Precauții pentru turnarea cu nisip a sticlei de apă
Care sunt factorii care afectează „îmbătrânirea” sticlei de apă? Cum se elimină „îmbătrânirea” sticlei de apă?
Paharul de apă proaspăt preparat este o adevărată soluție. Cu toate acestea, în timpul procesului de stocare, acidul silicic din sticla de apă va suferi polimerizare prin condensare, care se va policondensa treptat din soluția adevărată într-o soluție de acid silicic macromolecular și va deveni în cele din urmă un gel de acid silicic. Prin urmare, sticla cu apă este de fapt un amestec eterogen compus din acid polisilicic cu diferite grade de polimerizare, care este ușor afectat de modulul, concentrația, temperatura, conținutul de electroliți și timpul de depozitare.
În timpul depozitării, moleculele de sticlă de apă suferă polimerizare prin condensare pentru a forma un gel, iar rezistența sa de legătură scade treptat odată cu extinderea timpului de depozitare. Acest fenomen se numește „îmbătrânire” a sticlei de apă.
Fenomenul „îmbătrânire” poate fi explicat prin următoarele două seturi de date de testare: sticlă de apă cu modul ridicat (M = 2.89, ρ = 1.44g / cm3) după 20, 60, 120, 180, 240 zile de depozitare, CO2 întărit sticla cu apă este suflată Rezistența la tracțiune uscată a nisipului scade corespunzător cu 9.9%, 14%, 23.5%, 36.8% și 40%; silicatul de sodiu cu modul redus (M = 2.44, ρ = 1.41 g / cm3) este depozitat timp de 7, 30, 60 și 90 de zile după ce a fost uscat. Rezistența la tracțiune a scăzut cu 4.5%, 5%, 7.3% și respectiv 11%.
Timpul de păstrare al sticlei cu apă are un efect redus asupra rezistenței inițiale a nisipului auto-întăritor al sticlei de apă întărită cu ester, dar are un efect semnificativ asupra rezistenței ulterioare. Conform măsurătorilor, acesta este redus cu aproximativ 60% pentru sticla de apă cu modul ridicat și 15-20% pentru sticla de apă cu modul redus. . Rezistența reziduală scade, de asemenea, odată cu prelungirea timpului de depozitare.
În timpul depozitării sticlei de apă, policondensarea și depolimerizarea acidului polisilicic continuă în același timp, greutatea moleculară este disproporționată și, în cele din urmă, se formează un sistem multi-dispersat în care coexistă acidul monoortosilicic și particulele coloidale. Adică, în timpul procesului de îmbătrânire a sticlei de apă, gradul de polimerizare al acidului silicic este disproporționat, iar conținutul de acid monoortosilicic și acid polisilicic ridicat crește odată cu prelungirea timpului de depozitare. Ca rezultat al reacției de polimerizare prin condensare și de depolimerizare a sticlei de apă în timpul depozitării, rezistența la lipire este redusă, adică are loc fenomenul de „îmbătrânire”.
Principalii factori care afectează „îmbătrânirea” sticlei de apă sunt: timpul de depozitare, modulul și concentrația sticlei de apă. Cu cât timpul de depozitare este mai mare, cu atât modulul este mai mare și concentrația este mai mare, cu atât „îmbătrânirea” este mai gravă.
Paharul cu apă existent de mult poate fi modificat într-o varietate de moduri pentru a elimina „îmbătrânirea” și a restabili paharul cu apă la performanța paharului cu apă dulce:
1. Modificare fizică
Îmbătrânirea sticlei de apă este un proces spontan care eliberează încet energie. Modificarea fizică a sticlei de apă „îmbătrânită” este de a utiliza câmp magnetic, ultrasunete, frecvență înaltă sau încălzire pentru a furniza energie sistemului de sticlă cu apă și pentru a promova polimerizarea ridicată a lipiciului polisilicat. Particulele re-depolimerizează și promovează omogenizarea greutății moleculare a acidului polisilicic, eliminând astfel fenomenul de îmbătrânire, care este mecanismul modificării fizice. De exemplu, după tratamentul cu un câmp magnetic, puterea nisipului de silicat de sodiu crește cu 20-30%, cantitatea de silicat de sodiu adăugată este redusă cu 30-40%, CO2 este economisit, colapsabilitatea este îmbunătățită și există Beneficii economice.
