„Alcali” și „Magneziu” pentru a îmbunătăți performanța peletelor
Peletele oxidate au o rezistență mecanică bună și proprietăți metalurgice și au devenit o sarcină indispensabilă de înaltă calitate pentru fabricarea fierului în furnal. Cu toate acestea, lipsa de aprovizionare internă cu concentrat de magnetit a făcut ca multe fabrici siderurgice domestice să utilizeze hematit importat pentru a produce pelete de oxid. În comparație cu peletele de magnetit, peletele de hematit au o temperatură de prăjire ridicată și un interval îngust (1300 ~ 1350 ℃), iar peletele au rezistență la compresiune redusă. În plus, peletele de hematit acid au proprietăți metalurgice slabe. Dintre acestea, specularita aparține unui tip important de hematit, iar performanța de prăjire și proprietățile metalurgice ale peletelor sunt mai slabe decât peletele obișnuite de hematit.
Cercetătorii au efectuat o mulțime de cercetări cu privire la modul de utilizare a hematitei pentru a produce pelete oxidate de înaltă rezistență. Studiile au arătat că adăugarea magnetitei la hematită pentru a prepara pelete oxidate poate reduce în mod eficient temperatura de prăjire preîncălzire și poate crește rezistența la compresiune a peletelor prăjite preîncălzite; adăugarea de flux pentru a produce pelete de hematit flux este, de asemenea, o soluție.
Plantele domestice de pelete folosesc în general hematit și magnetit pentru a produce pelete de înaltă rezistență, dar odată cu creșterea raportului de hematit, efectul adăugării magnetitului este mult slăbit. Adăugarea fluxului de CaO pentru a produce pelete de flux poate obține o rezistență mecanică mai mare și o reducibilitate mai bună la o temperatură mai scăzută, dar performanța la reflux la temperatură ridicată este slabă și expansiunea reducerii este gravă. Studiile timpurii au arătat că adăugarea de MgO la pelete poate reduce rata de expansiune de reducere și poate îmbunătăți performanța de reflux la temperatură ridicată.
În prezent, există relativ puține rapoarte despre efectul alcalinității și conținutului de MgO asupra rezistenței și proprietăților metalurgice ale peletelor de specularită, în special efectul alcalinității și MgO asupra proprietăților metalurgice ale peletelor. Prin urmare, acest articol Studierea efectelor alcalinității și a conținutului de MgO asupra rezistenței și proprietăților metalurgice ale peletelor de specularită are o valoare teoretică importantă pentru îmbunătățirea prăjirii peletelor și întărirea fabricării fierului în furnal.
Proprietățile materiei prime și metodele de cercetare
Materiile prime utilizate în acest experiment sunt specularita braziliană, bentonita, calcarul și magnezita. Deoarece specularita braziliană, calcarul și magnezita au dimensiuni relativ grosiere, acestea sunt măcinate la dimensiunea particulelor și suprafața specifică necesară pentru producția de pelete cu o moară cu bile în laborator. Spiegelita are un grad ridicat de fier, mai puține minerale gangue și alte impurități dăunătoare și este o materie primă de pelete de înaltă calitate. Calcarul și magnezita au un conținut scăzut de SiO2 și puține alte impurități dăunătoare. Sunt fluxuri de calciu-magneziu de înaltă calitate.
Liantul utilizat în test este bentonita de sodiu de înaltă calitate, iar indicatorii sunt după cum urmează: conținutul de montmorillonit este de 92.76%, volumul de umflare este de 20 ml / g, rata de absorbție a apei în 2 ore este de 342% și conținutul de -0.074mm ajunge la 100%.
