Controlul calității la stingerea cu căldură uzată după forjare
Țările din întreaga lume susțin cu fermitate politica de reducere a emisiilor și a consumului: mulți erudiți și companii interne au luat măsuri din diferite aspecte, iar stingerea căldurii reziduale după forjare este una dintre măsurile importante.
Stingerea căldurii reziduale după forjare este un tratament termic termomecanic la temperaturi ridicate în tratamentul termic termomecanic. Datele [1, 2, 3] au descrieri specifice. Până în prezent, mulți producători autohtoni au folosit stingerea căldurii reziduale după forjare, iar câțiva producători au lansat → demontat → remontat sau montat → demontat → continuă să demonteze din cauza măsurilor slabe de control al calității.
În comparație cu tratamentul termic convențional, datorită încălzirii la temperatură ridicată și deformării turnării, mărimea granulei de unghi mic de martensită a oțelului crește, densitatea dislocării crește, hidrogenul original scapă parțial, fisurile originale sunt vindecate și reduse, iar carburile sunt dispersate și precipitate. Duritatea de stingere a pieselor din oțel s-a îmbunătățit semnificativ (în general îmbunătățită cu aproximativ 10%). În timpul călirii, piesele din oțel au o rezistență ridicată la temperare (temperatura de temperare este îmbunătățită în comparație cu cele convenționale, în general 20 ℃ -30 ℃).
- 1. Când am mers la stația de tratare termică din diverse motive, mulți angajați tehnici și tehnici au sugerat că materiile prime și alte aspecte sunt bune, cum să prezicem fenomenul de stingere a fracturii după ce ne-am uitat unul la altul? Acesta este rezumatul celor trei efecte majore (aceste trei efecte majore au, de asemenea, o valoare de referință pentru fragilitatea hidrogenului și fractura de coroziune prin stres în procesul de tratare a suprafeței).
- 1.1 Efectul compoziției chimice: De exemplu: oțel carbon: aceeași dimensiune ф6, aceeași apă sărată de stingere: 35 oțel, 40 oțel, 45 oțel, 50 oțel, 55 oțel, 60 oțel, 65 oțel, rezultatul este că 45 oțel ~ 60 oțel este ușor de rupt. Deoarece cu cât este mai mare conținutul de carbon martensit, cu atât este mai mare stresul, iar conținutul maxim de carbon este de aproximativ 0.6%. Atunci când conținutul de carbon al oțelului este foarte ridicat, va fi mai mare de 0.6% și va fi generat reziduul A, ceea ce încetinește eliberarea selectivă a stresului de martensită și nu este ușor de fracturat. În general, oțelul aliat este cel mai vulnerabil la stingere și fisurare. De exemplu: 42CrM. Când dimensiunea este mare ф100, apa de stingere nu se va sparge. Acesta este efectul de dimensiune descris mai jos.
- 1.2 Efectul dimensiunii: De exemplu: 45 oțel: ф1, ф2, ф3 ...... ф10 rezultatele de stingere au constatat că ф6 este cel mai probabil să fie stins. Deoarece sub ф6, poate fi în general stins în martensită. Cu toate acestea, transformarea generală a lui into6 în martensită are cel mai mare stres, deci este cel mai ușor de rupt. Același motiv: stresul maxim maxim al oțelului aliat este indicele de întărire (întărirea este jumătate de martensită), care este de aproximativ 2/3 . Prin urmare, verificați mai întâi indicele de întărire a unui anumit oțel aliat și apoi priviți piesa de prelucrat. Care este dimensiunea cea mai periculoasă?
- 1.3 Efect de formă: schimbare bruscă a secțiunii transversale, unghi R prea mic, colțuri ascuțite proeminente, caneluri adânci pe margini, perforare și marcare a muchiilor ascuțite, găuri oarbe, deschideri de jos, deschideri ale portalului, distanțe necorespunzătoare ale găurilor și diferite dimensiuni ale diafragmei Etc., asimetria secțiunii transversale etc.
