Procesul de tratare termică a pieselor matriței
Diferite tipuri de oțel sunt folosite ca matrițe din plastic, iar compoziția lor chimică și proprietățile mecanice sunt diferite, astfel că traseele procesului de fabricație sunt diferite; în mod similar, diferite tipuri de oțeluri din material plastic folosesc procese de tratare termică diferite. Această secțiune introduce în principal calea procesului de fabricație și caracteristicile procesului de tratare termică a matriței din plastic.
1. Traseul procesului de fabricație al matriței din plastic
1. Matrite din oțel cu emisii reduse de carbon și aliaj cu conținut scăzut de carbon
De exemplu, ruta de procesare a 20, 20Cr, 20CrMnTi și a altor oțeluri este: golire → matriță de forjare → tăiere → prelucrare mecanică brută → formare prin extrudare la rece → recoacere de recristalizare → finisare mecanică → carburare → călire, călire → șlefuire și lustruire → Asamblare .
2. Matriță din oțel carburat cu aliaj înalt
De exemplu, calea de proces a oțelului 12CrNi3A și 12CrNi4A este: blanking → matriță de forjare blank → normalizare și temperare la temperatură ridicată → prelucrare mecanică brută → temperare la temperatură ridicată → finisare → carburare → stingere și călire → măcinare și lustruire → asamblare.
3. Matriță din oțel călit și călit
De exemplu, ruta de procesare a 45, 40Cr și a altor oțeluri este: ștanțare → șlefuire a matrițelor → recoacere → prelucrare mecanică brută → călire și călire → finisare mecanică → pansament, lustruire → asamblare.
4. Matrite din oțel pentru scule din carbon și oțel aliat pentru scule
De exemplu, ruta de procesare a T7A ~ T10A, CrWMn, 9SiCr și a altor oțeluri este: blanking → forjare în matriță blank → recoacere sferoidantă → prelucrare mecanică brută → recoacere de reducere a stresului → semi-finisare mecanică → finisare mecanică → stingere, călire → șlefuire Lustruire → asamblare.
5. Matrita din otel pretermit
De exemplu, 5NiSiCa, 3Cr2Mo (P20) și alte oțeluri. Pentru cei prelucrați direct cu stocuri de bare, acestea au fost pre-întărite datorită stării de aprovizionare și pot fi prelucrate și formate direct, apoi lustruite și asamblate. Pentru cei care trebuie să fie forjați în spații libere și apoi prelucrați în formare, calea procesului este: blanking → forjare → recoacere sferoidantă → rabotare sau frezare pe șase fețe → tratament pre-întărire (34 ~ 42HRC) → degroșare mecanică → recoacere de reducere a stresului → Finisare mecanică → lustruire → asamblare.
Caracteristicile de tratament termic ale matrițelor din plastic
(1) Caracteristicile de tratament termic ale matriței din oțel carburat
- Pentru matrițele din plastic cu duritate ridicată, rezistență ridicată la uzură și cerințe de rezistență ridicată, oțelul carburat trebuie utilizat pentru fabricare, iar carburarea, stingerea și temperarea la temperaturi scăzute sunt tratamentul termic final.
- Cerințe pentru stratul carburat, în general grosimea stratului carburat este de 0.8 ~ 1.5 mm, la presarea materialelor plastice care conțin umpluturi dure, grosimea stratului carburat al matriței trebuie să fie de 1.3 ~ 1.5 mm, la presarea materialelor plastice moi, stratul carburat Grosimea este de 0.8 ~ 1.2 mm. Conținutul de carbon al stratului carburat este de preferință de la 0.7% la 1.0%. Dacă se utilizează co-infiltrarea cu carbon și azot, rezistența la uzură, rezistența la coroziune, rezistența la oxidare și proprietățile antiaderente vor fi mai bune.
- Temperatura de carburare este în general de 900 ~ 920 ℃, iar matrițele mici cu cavități complexe pot dura 840 ~ 860 ℃ carbonitridare la temperatură medie. Timpul de conservare a căldurii de carburare este de 5-10 ore, care trebuie selectat în funcție de cerințele pentru grosimea stratului carburat. Procesul de carburare este potrivit pentru adoptarea procesului de carburare ierarhic, adică stadiul de temperatură ridicată (900 x 920 ℃) este în principal pentru a se infiltra rapid în suprafața piesei; etapa de temperatură medie (820 ~ 840 ℃) este în principal creșterea grosimii stratului carburat. În stratul carburat se stabilește o distribuție uniformă și rezonabilă a gradientului de concentrație de carbon, care este convenabilă pentru stingerea directă.