Dezavantajul modificării fizice este că nu este durabil, iar rezistența la lipire va scădea atunci când este depozitată după tratament, deci este adecvată pentru utilizare cât mai curând posibil după tratament în turnătorie. În special pentru sticla cu apă cu M> 2.6, concentrația moleculelor de acid silicic este mare și, după modificări fizice și depolimerizare, se va policondensa relativ rapid. Cel mai bine este să-l utilizați imediat după tratament.
2. Modificare chimică
Modificarea chimică este de a adăuga o cantitate mică de compuși în sticla de apă, acești compuși conțin toți carboxil, amidă, carbonil, hidroxil, eter, amino și alte grupări polare, care sunt adsorbiți pe molecule de acid silicic sau particule coloidale prin legături de hidrogen sau statice. electricitate. Suprafața, schimbă-i energia potențială de suprafață și capacitatea de solvație, îmbunătățește stabilitatea acidului polisilicic, prevenind astfel „îmbătrânirea” să se desfășoare.
De exemplu, adăugarea de poliacrilamidă, amidon modificat, polifosfat etc. în sticla de apă poate obține rezultate mai bune.
Incorporarea materiei organice în paharul de apă obișnuit sau chiar în paharul de apă modificat poate juca o varietate de funcții, cum ar fi: schimbarea proprietăților de curgere vâscoasă a paharului de apă; îmbunătățirea performanței de modelare a amestecurilor de sticlă cu apă; creșterea rezistenței de lipire pentru a face paharul de apă adăugat absolut Cantitatea este redusă; plasticitatea gelului de acid silicic este îmbunătățită; rezistența reziduală este redusă, astfel încât nisipul de apă din sticlă este mai potrivit pentru fontă și aliaje neferoase.
3. Modificarea fizico-chimică
Modificarea fizică este potrivită pentru sticla de apă „îmbătrânită” și poate fi utilizată imediat după modificare. Modificarea chimică este potrivită pentru procesarea sticlei de apă dulce, iar sticla de apă modificată poate fi păstrată mult timp. Combinația dintre modificarea fizică și modificarea chimică poate face ca sticla de apă să aibă un efect de modificare durabilă. De exemplu, adăugarea poliacrilamidei în autoclavă pentru a modifica sticla de apă „îmbătrânită” are un efect bun. Printre acestea se utilizează presiunea și presiunea autoclavei. Agitarea este o modificare fizică, iar adăugarea poliacrilamidei este o modificare chimică.
Cum să preveniți suflarea cu CO2 a silicatului de sodiu întărit cu mucegai de nisip (miez) de cretă?
După ce nisipul silicat de sodiu sodic este suflat cu CO2 întărit și lăsat pentru o perioadă de timp, uneori o substanță precum înghețul hoar va apărea pe suprafața matriței inferioare (miez), care va reduce serios rezistența suprafeței locului și va produce cu ușurință nisip defecte de spălare în timpul turnării. Conform analizei, componenta principală a acestei substanțe albe este NaHCO3, care poate fi cauzată de umiditatea excesivă sau CO2 din nisipul silicatului de sodiu. Reacția este următoarea:
- Na2CO3 + H2O → NaHCO3 + NaOH
- Na2O+2CO2+H2O→2NaHCO3
- NaHCO3 migrează ușor spre exterior cu umezeală, provocând îngheț ca pulberea pe suprafața matriței și a miezului.
Soluția este următoarea:
- Controlați conținutul de umiditate al nisipului de silicat de sodiu să nu fie prea mare (mai ales în sezonul ploios și iarna).