Cercetarea experimentală include procesul de dozare, amestecare, pregătirea bilelor verzi, uscarea bilelor verzi, prăjirea cu preîncălzire a bilelor uscate și testarea performanței peletelor. Conținutul de SiO2 al peletelor finite este controlat la 3.0% ± 3.1% prin adăugarea de nisip de cuarț fin măcinat. Alcalinitatea și conținutul de MgO al peletelor finite sunt ajustate prin adăugarea de calcar și magnezit și efectele modificărilor de alcalinitate și conținut de MgO asupra rezistenței la compresiune, gradului de reducere, reducerii expansiunii, reducerii temperaturii scăzute a pulverizării și topirii la temperaturi ridicate. sunt investigate caracteristicile peletelor prăjite. Influență.
Rezultatele testelor și analiza impactului
"Efectul alcalinității și al conținutului de MgO asupra rezistenței la compresiune și porozitate." Rezistența la compresiune a peletelor este un indicator important care reflectă presiunea pe care peletele o pot suporta în timpul procesului de transport și depozitare și în cuptorul de reducere. Cuptoarele mari necesită rezistența la compresiune a peletelor mai mare de 2500 N / bucată.
Sub conținut natural de MgO, rezistența la compresiune a peletelor crește mai întâi odată cu creșterea alcalinității. Când alcalinitatea crește la 0.2, rezistența la compresiune a peletelor crește de la 2400 N / bucată de alcalinitate naturală la 3,500 N / bucată; După atingerea 0.4, rezistența la compresiune a peletelor nu mai crește. Acest lucru se datorează creșterii alcalinității CaO, Fe2O3 și SiO2, cum ar fi ferita de calciu și silicatul de calciu. Faza lichidă adecvată este favorabilă recristalizării hematitei, dar prea multă fază lichidă nu favorizează îmbunătățirea rezistenței la compresiune a peletelor. Sub alcalinitate naturală, rezistența la compresiune a peletelor scade odată cu creșterea conținutului de MgO. Acest lucru se datorează faptului că magnezita se descompune în timpul preîncălzirii și prăjirii peletelor, ceea ce crește porozitatea peletelor.
Când alcalinitatea și MgO funcționează împreună, sub același conținut de MgO, efectul alcalinității asupra rezistenței la compresiune a peletelor calcinate este practic același cu efectul alcalinității asupra rezistenței la compresiune a peletelor sub conținutul natural de MgO, adică rezistența la compresiune a peletelor. Rezistența crește mai întâi odată cu creșterea alcalinității. După ce alcalinitatea atinge o anumită valoare, rezistența la compresiune a peletelor nu mai crește semnificativ; sub aceeași alcalinitate, rezistența la compresiune a peletelor scade odată cu creșterea conținutului de MgO, care se datorează conținutului de MgO Pe măsură ce crește, porozitatea peletelor crește și, în același timp, MgO intră în faza de zgură pentru a crește punctul de topire al mineralelor gangue, care are un anumit efect de împiedicare asupra formării fazei lichide. Rezultatele testului arată că atunci când alcalinitatea este peste 0.2, rezistența la compresiune a peletelor de specularită cu alcalinitate diferită și conținut de MgO poate atinge mai mult de 2500 N / bucată.
Pe măsură ce cantitatea de flux crește, porii lăsați de descompunerea fluxului în timpul prăjirii de preîncălzire cresc, de asemenea. Adăugarea de flux nu afectează doar compoziția chimică și compoziția minerală a peletelor, ci afectează și structura și porozitatea peletelor. Acest lucru va afecta rezistența la compresiune și proprietățile metalurgice ale peletelor într-o anumită măsură.
Efectul alcalinității și al conținutului de MgO asupra gradului de reducere. Gradul de reducere (RI) este un indicator important pentru evaluarea tendinței și dificultății eliminării oxigenului din minereul de fier în condițiile de temperatură și atmosferă din zona de reducere a furnalului. Factorii care afectează gradul de reducere a minereului de fier includ dimensiunea particulelor, porozitatea, compoziția și structura mineralelor și compoziția minerală gangue.