- 2. Selectarea temperaturii de pre-răcire: Toată lumea știe că boabele de structură de martensită stinse direct fără pre-răcire după forjare sunt mai mici. Poate îndeplini cerințele standard metalografice generale domestice actuale, iar performanța este, de asemenea, bună, dar pentru piesele mari și complexe, uleiul de stingere nu poate îndeplini cerințele, stingerea cu apă sau mediu de stingere apos va provoca cu ușurință fisuri. Este pentru stingerea uleiului, pentru a preveni poluarea și a economisi costurile, ar trebui să fie schimbat în mediu de stingere pe bază de apă cât mai mult posibil; 42CrM în ansamblul camionului Steyr pentru vehicule grele produs de o companie din Chongqing. Oţel; Forjate ale grinzii osiei frontale și ale arborelui de echilibrare, un anumit personal tehnic al companiei a schimbat unilateral pre-răcirea ≈800 ℃ la ≥850 ℃ stingere directă, ceea ce a cauzat aproximativ 80% din fisurile mari de stingere. Desigur, a fost analizată cauza fracturii, iar conținutul de B al materiei prime a ajuns la 0.0022% din raportul de inspecție al Grupului de construcții Chongqing și al Grupului Changan al Centrului de inspecție fizică și chimică din sud-vestul Ministerului Armelor. 0.0042%. Nota 1). Standardul militar național GJB2720-1996, standardul conținutului de bor al oțelului cu bor este de 0.0005 ~ 0.0035%; (2). Condițiile tehnice ale oțelului de structură portant aur GB3077-88 conținutul de bor standard al oțelului cu bor este de 0.0005 ~ 0.0035%. Segregarea benzii la nivelul I ... este, de asemenea, unul dintre motive. Problema segregării zonale severe a materiilor prime care ating nivelul I este un factor important pentru fisuri (segregarea mai grea determină o compoziție chimică inegală și tratamentul termic, distribuirea stresului de stingere, care este ușoară a provoca fisuri de stingere);
Utilizarea analizei spectrului de energie cu raze X: Limitele granulelor și matricea din structura metalografică pregătită a probei au fost analizate calitativ și semicantitativ cu un analizor de spectru de energie cu raze X Vantage. Rezultatele analizei sunt prezentate în Figura 1, Figura 2 și Tabelul 1.
Cu toate acestea, celălalt oțel pentru cuptor are un conținut ridicat de bor și o segregare mare. Concentrația PAG este ajustată prin scăderea temperaturii de pre-răcire, astfel încât nu au apărut fisuri.
Alegerea temperaturii de pre-răcire: În primul rând, conform celor trei efecte menționate mai sus, se determină partea cea mai vulnerabilă. Parametrii procesului ar trebui să fie reglați corespunzător. De exemplu:
- (1) „Deasupra grinzii osiei față” 42CrM. Pre-răcim ≈800 ℃ pentru a stinge PAG și este ușor de controlat HRC la 48-52.
- (2) O fabrică mare de arborele cotit pentru motociclete din Chongqing: adoptă metoda de așteptare și pre-răcire după forjare pentru a realiza pre-răcirea ≈770 ℃ pentru stingerea PAG și adoptă un mecanism de ridicare a centurii de plasă pentru a părăsi suprafața lichidului fără a fi rece și ușor temperat de sine. După golire, temperatura de pre-răcire de 45 oțel și 40Cr este similară, dar concentrația PAG este diferită.
- (3) O fabrică de arborele cotit din Chongqing: adoptă un dispozitiv care intră într-un cuptor cu temperatură constantă după forjare pentru a-l menține pre-răcit la ~ 770 ℃ și a stinge într-o soluție pe bază de apă ...
Alegerea mediului de stingere: bazat pe cele mai recente cercetări din întreaga lume, așa-numitul efect hard shell. Cerințe: Prima rată de răcire a rotației perlitei trebuie să fie rapidă pentru a forma un efect de coajă dură cu stres compresiv. Martensitul se întoarce încet, astfel încât fisurile să nu fie ușor să apară, iar o serie de rezultate ale cercetării, cum ar fi utilizarea răcirii prin pulverizare controlate de program pentru a controla viteza, sunt demne de popularizare și aplicare.
Fluidele de stingere PAG-ⅢA și PAG-ⅢB dezvoltate de noi se bazează pe necesitatea urgentă a unui nou tip de viteză de transformare a perlitei similară cu apa sărată și apa alcalină și viteza de transformare a martensitei similară cu uleiul, care înlocuiește cu adevărat stingerea apei și uleiul răcire. Lichid de stingere, iar capacitatea anti-rugină este menținută mai mult de 5 zile. Pentru a face schimbarea perlitei asemănătoare cu apa sărată și alcalină, pelicula de bule formată atunci când lucrarea de stingere intră în lichid trebuie ruptă rapid, astfel încât viteza de răcire să fie accelerată. De exemplu, la o concentrație de 3%, prima rată de răcire nu este la fel de bună ca apa salină și alcalină, adică trebuie adăugat unul sau mai mulți aditivi amestecați pentru a îndeplini cerințele de mai sus. De fapt, concentrația de PAG-ⅢA atinge prima viteză mai rapidă decât apa și alcoolul polivinilic, iar a doua viteză este mai lentă decât cea a altor producători sub aceeași concentrație de PAG ....... În carburarea și stingerea ochiurilor de plasă cuptoare cu curea: PAG-ⅢA a fost dezvoltat și aplicat în multe moduri ... În prezent, există mai mult de 20 de cuptoare cu curea din plasă utilizate în toată țara; în special carburarea cu cuptor cu plasă rezolvă problema punctelor moi, a durității insuficiente, a deformării mari ...…. Capacitatea anti-rugină este mai mare de 5 zile, iar consumul de PAG este redus cu 20%.