- Procesul de stingere după carburare este diferit în funcție de tipul de oțel. După carburare, poate fi utilizat separat: reîncălzire și stingere; stingerea directă după carburarea gradată (cum ar fi oțelul carburat din aliaj); stingerea directă după carbonitrurare la temperatură medie (cum ar fi matrițele industriale de mică precizie formate prin extrudarea la rece a fierului pur sau a oțelului cu emisii scăzute de carbon); stingerea aerului după carburare (cum ar fi matrițele mari și mijlocii din oțel carburat cu aliaj înalt).
(2) Tratamentul termic al matriței din oțel călit
- Pentru matrițele cu forme mai complexe, tratamentul termic trebuie efectuat după prelucrarea brută și apoi terminarea prelucrării pentru a asigura cea mai mică deformare în timpul tratamentului termic. Pentru matrițele de precizie, deformarea trebuie să fie mai mică de 0.05%.
- Cerințele de suprafață ale cavității matriței din plastic sunt foarte stricte, deci în timpul procesului de stingere și încălzire este necesar să se asigure că suprafața cavității nu este oxidată, decarburată, nu corodată, supraîncălzită etc. Ar trebui încălzită într-un cuptor cu atmosferă de protecție sau într-un cuptor cu baie de sare după o dezoxidare strictă. Dacă pentru încălzire se folosește un cuptor obișnuit cu rezistență de tip cutie, trebuie aplicat un agent de protecție pe suprafața cavității matriței, iar rata de încălzire trebuie controlată. Mediu de răcire, controlați rata de răcire pentru a evita deformarea, crăparea și casarea în timpul procesului de stingere. În general, stingerea băii fierbinți este mai bună și poate fi utilizată și stingerea pre-răcire.
- După stingere, acesta trebuie temperat în timp, temperatura de temperare trebuie să fie mai mare decât temperatura de lucru a matriței, iar timpul de temperare trebuie să fie suficient. Lungimea depinde de materialul matriței și dimensiunea secțiunii, dar cel puțin 40-60min.
(3) Tratamentul termic al matriței din oțel pre-întărit
- Oțelul pre-întărit este furnizat într-o stare pre-întărită și, în general, nu necesită tratament termic, dar uneori trebuie modificat prin forjare, iar matrița matriță după forjare modificată trebuie tratată termic.
- Tratamentul pre-termic al oțelului pre-întărit adoptă de obicei recoacerea sferoidantă, scopul este de a elimina stresul de forjare, de a obține o structură sferică uniformă de perlită, de a reduce duritatea, de a crește plasticitatea și de a îmbunătăți performanța de tăiere sau extrudarea la rece a formei semifabricatului.
- Procesul de pre-întărire a oțelului pre-întărit este simplu, dintre care majoritatea adoptă un tratament de stingere și călire, iar structura de sorbit temperat se obține după stingere și călire. Temperarea la temperaturi ridicate are o gamă largă de temperatură care poate îndeplini diversele cerințe de duritate de lucru ale matriței. Datorită întăririi bune a acestui tip de oțel, răcirea cu ulei, răcirea cu aer sau stingerea gradată a sării de azot pot fi utilizate în timpul stingerii. Tabelul 3-27 prezintă procesul de pre-întărire a unor oțeluri pre-întărite pentru referință.
Numărul de oțel | Temperatura de încălzire / ℃ | metoda de răcire | Temperatura de temperare / ℃ | Duritate pre-întărităHRC |
3Cr2Mo | 830 ~ 840 | Răcirea uleiului sau clasificarea 160 ~ 180 ℃ azotat | 580 ~ 650 | 28 ~ 36 |
5NiSCa | 880 ~ 930 | Răcitor de ulei | 550 ~ 680 | 30 ~ 45 |
8Cr2MnWMoVS | 860 ~ 900 | Răcire cu ulei sau aer | 550 ~ 620 | 42 ~ 48 |
P4410 | 830 ~ 860 | Răcirea uleiului sau clasificarea nitraților | 550 ~ 650 | 35 ~ 41 |
SM1 | 830 ~ 850 | Răcitor de ulei | 620 ~ 660 | 36 ~ 42 |
(4) Tratamentul termic al matriței din plastic din oțel întărit
- Procesul de tratament termic al oțelului de întărire în vârstă este împărțit în două etape de bază. În primul rând, se efectuează tratamentul soluției, adică oțelul este încălzit la o temperatură ridicată pentru a dizolva diferite elemente de aliere în austenită și, după finalizarea austenitei, structura martensitei se obține prin stingere. Al doilea pas este tratamentul de îmbătrânire, iar îmbătrânirea este utilizată pentru a întări proprietățile mecanice care îndeplinesc cerințele finale.