- Timpul de suflare a CO2 nu ar trebui să fie prea lung.
- Matrița și miezul întărit nu trebuie așezate mult timp și trebuie turnate și turnate în timp.
- Adăugarea aproximativ 1% (fracție de masă) a siropului cu o densitate de 1.3 g / cm3 la nisipul cu silicat de sodiu poate preveni în mod eficient suprafața de pulbere.
Cum se îmbunătățește rezistența la absorbția umezelii a matriței de nisip din sticlă de apă (miez)
Miezul de nisip din sticlă de apă sodă întărit prin CO2 sau prin metode de încălzire este asamblat în matrița de lut umed. Dacă nu este turnat la timp, rezistența miezului de nisip va scădea brusc, nu numai că se poate strecura, chiar se poate prăbuși; este depozitat într-un mediu umed. Rezistența miezului de nisip este, de asemenea, redusă semnificativ. Tabelul 1 prezintă valorile de rezistență ale miezurilor de nisip din sticlă cu apă sodică întărită cu CO2 atunci când sunt plasate într-un mediu cu o umiditate relativă de 97% timp de 24 de ore. Motivul pierderii de rezistență atunci când este depozitat într-un mediu umed se datorează rehidratării sticlei cu apă de sodiu. Na + și OH- din matricea liantului silicatului de sodiu absorb umezeala și erodează matricea, rupând în cele din urmă legătura siliciu-oxigen Si-O-Si, rezultând o scădere semnificativă a rezistenței de legătură a nisipului cu silicat de sodiu.
Măsurile pentru rezolvarea acestei probleme sunt:
- 1. Paharul cu apă de litiu este adăugat la paharul cu apă de sodiu sau Li2CO3, CaCO3, ZnCO3 și alți aditivi anorganici se adaugă la paharul cu apă de sodiu, deoarece se pot forma carbonați și silicați relativ insolubili, iar ionii de sodiu liberi pot fi reduși. rezistența la absorbție a liantului de sticlă cu apă sodică poate fi îmbunătățită.
- 2. Adăugați o cantitate mică de material organic sau materie organică cu funcție tensioactivă la paharul cu apă de sodiu. Când liantul este întărit, ionii hidrofili Na + și OH- din gelul de sticlă cu apă de sodiu pot fi înlocuiți cu grupări organice hidrofobe sau Combinate între ele, baza organică hidrofobă expusă îmbunătățește absorbția umidității.
- 3. Îmbunătățiți modulul sticlei de apă, deoarece rezistența la umiditate a sticlei de apă cu modul înalt este mai puternică decât cea a sticlei de apă cu modul scăzut.
- 4. Adăugați hidrolizat de amidon pe nisipul cu silicat de sodiu. O metodă mai bună este utilizarea hidrolizatului de amidon pentru modificarea sticlei de apă sodică.
4 Care sunt caracteristicile procesului compozit cu nisip sticlă-rășină fenolică alcalină cu suflare de CO2?
În ultimii ani, pentru a îmbunătăți calitatea pieselor turnate din oțel, unele întreprinderi mici și mijlocii trebuie să adopte urgent procesul de nisip cu rășină. Cu toate acestea, din cauza capacității economice limitate, aceștia nu pot achiziționa echipamente de regenerare a nisipului cu rășină, iar nisipul vechi nu poate fi reciclat și reutilizat, rezultând costuri ridicate de producție. Pentru a găsi o modalitate eficientă de a îmbunătăți calitatea pieselor turnate fără a crește prea mult costul, caracteristicile procesului de nisip de silicat de sodiu întărit cu suflare de CO2 și nisip de rășină fenolică alcalină întărită cu suflare de CO2 pot fi combinate și de silicat de sodiu întărit cu suflare de CO2 - alcalin se poate folosi rășină fenolică. Procesul de amestecare a nisipului cu rășină folosește nisip de rășină fenolică alcalină ca nisip de suprafață și nisip de sticlă de apă ca nisip din spate, în timp ce suflă CO2 pentru întărire.