Gradul de reducere a peletelor acide cu alcalinitate naturală și conținut natural de MgO este scăzut, doar 62.22%. Odată cu creșterea conținutului de MgO, gradul de reducere crește. Când conținutul de MgO este de 3.0%, gradul de reducere a peletelor poate ajunge la 68%; Când conținutul de MgO crește alcalinitatea, gradul de reducere a peletelor de specularită este mult îmbunătățit. Când alcalinitatea crește la 1.2, gradul de reducere a peletelor crește la 72.82%. Acest lucru se datorează faptului că adăugarea de calcar crește porozitatea peletelor și, în același timp, CaO reacționează cu Fe2O3 pentru a forma ferită de calciu ușor redusă.
Când alcalinitatea și MgO acționează împreună, sub aceeași alcalinitate, gradul de reducere a peletelor de mirită crește odată cu creșterea conținutului de MgO; sub același conținut de MgO, gradul de reducere crește odată cu creșterea alcalinității.
Când alcalinitatea atinge 1.2 și conținutul de MgO crește la 3.0%, gradul de reducere a peletelor este de până la 76.94%. Acest lucru se datorează faptului că magnezita crește, de asemenea, porozitatea peletelor în timpul preîncălzirii și prăjirii peletelor, iar MgO poate crește punctul de topire a fazei de zgură și a corpului plutitor, astfel încât să nu se topească ușor în timpul procesului de reducere, iar porii peletelor nu se topesc. Materialul este umplut pentru a menține o porozitate ridicată, care favorizează difuzia gazelor.
Efectul alcalinității și al conținutului de MgO asupra reducerii expansiunii.
Sub conținutul natural de MgO, rata de expansiune de reducere a peletelor de specularită crește mai întâi și apoi scade, iar alcalinitatea atinge valoarea maximă între 0.4 și 0.6, iar valoarea maximă este de până la 32%.
Acest lucru se datorează faptului că o mică parte din CaO adăugată la pelete reacționează cu Fe2O3 pentru a produce ferită de calciu și cea mai mare parte a acesteia intră în faza de zgură. Când nu este redusă, faza de zgură este dominată de sistemul binar CaO-SiO2. Când alcalinitatea este cuprinsă între 0.4 și 0.6, adică conținutul de SiO2 în faza de zgură este între 62.5% și 70%, care este intervalul compoziției punctului eutectic binar al metasilicatului de calciu (CaOSiO2) și SiO2, și scăzut temperatura punctului eutectic este de 1436 ℃, dar în condiții de reducere, această fază de zgură devine un sistem ternar de zgură CaO-SiO2-FeO datorită adăugării de FeO. În acest sistem de zgură, raportul CaO și SiO2 rămâne neschimbat. Punctul de topire al fazei de zgură crește brusc odată cu creșterea conținutului de FeO. În sistemul pur de zgură ternară, poate fi de până la 1093 ℃, iar faza de zgură cu punct de topire scăzut va agrava doar reducerea și expansiunea peletelor.
Sub alcalinitate naturală, viteza de expansiune de reducere a peletelor scade ușor odată cu creșterea conținutului de MgO, dar nu este evident. Acest lucru se datorează alcalinității naturale și fazei naturale de zgură de pelete MgO cu un punct de topire de 1700 ℃ când conținutul de SiO2 este de 90%. Odată cu adăugarea de MgO, faza de zgură este dominată de sistemul binar MgO-SiO2, dar temperatura sa eutectică la temperatură scăzută are și o temperatură eutectică scăzută. 1543 ° C. Când alcalinitatea și MgO funcționează împreună, efectul alcalinității asupra vitezei de reducere a expansiunii peletelor este practic același cu conținutul natural de MgO sub același conținut de MgO. Când se adaugă MgO, punctul de topire al fazei de zgură este crescut prin topirea MgO în faza de zgură. În același timp, punctul de topire al fazei de zgură este, de asemenea, crescut de MgO în faza de zgură.