- Încălzirea tratamentului soluției se efectuează în general într-un cuptor cu baie de sare sau într-un cuptor cu cutie. Timpul de încălzire poate fi respectiv: 1min / mm, 2 ~ 2.5min / mm, stingerea adoptă răcirea cu ulei, iar oțelul cu o bună întărire poate fi, de asemenea, răcit cu aer. Dacă temperatura finală de forjare poate fi controlată cu exactitate la forjarea matriței, stingerea soluției poate fi efectuată direct după forjare.
- Tratamentul de îmbătrânire se efectuează cel mai bine într-un cuptor cu vid. Dacă se realizează într-un cuptor cu cutie, pentru a preveni oxidarea suprafeței cavității mucegaiului, trebuie să se treacă în cuptor o atmosferă de protecție sau ar trebui să se utilizeze pulbere de oxid de aluminiu, pulbere de grafit, resturi de fontă. cutie. Îmbătrânirea în condiții de protecție. Încălzirea de protecție a ambalajului ar trebui să extindă în mod corespunzător timpul de conservare a căldurii, altfel va fi dificil să se obțină efectul de îmbătrânire. Specificațiile privind tratamentul termic al oțelului din matriță din plastic care se întărește parțial se poate face referire la Tabelul 3-28.
Numărul de oțel | Procesul de tratare a soluției | Procesul de tratament al îmbătrânirii | Duritatea îmbătrânirii HRC |
06Ni6CrMoVTiAl | 800 ~ 850 ℃ Răcitor de ulei | 510 ~ 530 ℃ × (6 ~ 8) h | 43 ~ 48 |
PMS | 800 ~ 850 ℃ Răcire cu aer | 510 ~ 530 ℃ × (3 ~ 5) h | 41 ~ 43 |
25CrNi3MoAl | 880 qu Stingerea apei sau răcirea cu aer | 520 ~ 540 ℃ × (6 ~ 8) h | 39 ~ 42 |
SM2 | 900 ℃ × 2h Răcitor de ulei + 700 ℃ × 2h | 510 ℃ × 10h | 39 ~ 40 |
PCR | 1050 cooling Soluție solidă răcire cu aer | 460 ~ 480 ℃ × 4h | 42 ~ 44 |
Tratarea suprafeței matrițelor din plastic
Pentru a îmbunătăți rezistența la uzură și rezistența la coroziune a suprafeței matriței din plastic, se aplică adesea un tratament adecvat al acesteia.
- Placarea cu crom a matrițelor din plastic este una dintre cele mai utilizate metode de tratare a suprafeței. Stratul de placare cu crom are o puternică capacitate de pasivare în atmosferă, poate menține luciul metalic pentru o lungă perioadă de timp și nu reacționează chimic într-o varietate de medii acide. Duritatea acoperirii atinge 1000HV, deci are o rezistență excelentă la uzură. Stratul cromat are, de asemenea, o rezistență ridicată la căldură, iar aspectul și duritatea acestuia rămân neschimbate atunci când sunt încălzite la 500 ° C în aer.
- Nitrarea are avantajele temperaturii scăzute de prelucrare (în general 550 ± 570 °), a deformării reduse a mucegaiului și a durității ridicate a stratului infiltrat (până la 1000 × 1200HV), deci este foarte potrivită și pentru tratarea suprafeței matrițelor din plastic. Gradele de oțel care conțin elemente de aliere precum crom, molibden, aluminiu, vanadiu și titan au performanțe mai bune de nitrurare decât oțelul carbon. Tratamentul cu nitrurare atunci când este utilizat ca matriță din plastic poate îmbunătăți foarte mult rezistența la uzură.
Metodele de tratare a suprafețelor adecvate pentru matrițele din plastic includ: nitrocarburare, placare cu nichel fără electrolitură, nitrură de titan cu placare ionică, carbură de titan sau carbonitrură de titan, PVD, metoda CVD depunerea filmului dur sau a filmului super dur etc.