Rășina fenolică utilizată în nisipul cu rășină fenolică alcalină CO2 este produsă prin policondensarea fenolului și formaldehidei sub acțiunea unui catalizator puternic alcalin și adăugarea unui agent de cuplare. Valoarea sa PH este ≥13, iar vâscozitatea sa este ≤500mPa • s. Cantitatea de rășină fenolică adăugată la nisip este de 3% până la 4% (fracție de masă). Când debitul de CO2 este de 0.8 ~ 1.0m3 / h, cel mai bun timp de suflare este de 30 ~ 60s; dacă timpul de suflare este prea scurt, rezistența la întărire a miezului de nisip va fi redusă; dacă timpul de suflare este prea lung, rezistența miezului de nisip nu va crește și este un gaz irosit.
CO2 - Nisipul cu rășină fenolică alcalină nu conține elemente dăunătoare precum N, P, S etc., astfel încât sunt eliminate defectele de turnare precum porii, microfisurile de suprafață etc. cauzate de aceste elemente; gaze nocive precum H2S și SO2 nu sunt eliberate în timpul turnării, ceea ce este benefic pentru protecția mediului; Colapsabil bun, ușor de curățat; precizie dimensionala ridicata; eficiență ridicată a producției.
Procesul compozit al nisipului de sticlă-rășină fenolică alcalină alcalină cu suflare de CO2 poate fi utilizat pe scară largă în piesele turnate din oțel, piesele din fier, aliajele de cupru și piesele turnate din aliaj ușor.
Procesul compozit este un proces simplu și convenabil. Procesul este după cum urmează: mai întâi amestecați separat nisipul de rășină și nisipul de silicat de sodiu, apoi puneți-le în două găleți de nisip; apoi adăugați nisipul de rășină amestecat ca nisip de suprafață în cutia de nisip și lire, grosimea stratului de nisip de suprafață este în general de 30-50mm; apoi se adaugă nisip de sticlă de apă pentru a face nisipul din spate să se umple și să se compacteze; în cele din urmă, gazul CO2 este suflat în matriță pentru întărire.
Diametrul tubului de suflare este în general de 25 mm, iar domeniul de întărire este de aproximativ 6 ori diametrul tubului de suflare.
Timpul de suflare depinde de mărimea, forma, debitul de gaz și zona dopului de evacuare al matriței de nisip (miez). În general, timpul de suflare este controlat în decurs de 15 ~ 40s.
După suflarea matriței de nisip dur (miez), mucegaiul poate fi preluat. Rezistența matriței de nisip (miez) crește rapid. Periați vopseaua în decurs de jumătate de oră după ce ați luat matrița și închideți cutia pentru turnare după 4 ore.
Procesul compozit este deosebit de potrivit pentru instalațiile de turnare a oțelului care nu au echipamente de regenerare a nisipului cu rășină și trebuie să producă piese turnate de înaltă calitate. Procesul este simplu și ușor de controlat, iar calitatea pieselor turnate produse este echivalentă cu cea a altor piese turnate cu nisip din rășină.
Nisipul de silicat de sodiu întărit cu suflare de CO2 poate fi, de asemenea, combinat cu nisip din rășină de poliacrilat de sodiu întărit cu suflare de CO2 pentru producerea de piese turnate de înaltă calitate.
Care sunt avantajele și dezavantajele procesului de nisip silicat de sodiu întărit compus cu ester organic CO2?
În ultimii ani, procesul de nisip silicat de sodiu întărit compozit cu ester organic CO2 are o tendință de extindere a aplicațiilor. Procesul este după cum urmează: adăugați o anumită cantitate de ester organic în timpul amestecării nisipului (de obicei, jumătate din cantitatea normală necesară sau 4 ~ 6% din greutatea sticlei de apă); după finalizarea modelării, suflați CO2 pentru a întări la rezistența de eliberare a matriței (în general este necesară rezistența la compresiune) Rezistența este de aproximativ 0.5 MPa); după demoldare, esterul organic continuă să se întărească, iar rezistența nisipului de turnare crește cu o viteză mai mare; după ce CO2 este suflat și plasat timp de 3 ~ 6h, matrița de nisip poate fi combinată și turnată.