Prin urmare, sub aceeași alcalinitate, creșterea conținutului de MgO poate reduce expansiunea reducerii.
Extinderea volumului hematitei în peletele oxidate este redusă la magnetit și floatit. Această expansiune este cauzată în principal de schimbarea structurii cristaline atunci când hematitul este redus la magnetit. Rata de expansiune de reducere a peletelor este legată de compoziția ganguei și capacitatea fazei de zgură de a rezista la stresul generat de reducerea particulelor de hematit.
Faza de zgură cu un punct de topire ridicat nu este ușor de topit în timpul procesului de reducere, iar menținerea unei rezistențe ridicate poate limita efectiv rata de expansiune a reducerii peletelor, în timp ce faza de zgură cu punct de topire scăzut va agrava expansiunea de reducere a peletelor.
Rata de expansiune de reducere a peletelor sub 20% aparține intervalului normal de expansiune, iar alcalinitatea peletelor de specularită trebuie controlată în intervalul mai mic de 0.2 sau mai mare sau egal cu 1.0.
Cu toate acestea, în producția industrială generală, rata de expansiune de reducere a peletelor trebuie controlată sub 15%. Pentru peletele de specularită cu alcalinitate naturală conținând 3.0% ~ 3.1% SiO2, rata de expansiune de reducere este mai mică de 15%, iar gradul de reducere este de numai 62.2%. La îmbunătățirea gradului de reducere prin creșterea alcalinității, este necesar să se reducă alcalinitatea Numai când gradul de creștere la 1.0 și conținutul de MgO la 3.0%, sau alcalinitatea la 1.2 și conținutul de MgO ≥1.0%, poate crește expansiunea reducerii rata este mai mică de 15%.
Efectul alcalinității și al conținutului de MgO asupra pulverizării cu reducere a temperaturii scăzute. Pulverizarea cu reducere a temperaturii scăzute (RDI) reflectă tendința peletelor de a produce pulbere atunci când acestea sunt reduse în partea superioară a furnalului sau a cuptorului cu arbore de reducere directă la o temperatură cuprinsă între 400 ° C și 600 ° C. Principalul motiv pentru reducerea temperaturii scăzute și pulverizarea este expansiunea volumului și distorsiunea rețelei cauzate de conversia structurii cristaline atunci când hematitul este redus la magnetit.
Există trei metode principale de lipire formate atunci când peletele sunt preîncălzite și prăjite:
Recristalizarea oxidului de fier, lipirea silicatului și lipirea feritei.
Dintre acestea, legătura de recristalizare a hematitului este cea mai comună și mai puternică, dar hematita este extrem de instabilă în condiții de reducere, în timp ce faza de legare a silicatului poate fi menținută atunci când hematita este redusă la magnetit. Schimbare.
Prin urmare, este posibil să se mărească această distribuție uniformă și să se mențină o fază de legare stabilă în condiții de reducere a temperaturii scăzute prin adăugarea unui flux, astfel încât să se reducă reducerea temperaturii scăzute și pulverizarea peletelor de mirită.
Peletele cu alcalinitate naturală și conținut natural de MgO sunt în principal consolidare prin difuzie în fază solidă a hematitului, cu o fază de legare mai mică a silicatului. Prin urmare, se produce mai multă pulbere în timpul reducerii temperaturii scăzute, iar valoarea sa RDI-3.15mm este de până la 12.75. %. Sub conținutul natural de MgO, alcalinitatea a crescut la 0.2, iar rata de pulverizare a temperaturii scăzute a peletei, valoarea RDI-3.15 mm a scăzut rapid la 0.52%; alcalinitatea a continuat să crească, iar valoarea RDI-3.15 mm a fost practic menținută la aproximativ 0.5%. Acest lucru se datorează faptului că adăugarea de CaO permite peletelor să formeze faze lichide mai silicate care sunt stabile în timpul reducerii temperaturii scăzute în timpul preîncălzirii și calcinării, atingând astfel scopul de a reduce reducerea temperaturii scăzute și pulverizarea peletelor.