Vă rugăm să păstrați sursa și adresa acestui articol pentru reimprimare:Procesul de tratare termică a pieselor matriței
Minghe Compania de turnare sub presiune sunt dedicate fabricării și furnizează piese de turnare de calitate și de înaltă performanță (gama de piese turnate sub presiune din metal include în principal Turnare sub presiune cu perete subțire,Hot Cast casting sub presiune,Turnare sub presiune în cameră rece), Serviciu rotund (Serviciu de turnare sub presiune,Prelucrare Cnc,Fabricarea mucegaiului, Tratament de suprafață). Orice cerință personalizată de turnare sub presiune din aluminiu, magneziu sau turnare sub presiune din Zamak / zinc și alte cerințe de turnare sunt binevenite să ne contacteze.
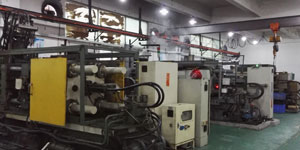
Sub controlul ISO9001 și TS 16949, toate procesele sunt efectuate prin sute de mașini avansate de turnare sub presiune, mașini cu 5 axe și alte facilități, variind de la blastere la mașini de spălat Ultra Sonic. Minghe nu numai că are echipamente avansate, dar are o echipă de ingineri cu experiență, operatori și inspectori pentru a face realitatea designul clientului.
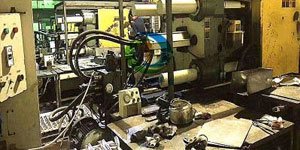
Producător contract de piese turnate sub presiune. Capacitățile includ piese de turnare sub presiune din aluminiu cu cameră rece de la 0.15 lbs. la 6 lbs., schimbare rapidă configurată și prelucrare. Serviciile cu valoare adăugată includ lustruire, vibrare, debavurare, sablare, vopsire, placare, acoperire, asamblare și scule. Materialele lucrate includ aliaje precum 360, 380, 383 și 413.
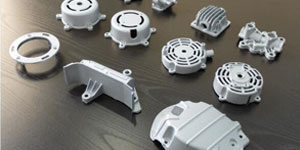
Asistență la proiectarea turnării sub presiune din zinc / servicii de inginerie simultană. Producător personalizat de piese turnate sub presiune din zinc. Pot fi fabricate piese turnate în miniatură, piese turnate sub presiune înaltă, piese turnate multi-glisante, piese turnate convenționale, piese turnate sub formă de unități și piese turnate independente și piese turnate sigilate în cavitate. Piesele turnate pot fi fabricate în lungimi și lățimi de până la toleranță de +/- 24 in.
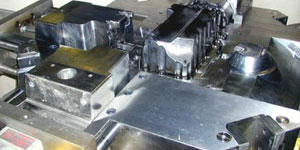
Producător certificat ISO 9001: 2015 de magneziu turnat sub presiune, capabilitățile includ turnare sub presiune cu magneziu de înaltă presiune de până la 200 tone cameră fierbinte și 3000 tone cameră rece, proiectare scule, lustruire, turnare, prelucrare, vopsire cu pulbere și lichide, QA complet cu capacități CMM , asamblare, ambalare și livrare.
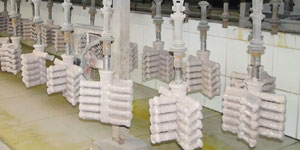
Certificat ITAF16949. Serviciul de turnare suplimentar include investiții de turnătorie,turnare cu nisip,Turnarea gravitației, Pierdere spumă turnare,Turnare centrifugă,Turnarea în vid,Turnare permanentă a matriței, .Capacitățile includ EDI, asistență tehnică, modelare solidă și procesare secundară.
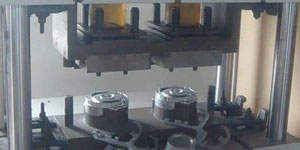
Industrii de turnare Părți Studii de caz pentru: Mașini, biciclete, aeronave, instrumente muzicale, ambarcațiuni, dispozitive optice, senzori, modele, dispozitive electronice, carcase, ceasuri, mașini, motoare, mobilier, bijuterii, jiguri, telecomunicații, iluminat, dispozitive medicale, dispozitive fotografice, Roboți, sculpturi, echipamente de sunet, echipamente sportive, scule, jucării și multe altele.
Ce vă putem ajuta să faceți în continuare?
∇ Accesați pagina principală pentru China turnare sub presiune
→Piese de turnare-Aflați ce am făcut.
→ Ralated Tips About Servicii de turnare sub presiune
By Producător de turnare sub presiune Minghe | Categorii: Articole utile |Material Etichete: Turnare din aluminiu, Turnarea zincului, Turnarea cu magneziu, Turnare cu titan, Turnare din oțel inoxidabil, Turnare din alamă,Turnarea bronzului,Distribuirea videoclipului,Istoricul companiei,Turnare din aluminiu | Comentarii dezactivate