Mecanismul de întărire este:
Când nisipul din sticlă de apă suflă CO2, sub acțiunea diferenței de presiune a gazului și a diferenței de concentrație, gazul CO2 va încerca să curgă în toate direcțiile nisipului de turnare. După ce gazul CO2 intră în contact cu sticla de apă, acesta reacționează imediat cu el pentru a forma un gel. Datorită efectului de difuzie, reacția este întotdeauna de la exterior la interior, iar stratul exterior formează mai întâi o peliculă de gel, care împiedică gazul CO2 și sticla de apă să reacționeze în continuare. Prin urmare, într-un timp scurt, indiferent de metoda utilizată pentru controlul CO2 gazului, este imposibil să-l facem să reacționeze cu toată sticla de apă. Conform analizei, atunci când nisipul de turnare atinge cea mai bună rezistență la suflare, sticla de apă care reacționează cu gazul CO2 este de aproximativ 65%. Aceasta înseamnă că sticla de apă nu își exercită pe deplin efectul de legare și cel puțin 35% din sticla de apă nu reacționează. Întăritorul ester organic poate forma un amestec uniform cu liantul și poate da un joc complet efectului de legare al liantului. Toate părțile nisipului de bază acumulează rezistență la aceeași viteză.
Creșterea cantității de sticlă de apă adăugată va crește rezistența finală a matriței de nisip, dar rezistența sa reziduală va crește, făcând dificilă curățarea nisipului. Când cantitatea adăugată de sticlă de apă este prea mică, rezistența finală este prea mică și nu poate îndeplini cerințele de utilizare. În producția reală, cantitatea de sticlă de apă adăugată este în general controlată la aproximativ 4%.
Când se utilizează ester organic singur pentru întărire, cantitatea generală de ester organic adăugată este de 8-15% din cantitatea de sticlă de apă. Când se utilizează întărirea compozită, se estimează că aproximativ jumătate din paharul de apă a fost întărit atunci când CO2 este suflat și aproximativ jumătate din paharul de apă nu s-a întărit încă. Prin urmare, este mai potrivit ca cantitatea de esteri organici să reprezinte 4 până la 6% din cantitatea de sticlă de apă.
Metoda de întărire compozită poate juca pe deplin avantajele duale ale întăririi cu CO2 și a întăririi cu ester organic și poate exercita pe deplin efectul de lipire a sticlei de apă pentru a obține o viteză de întărire rapidă, eliberare timpurie a mucegaiului, rezistență ridicată, pliabilitate bună și cost redus. Efect cuprinzător.
Cu toate acestea, procesul de întărire compozit CO2-ester organic trebuie să adauge cu 0.5 până la 1% mai multă sticlă de apă decât metoda simplă de întărire a esterului organic, ceea ce va crește dificultatea regenerării nisipului de sticlă de apă folosit.
De ce este ușor să producem nisip lipicios atunci când procesul de nisip cu silicat de sodiu este utilizat pentru a produce piese turnate din fier? Cum se previne?
Când matrița de nisip (miez) din nisip de silicat de sodiu este utilizată pentru turnarea pieselor turnate din fier, este adesea produs nisip lipicios serios, care limitează aplicarea sa în producția de fontă.
Na2O, SiO2 din nisipul silicatului de sodiu și oxidul de fier produs de metalul lichid în timpul turnării formează silicat cu topire redusă. După cum s-a menționat mai devreme, dacă acest compus conține sticlă amorfă mai fuzibilă, forța de legătură dintre acest strat de sticlă și suprafața turnării este foarte mică, iar coeficientul de contracție este diferit de cel al metalului. Stresul mare este ușor de îndepărtat de pe suprafața turnării fără lipirea nisipului. Dacă compusul format pe suprafața turnării are un conținut ridicat de SiO2 și un conținut redus de FeO, MnO etc., structura sa solidificată are practic o structură cristalină, care va fi combinată ferm cu turnarea, rezultând nisip lipicios. .