Sub alcalinitate naturală, creșterea conținutului de MgO, reducerea temperaturii scăzute și rata de pulverizare a peletelor, RDI-3.15mm, toate scad sub 3.0%. Când alcalinitatea și MgO funcționează împreună, valoarea RDI-3.15 mm a peletelor în pulverizarea cu reducere a temperaturii scăzute este scăzută. RDI-3.15mm scade odată cu creșterea alcalinității și crește ușor odată cu creșterea conținutului de MgO. Acest lucru se datorează MgO. Poate împiedica formarea silicatului în fază lichidă.
Efectul alcalinității și al conținutului de MgO asupra caracteristicilor de reflux. Caracteristicile de topire a peletelor pot reflecta formarea peletilor în zona de topire moale din partea inferioară a furnalului și performanța lor în zona de topire moale. Caracteristicile de reflux ale încărcăturii au un impact mai mare asupra funcționării furnalului. Temperatura de înmuiere a peletelor este scăzută și intervalul de reflux este larg, iar permeabilitatea la aer a zonei de reflux în partea inferioară a furnalului va deveni slabă, ceea ce nu este favorabil convecției gazului reducător și a încărcăturii și afectează grav procesul de reducere.
Peleții acizi cu alcalinitate naturală și conținut natural de MgO încep să se înmoaie la 1009 ° C, iar temperatura de scădere este de 1272 ° C. Cu conținut natural de MgO, alcalinitatea crește la 1.2, temperatura de înmuiere a peletelor crește la 1034 ° C, intervalul de înmuiere și intervalul de înmuiere sunt restrânse, iar temperatura de picurare crește și la 1299 ° C. Când alcalinitatea este 1.2, creșterea conținutului de MgO poate crește temperatura de pornire și temperatura de picurare. Când conținutul de MgO este de 1.0%, temperatura de înmuiere a peletelor va crește la 1072 ℃, temperatura de picurare va ajunge la 1319 ℃, conținutul de MgO va continua să crească, iar temperatura de înmuiere a peletelor nu va crește Cu o creștere suplimentară, temperatura de picurare a crescut .
Caracteristicile de reflux ale peletelor sunt afectate în principal de fazele lichide cu topire redusă, cum ar fi fusterita și zgura produse în timpul reducerii. Caracteristicile slabe de reflux la temperaturi ridicate ale peletelor acide se datorează în principal punctului de topire scăzut al fazei de zgură olivină bogată în FeO în timpul procesului de reducere, iar adăugarea de MgO poate crește punctul de topire al fazei de zgură. Formarea unei soluții solide cu un punct de topire ridicat va juca, de asemenea, un rol în îmbunătățirea caracteristicilor de reflux la temperaturi ridicate ale peletelor.
Vă rugăm să păstrați sursa și adresa acestui articol pentru reimprimare: „Alcali” și „Magneziu” pentru a îmbunătăți performanța peletelor
Minghe Compania de turnare sub presiune sunt dedicate fabricării și furnizează piese de turnare de calitate și de înaltă performanță (gama de piese turnate sub presiune din metal include în principal Turnare sub presiune cu perete subțire,Hot Cast casting sub presiune,Turnare sub presiune în cameră rece), Serviciu rotund (Serviciu de turnare sub presiune,Prelucrare Cnc,Fabricarea mucegaiului, Tratament de suprafață). Orice cerință personalizată de turnare sub presiune din aluminiu, magneziu sau turnare sub presiune din Zamak / zinc și alte cerințe de turnare sunt binevenite să ne contacteze.
