sub presiune
By Producător de turnare sub presiune Minghe | Categorii: Articole utile |Material Etichete: Turnare din aluminiu, Turnarea zincului, Turnarea cu magneziu, Turnare cu titan, Turnare din oțel inoxidabil, Turnare din alamă,Turnarea bronzului,Distribuirea videoclipului,Istoricul companiei,Turnare din aluminiu | Comentarii dezactivate