Există 6 aplicații PAG-ⅢA în Chongqing. Deoarece unii producători folosesc acest model, unele produse speciale rezolvă probleme greu de rezolvat cu alte suporturi, iar producția crește. Din motive de confidențialitate, nu le vom introduce unul câte unul. Este utilizat pe scară largă în frecvență înaltă; arborele osiei auto de frânare cu frecvență medie.
Concentrația, temperatura și agitarea lichidului de stingere
Unitatea pe care o deservim: concentrația PAG a lichidului de stingere, în funcție de gradul de oțel, dimensiunea pieselor și dimensiunile externe în conformitate cu teoria și experiența pentru a regla concentrația sa ....
Temperatura lichidului este controlată la 30-50 ℃ și o piscină mare de circulație în afara centralei este utilizată pentru schimbul de căldură circulant. Agitarea și circulația sunt un întreg integral.
Controlul durității după stingere
Duritatea după stingere este un indicator foarte important pentru a preveni crăparea: mai ales atunci când este utilizat fluid de stingere pe bază de apă, cu atât duritatea, crăpăturile și creșterea deformării sunt mai mari. Luați 42CrMo. De exemplu, grinda axului frontal trebuie controlată la HRC48 ~ 52.
Temperarea trebuie făcută imediat după stingere
Interval de stingere și temperare: ≤ 30 de minute (Produsele militare și civile ale Chongqing Construction Group necesită ca stingerea lichidului pe bază de apă la intervalul de revenire a apei să depășească 30 de minute, apoi va fi casată) Producția de piese mici poate fi utilizată în temperare continuă linii de producție.
Structura și proprietățile metalografice după forjare și stingere
Forjarea stingerii căldurii, dacă este necesară pre-răcirea, boabele sunt în general mai mari. Date [1, 2, 3] datorate testului tezei de absolvire a elevilor din acel an, exemplarele mici utilizate în general nu sunt pre-răcite și stinse direct, oferind o bază teoretică foarte importantă.
Odată cu inovarea și dezvoltarea oamenilor: tehnologia de producție actuală adoptă în prezent pre-răcirea și stingerea, iar mărimea bobului este în general de 2-3, dar performanța este excelentă. Luați ca exemplu grinda axului față menționată mai sus: bobul este mic, iar datele standard ale ciclului de oboseală sunt că se permite ruperea după 900,000 de ori, iar ciclul de oboseală de pre-răcire și stingere după forjare este adoptat pentru a ajunge la 1.3 de milioane de ori fără să se rupă.
De ce forjarea, pre-răcirea și stingerea cerealelor grosiere și performanțele bune de testare? Motivul principal este că limitele granulelor cu unghi mic cresc și densitatea dislocării crește, care sunt invizibile la un microscop metalurgic general. Prin urmare, multe unități de forjare și stingere trebuie să „învețe probleme” cu unitatea de inspecție anterioară. Din acest motiv, este o problemă urgentă ca personalul tehnic și tehnic care se ocupă în prezent cu standarde metalografice să formuleze rapid standarde metalografice de forjare și stingere ...
Concluzie
- Aplicarea metodei de pre-răcire pentru stingerea căldurii reziduale după forjare Alegerea temperaturii de pre-răcire se bazează pe structura și performanța cerute, atâta timp cât îndeplinește cerințele, cu cât este mai mică cu atât mai bine.
- După forjare, mediul de stingere pentru stingerea prin căldură reziduală este selectat pe cât posibil pentru a utiliza prima rată de răcire (rata de transformare a perlitei) pentru a forma un efect de coajă tare. Al doilea lichid de stingere cu o rată de răcire lentă (rată lentă de transformare a martensitei).
- Atunci când materiile prime și alte aspecte sunt bune, dacă planificarea prealabilă va produce fisuri ar trebui să se înțeleagă cele trei efecte majore.
- Compoziția chimică și segregarea materiilor prime sunt deosebit de predispuse la fisuri. Se recomandă ca atunci când se schimbă numărul cuptorului, să se efectueze un lot mic de producție de încercare și o inspecție de magnetizare 100%. Profitați pentru a găsi măsuri pentru a preveni apariția unui număr mare de resturi.