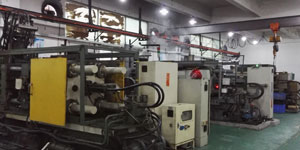
Sub controlul ISO9001 și TS 16949, toate procesele sunt efectuate prin sute de mașini avansate de turnare sub presiune, mașini cu 5 axe și alte facilități, variind de la blastere la mașini de spălat Ultra Sonic. Minghe nu numai că are echipamente avansate, dar are o echipă de ingineri cu experiență, operatori și inspectori pentru a face realitatea designul clientului.
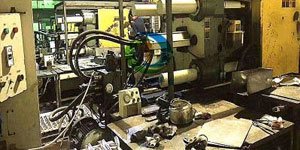
Producător contract de piese turnate sub presiune. Capacitățile includ piese de turnare sub presiune din aluminiu cu cameră rece de la 0.15 lbs. la 6 lbs., schimbare rapidă configurată și prelucrare. Serviciile cu valoare adăugată includ lustruire, vibrare, debavurare, sablare, vopsire, placare, acoperire, asamblare și scule. Materialele lucrate includ aliaje precum 360, 380, 383 și 413.
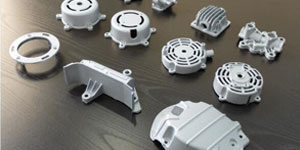
Asistență la proiectarea turnării sub presiune din zinc / servicii de inginerie simultană. Producător personalizat de piese turnate sub presiune din zinc. Pot fi fabricate piese turnate în miniatură, piese turnate sub presiune înaltă, piese turnate multi-glisante, piese turnate convenționale, piese turnate sub formă de unități și piese turnate independente și piese turnate sigilate în cavitate. Piesele turnate pot fi fabricate în lungimi și lățimi de până la toleranță de +/- 24 in.
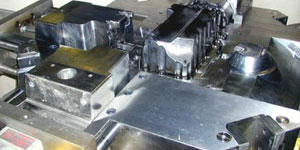
Producător certificat ISO 9001: 2015 de magneziu turnat sub presiune, capabilitățile includ turnare sub presiune cu magneziu de înaltă presiune de până la 200 tone cameră fierbinte și 3000 tone cameră rece, proiectare scule, lustruire, turnare, prelucrare, vopsire cu pulbere și lichide, QA complet cu capacități CMM , asamblare, ambalare și livrare.
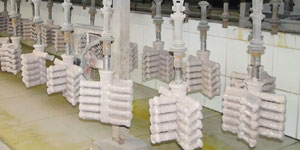
Certificat ITAF16949. Serviciul de turnare suplimentar include investiții de turnătorie,turnare cu nisip,Turnarea gravitației, Pierdere spumă turnare,Turnare centrifugă,Turnarea în vid,Turnare permanentă a matriței, .Capacitățile includ EDI, asistență tehnică, modelare solidă și procesare secundară.
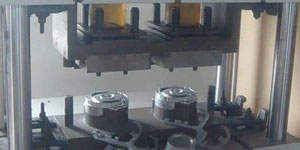
Industrii de turnare Părți Studii de caz pentru: Mașini, biciclete, aeronave, instrumente muzicale, ambarcațiuni, dispozitive optice, senzori, modele, dispozitive electronice, carcase, ceasuri, mașini, motoare, mobilier, bijuterii, jiguri, telecomunicații, iluminat, dispozitive medicale, dispozitive fotografice, Roboți, sculpturi, echipamente de sunet, echipamente sportive, scule, jucării și multe altele.
Ce vă putem ajuta să faceți în continuare?
∇ Accesați pagina principală pentru China turnare sub presiune
→Piese de turnare-Aflați ce am făcut.
→ Ralated Tips About Servicii de turnare sub presiune
By Producător de turnare sub presiune Minghe | Categorii: Articole utile |Material Etichete: Turnare din aluminiu, Turnarea zincului, Turnarea cu magneziu, Turnare cu titan, Turnare din oțel inoxidabil, Turnare din alamă,Turnarea bronzului,Distribuirea videoclipului,Istoricul companiei,Turnare din aluminiu | Comentarii dezactivate