Colectarea defectelor comune și a măsurilor preventive la carburare și stingere
Carburarea și stingerea este de fapt un proces compozit, și anume carburarea + stingerea. Adesea suntem obișnuiți să vorbim despre cele două împreună, deoarece cele două procese care sunt finalizate pe același echipament sunt cele mai întâlnite în producție (dar există, de asemenea, răcirea aerului de carburare, răcirea lentă a carburării și apoi procesele de reîncălzire și stingere, și Procesul) Apoi unele dintre fenomenele nedorite întâlnite în producție sunt probleme de carburare, altele sunt probleme de stingere, iar altele sunt rezultatul efectelor combinate ale carburării și stingerii.
Știm că toate procesele de tratament termic sunt inseparabile de trei aspecte esențiale: încălzirea, conservarea căldurii și răcirea. În detaliu, inclusiv temperatura de încălzire, rata de încălzire, timpul de menținere, rata de răcire și, bineînțeles, problemele legate de atmosferă. Deci, odată ce ceva nu merge bine, vom analiza în mod obișnuit cauza din aceste aspecte.
Pentru carburare și stingere, testăm adesea acești indicatori: aspectul suprafeței produsului, duritatea suprafeței, duritatea miezului, adâncimea stratului carburat, (adâncimea efectivă a stratului întărit, adâncimea stratului complet întărit) structura metalografică și deformarea. Să ne împărtășim opiniile despre acești indicatori, respectiv.
1. Problema aspectului
1. Scară de oxid: Aceasta se datorează în principal scurgerilor de echipamente, gazului purtător impur sau conținutului de apă. Trebuie să găsesc motivul din echipamente și materii prime.
2. Cealaltă problemă cea mai supărătoare este problema petelor, care este, de asemenea, o cerință nouă și provocatoare pentru tratamentul termic în epoca modernă. Motivele sunt complicate și foarte profunde.
Două. Duritate necalificată
1. Duritate ridicată (nediscutată)
2. Duritate scăzută: Există două situații, una este carburarea necalificată. Motivul poate fi faptul că stratul carburat este prea superficial pentru a îndeplini cerințele desenelor (stratul carburat nu este infiltrat) sau scala de detecție selectată depășește intervalul tolerabil al stratului carburat existent, ceea ce va defecta stratul carburat.
Soluție: Completați filtrarea și urmați rigla de inspecție. JBT 6050-2006 "Principii generale pentru inspecția durității tratamentului termic al pieselor din oțel" Adâncimea stratului carburat este de fapt o funcție de temperatură, timp și potențial de carbon. Din factorii de mai sus, putem lua în considerare modalități de a crește temperatura de încălzire, de a prelungi timpul de menținere și de a crește potențialul de carburare. (Desigur, ajustarea fiecărui parametru ar trebui să fie pe deplin combinată cu cerințele propriilor echipamente și produse) Poate fi, de asemenea, din cauza existenței unor organizații non-cai la suprafață. O altă situație apare atunci când duritatea este scăzută, adică carburarea este calificată, dar stingerea este necalificată. În general, nu este stins. Această situație este cea mai complicată, după cum se spune zicala: tratamentul termic se bazează pe încălzire timp de trei sferturi și răcire timp de șapte sferturi. De asemenea, reflectă poziția pe care o ocupă procesul de răcire în procesul de tratare termică.
Următorul este un test comparativ pe care l-am proiectat. Puteți discuta despre efectul răcirii asupra durității.
Luați 3 grupe de bare de testare cu materiale diferite, dar aceleași specificații și dimensiuni, a căror dimensiune este Φ20mmX100mm. (Numim bara de testare nr. 20 din oțel nr. 1, bara de testare 20Cr nr. 2 și bara de testare 20CrMnTi nr. 3). Barele de testare sunt carburate în aceeași căldură folosind același proces. Presupunând că adâncimea stratului carburat al celor trei bare de testare este de 0.6-0.7 mm (ps: presupunerea este stabilită doar într-o stare ideală).
Vă rugăm să luați în considerare următoarele condiții:
A. Terminați stingerea în aceleași condiții
b. Mediul de stingere este ulei lent, ulei rapid, apă limpede, apă sărată
c. În același mediu fără agitare și agitare intensă și stingere, cele trei bare de testare sunt luate fiecare în două grupe pentru testare.