Vă rugăm să păstrați sursa și adresa acestui articol pentru reimprimare: Controlul calității la stingerea cu căldură uzată după forjare
Minghe Compania de turnare sub presiune sunt dedicate fabricării și furnizează piese de turnare de calitate și de înaltă performanță (gama de piese turnate sub presiune din metal include în principal Turnare sub presiune cu perete subțire,Hot Cast casting sub presiune,Turnare sub presiune în cameră rece), Serviciu rotund (Serviciu de turnare sub presiune,Prelucrare Cnc,Fabricarea mucegaiului, Tratament de suprafață). Orice cerință personalizată de turnare sub presiune din aluminiu, magneziu sau turnare sub presiune din Zamak / zinc și alte cerințe de turnare sunt binevenite să ne contacteze.
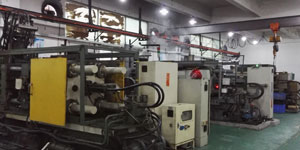
Sub controlul ISO9001 și TS 16949, toate procesele sunt efectuate prin sute de mașini avansate de turnare sub presiune, mașini cu 5 axe și alte facilități, variind de la blastere la mașini de spălat Ultra Sonic. Minghe nu numai că are echipamente avansate, dar are o echipă de ingineri cu experiență, operatori și inspectori pentru a face realitatea designul clientului.
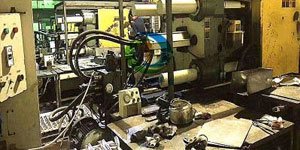
Producător contract de piese turnate sub presiune. Capacitățile includ piese de turnare sub presiune din aluminiu cu cameră rece de la 0.15 lbs. la 6 lbs., schimbare rapidă configurată și prelucrare. Serviciile cu valoare adăugată includ lustruire, vibrare, debavurare, sablare, vopsire, placare, acoperire, asamblare și scule. Materialele lucrate includ aliaje precum 360, 380, 383 și 413.
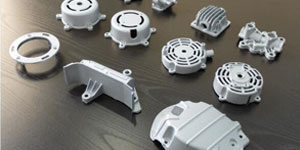
Asistență la proiectarea turnării sub presiune din zinc / servicii de inginerie simultană. Producător personalizat de piese turnate sub presiune din zinc. Pot fi fabricate piese turnate în miniatură, piese turnate sub presiune înaltă, piese turnate multi-glisante, piese turnate convenționale, piese turnate sub formă de unități și piese turnate independente și piese turnate sigilate în cavitate. Piesele turnate pot fi fabricate în lungimi și lățimi de până la toleranță de +/- 24 in.
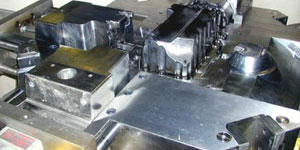
Producător certificat ISO 9001: 2015 de magneziu turnat sub presiune, capabilitățile includ turnare sub presiune cu magneziu de înaltă presiune de până la 200 tone cameră fierbinte și 3000 tone cameră rece, proiectare scule, lustruire, turnare, prelucrare, vopsire cu pulbere și lichide, QA complet cu capacități CMM , asamblare, ambalare și livrare.
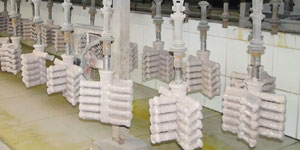
Certificat ITAF16949. Serviciul de turnare suplimentar include investiții de turnătorie,turnare cu nisip,Turnarea gravitației, Pierdere spumă turnare,Turnare centrifugă,Turnarea în vid,Turnare permanentă a matriței, .Capacitățile includ EDI, asistență tehnică, modelare solidă și procesare secundară.
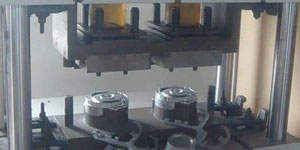
Industrii de turnare Părți Studii de caz pentru: Mașini, biciclete, aeronave, instrumente muzicale, ambarcațiuni, dispozitive optice, senzori, modele, dispozitive electronice, carcase, ceasuri, mașini, motoare, mobilier, bijuterii, jiguri, telecomunicații, iluminat, dispozitive medicale, dispozitive fotografice, Roboți, sculpturi, echipamente de sunet, echipamente sportive, scule, jucării și multe altele.
Ce vă putem ajuta să faceți în continuare?
∇ Accesați pagina principală pentru China turnare sub presiune
→Piese de turnare-Aflați ce am făcut.
→ Ralated Tips About Servicii de turnare sub presiune
By Producător de turnare sub presiune Minghe | Categorii: Articole utile |Material Etichete: Turnare din aluminiu, Turnarea zincului, Turnarea cu magneziu, Turnare cu titan, Turnare din oțel inoxidabil, Turnare din alamă,Turnarea bronzului,Distribuirea videoclipului,Istoricul companiei,Turnare din aluminiu | Comentarii dezactivate