După terminarea carburării, grupul A este stins la 800 de grade, iar grupul B este stins la 860 grade. Care este ordinea durității lor de la mare la scăzut? Cum să ordonați stratul întărit (cu 550HV1.0 ca limită) de la adânc la superficial? Luați două bare de testare din același material și comparați și testați, care grupă poate obține o duritate mai mare de stingere și o adâncime efectivă a stratului întărit?
Se poate concluziona din rezultatele testelor de mai sus că adâncimea stratului carburat nu este egală cu adâncimea stratului efectiv întărit, iar adâncimea efectivă a stratului întărit este afectată de întărirea materialului, de temperatura de stingere și de răcire rată. Caracteristicile de răcire și intensitatea de stingere a mediului de răcire afectează, de asemenea, efectul de stingere. Cele de mai sus sunt opiniile oamenilor, dacă există o incompletitudine, puteți adăuga. Desigur, efectul de dimensiune al pieselor afectează și efectul de întărire.
Cred că un inspector cu experiență poate determina cauza reală a durității scăzute prin organizarea și combinarea altor metode de testare și apoi poate găsi adevărata cauză pentru rezolvarea acesteia; ca meșter, dacă sunteți familiarizați cu caracteristicile materiilor prime convenționale din metal, Performanța de răcire a propriului echipament și mediu a atins un anumit nivel de recunoaștere, ceea ce este de mare ajutor pentru formularea proceselor de carburare și stingere.
3. Duritate neuniformă: temperatura uniformă a cuptorului (care afectează uniformitatea carburării), structura echipamentului, circulația atmosferei, încărcarea cuptorului (care afectează uniformitatea stratului de carburare și, în același timp, afectează uniformitatea de stingere)
4. Duritatea miezului este necalificată. Prea ridicat: temperatura de stingere este prea ridicată, durabilitatea materialului este prea bună, limita superioară a compoziției de carbon și aliaj și rata medie de răcire este prea rapidă. Duritatea miezului este scăzută: exact opusul.
Exemplu de partajare: 20 # produs de oțel de 1.5 mm, cerințe: strat de infiltrare 0.2-0.4 mm miez HV250, unii prieteni din aceeași industrie cred că cerințele sunt nerezonabile, (toată lumea ar trebui să știe că cea mai mare duritate a martensitei de oțel de 20 # va fi HV450- 470) Pentru a rezolva această problemă, trebuie mai întâi să înțelegem caracteristicile acestui material: inclusiv întărirea și întărirea.
Apoi combinați factorii menționați mai sus care afectează efectul de stingere și găsiți modalități de încălzire și răcire. În acest caz, materialul este fix. Ne putem da seama de o cale de la temperatura de răcire și rata de răcire. Acest producător folosește ulei de viteză excesivă. Dacă reducerea intensității de stingere nu îndeplinește cerințele, putem reduce și temperatura de stingere. Metodă.
Încă aceeași propoziție, de la 860-760 grade, (când temperatura este redusă la un anumit nivel, o anumită cantitate de ferită va fi precipitată din austenita supercooled din miez, iar duritatea va scădea în acest moment. temperatura scade, cu cât precipita cantitatea de ferită, cu atât duritatea scade.
Iată o reamintire: este necesar să combinați pe deplin condițiile existente ale echipamentului și să faceți furori cu privire la indicele favorabil special al permeabilității de mică adâncime.
3. Stratul carburat sau stratul carburat eficient este mai profund și mai superficial
După cum sa menționat mai devreme, adâncimea stratului de infiltrare este o funcție cuprinzătoare a temperaturii, a timpului și a concentrației de carbon. Pentru a rezolva această problemă, trebuie să începem cu temperatura de încălzire, viteza de încălzire, timpul de menținere, viteza de răcire și controlul gradientului de concentrație de carbon în stratul de carbon. Cu cât temperatura este mai ridicată, cu atât este mai mare timpul și cu cât este mai mare potențialul de carbon, cu atât stratul de infiltrație este mai adânc și invers.
Dar, de fapt, este mult mai mult decât atât de simplu. Pentru a proiecta un proces de carburare, trebuie să luați în considerare și echipamentul, capacitatea cuptorului, caracteristicile uleiului, structura metalografică, întărirea materialului, gradientul de concentrație de carbon în stratul carburat și viteza de răcire. Și mulți alți factori. Acest lucru poate fi analizat cu referire la situația anterioară de duritate scăzută și nu va fi explicat în profunzime.
În al patrulea rând, organizarea metalografică
Martensit excesiv: materia primă are cereale grosiere sau nu este normalizată, iar temperatura de carburare este prea mare. Soluție: normalizare sau normalizare multiplă (se recomandă ca temperatura de normalizare să fie cu 20-30 de grade mai mare decât temperatura de carburare) Dacă este posibil, luați în considerare carburarea și răcirea lentă și apoi reîncălzirea și stingerea
Paralimpic excesiv: temperatura de stingere este prea mare, conținutul de carbon din austenită este prea mare (potențialul de carbon este prea mare). Soluție: Difuzarea completă și condițiile permise pot reduce temperatura de stingere, temperarea la temperaturi ridicate și reîncălzirea și stingerea sau tratamentul criogen.
Carbid excesiv: conținut de carbon prea mare în austenită (potențial de carbon prea mare), proces de răcire prea lent, precipitații de carbură
Soluție: complet difuză, controlați viteza de răcire, reduceți diferența de temperatură dintre carburare și stingere și utilizați stingerea temperaturii scăzute sau sub-temperatură cât mai puțin posibil. Dacă trebuie utilizat acest proces, sarcina cuptorului trebuie controlată. Să ne imaginăm: același echipament este carburat la 920 ° C și stins la 820 ° C. Capacitatea cuptorului este de 1000 kg și 600 kg, iar rata de răcire este aceeași? Care va dura mai mult? Care clasă de carbură este mai mare?
Cinci. Oxidare internă și fără cal
Oxidarea internă: este reacția dintre elementele de aliere precum cromul, manganul și molibdenul din oțel și atmosfera oxidantă din atmosferă (în principal oxigen, apă, dioxid de carbon), care epuizează elementele de aliere din matrice, rezultând o scădere în întărirea materialului. Structura rețelei negre poate fi văzută la microscop, esența sa este structura troostitei obținută prin epuizarea elementelor de aliere din matrice și scăderea durabilității.
Soluția este de a găsi modalități de a crește rata de răcire a mediului, de a spori intensitatea de stingere și de a reduce atmosfera oxidantă din cuptor (asigurați puritatea materialelor brute și auxiliare de carburare, minimizați cantitatea de aer echilibrat, controlați echilibrul umiditatea aerului și asigurați-vă că echipamentul nu se scurge. Evacuare suficientă) Echipamentul convențional este dificil de eliminat. Se spune că echipamentul de carburare cu vid de joasă presiune poate fi complet eliminat. În plus, împușcătura puternică poate reduce, de asemenea, nivelul de oxidare internă.
Am citit opiniile unor experți, iar unii cred că amoniacul excesiv în procesul de carbonitridare poate provoca, de asemenea, non-cal. Eu personal am o altă părere cu privire la acest lucru: poate este cauzată de un conținut excesiv de apă în amoniac? Deoarece am fost expus la multe procese de carbonitridare, nu s-a găsit nici un țesut evident non-cal la inspectarea produsului. (Dar nu cred că acest punct de vedere este greșit) Unele industrii de mașini străine acordă o mare importanță oxidării interne, în special industriei de angrenaje. La nivel intern, adâncimea este, în general, necesară să nu fie mai mare de 0.02 mm, după cum este calificat.
Non-martensitic: structura non-martensitic apare pe suprafața stratului carburat din cauza problemelor de carburare sau de stingere după stingere, cum ar fi ferita, bainita și, desigur, troostita de tip oxidare internă. Mecanismul de generare este similar cu oxidarea internă, iar soluția este similară.
Şase. Problema deformării
Aceasta este o problemă de sistem și este, de asemenea, cea mai supărătoare problemă pentru personalul nostru angajat în tratamentul termic. Este garantat din mai multe aspecte ale mediului de răcire a procesului materiei prime. Conținutul de mai sus este doar o experiență personală. Dacă există vreo inconsecvență, sunteți binevenit să mă corectați, vă mulțumesc.
Vă rugăm să păstrați sursa și adresa acestui articol pentru reimprimare:Colectarea defectelor comune și a măsurilor preventive la carburare și stingere
Minghe Compania de turnare sub presiune sunt dedicate fabricării și furnizează piese de turnare de calitate și de înaltă performanță (gama de piese turnate sub presiune din metal include în principal Turnare sub presiune cu perete subțire,Hot Cast casting sub presiune,Turnare sub presiune în cameră rece), Serviciu rotund (Serviciu de turnare sub presiune,Prelucrare Cnc,Fabricarea mucegaiului, Tratament de suprafață). Orice cerință personalizată de turnare sub presiune din aluminiu, magneziu sau turnare sub presiune din Zamak / zinc și alte cerințe de turnare sunt binevenite să ne contacteze.
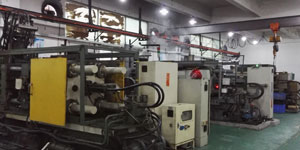
Sub controlul ISO9001 și TS 16949, toate procesele sunt efectuate prin sute de mașini avansate de turnare sub presiune, mașini cu 5 axe și alte facilități, variind de la blastere la mașini de spălat Ultra Sonic. Minghe nu numai că are echipamente avansate, dar are o echipă de ingineri cu experiență, operatori și inspectori pentru a face realitatea designul clientului.
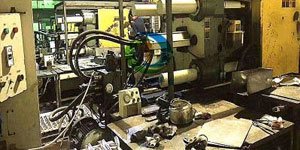
Producător contract de piese turnate sub presiune. Capacitățile includ piese de turnare sub presiune din aluminiu cu cameră rece de la 0.15 lbs. la 6 lbs., schimbare rapidă configurată și prelucrare. Serviciile cu valoare adăugată includ lustruire, vibrare, debavurare, sablare, vopsire, placare, acoperire, asamblare și scule. Materialele lucrate includ aliaje precum 360, 380, 383 și 413.
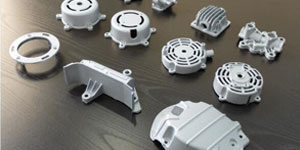
Asistență la proiectarea turnării sub presiune din zinc / servicii de inginerie simultană. Producător personalizat de piese turnate sub presiune din zinc. Pot fi fabricate piese turnate în miniatură, piese turnate sub presiune înaltă, piese turnate multi-glisante, piese turnate convenționale, piese turnate sub formă de unități și piese turnate independente și piese turnate sigilate în cavitate. Piesele turnate pot fi fabricate în lungimi și lățimi de până la toleranță de +/- 24 in.
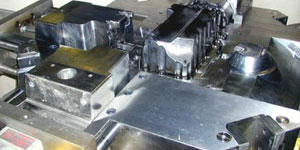
Producător certificat ISO 9001: 2015 de magneziu turnat sub presiune, capabilitățile includ turnare sub presiune cu magneziu de înaltă presiune de până la 200 tone cameră fierbinte și 3000 tone cameră rece, proiectare scule, lustruire, turnare, prelucrare, vopsire cu pulbere și lichide, QA complet cu capacități CMM , asamblare, ambalare și livrare.
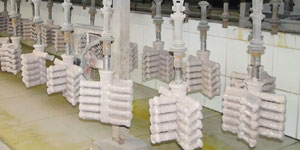
Certificat ITAF16949. Serviciul de turnare suplimentar include investiții de turnătorie,turnare cu nisip,Turnarea gravitației, Pierdere spumă turnare,Turnare centrifugă,Turnarea în vid,Turnare permanentă a matriței, .Capacitățile includ EDI, asistență tehnică, modelare solidă și procesare secundară.
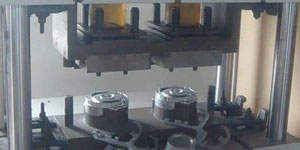
Industrii de turnare Părți Studii de caz pentru: Mașini, biciclete, aeronave, instrumente muzicale, ambarcațiuni, dispozitive optice, senzori, modele, dispozitive electronice, carcase, ceasuri, mașini, motoare, mobilier, bijuterii, jiguri, telecomunicații, iluminat, dispozitive medicale, dispozitive fotografice, Roboți, sculpturi, echipamente de sunet, echipamente sportive, scule, jucării și multe altele.
Ce vă putem ajuta să faceți în continuare?
∇ Accesați pagina principală pentru China turnare sub presiune
→Piese de turnare-Aflați ce am făcut.
→ Ralated Tips About Servicii de turnare sub presiune
By Producător de turnare sub presiune Minghe | Categorii: Articole utile |Material Etichete: Turnare din aluminiu, Turnarea zincului, Turnarea cu magneziu, Turnare cu titan, Turnare din oțel inoxidabil, Turnare din alamă,Turnarea bronzului,Distribuirea videoclipului,Istoricul companiei,Turnare din aluminiu | Comentarii dezactivate