Când nisipul cu silicat de sodiu este utilizat pentru a produce piese turnate din fier, datorită temperaturii scăzute de turnare și a conținutului ridicat de carbon al pieselor turnate din fier, fierul și manganul nu sunt ușor oxidate, iar stratul de nisip lipicios rezultat are o structură cristalină și este dificil pentru a stabili un strat adecvat între piesele turnate din fier și stratul de nisip lipicios. Grosimea stratului de oxid de fier este diferită de nisipul de rășină dintre turnare și stratul de nisip lipicios, care poate produce un film de carbon strălucitor prin piroliza rășinii atunci când se produce piese turnate din fier, astfel încât stratul de nisip lipicios nu este ușor de îndepărtat.
Pentru a preveni producerea nisipului de sticlă cu apă sifonată din producția de piese turnate din fier, pot fi utilizate acoperiri adecvate. Cum ar fi vopseaua pe bază de apă, suprafața trebuie uscată după vopsire, astfel încât vopseaua cu uscare rapidă pe bază de alcool este cea mai bună.
În general, piesele turnate din fier pot adăuga, de asemenea, o cantitate adecvată de pulbere de cărbune (cum ar fi 3% până la 6%) (fracție de masă) la nisipul silicatului de sodiu, astfel încât piroliza pulberii de cărbune dintre turnare și stratul de nisip poate produce un film de carbon strălucitor. Nu este udat de metale și oxizii lor, astfel încât stratul de nisip lipicios este ușor decojit din turnare.
Se așteaptă ca nisipul cu silicat de sodiu să devină nisip de turnare ecologic, fără descărcare de nisip uzat?
Sticla de apă este incoloră, inodoră și netoxică. Nu va provoca probleme grave dacă atinge pielea și hainele și clătește cu apă, dar trebuie evitată stropirea în ochi. Sticla de apă nu conține gaze iritante sau nocive degajate în timpul amestecării nisipului, modelării, întăririi și turnării și nu există poluare neagră și acidă. Cu toate acestea, dacă procesul este necorespunzător și se adaugă prea mult silicat de sodiu, colapsabilitatea nisipului cu silicat de sodiu nu va fi bună, iar praful va zbura în timpul curățării nisipului, ceea ce va provoca și poluare. În același timp, este dificil să se regenereze nisipul vechi, iar evacuarea nisipului uzat provoacă poluare alcalină mediului.
Dacă aceste două probleme pot fi depășite, nisipul cu silicat de sodiu poate deveni nisip de turnare ecologic, practic, fără descărcare de nisip uzat.
Măsura fundamentală pentru rezolvarea acestor două probleme este reducerea cantității de sticlă de apă adăugată la mai puțin de 2%, care practic poate scutura nisipul. Când se reduce cantitatea de sticlă de apă adăugată, se reduce și Na2O rezidual din nisipul vechi. Folosind o metodă relativ simplă de regenerare uscată, este posibil să se mențină Na2O rezidual în nisipul circulant sub 0.25%. Acest nisip recuperat poate îndeplini cerințele de aplicare ale nisipului de turnare simplă pentru piesele turnate din oțel de dimensiuni mici și mijlocii. În acest moment, chiar dacă nisipul vechi cu silicat de sodiu nu folosește metoda umedă scumpă și complicată pentru a se regenera, dar se folosește metoda uscată relativ simplă și ieftină, poate fi reciclată complet, practic nu se descarcă nisip uzat și raportul de nisip la fier Se poate reduce la mai puțin de 1: 1.
Cum se regenerează în mod eficient nisipul cu silicat de sodiu?
Dacă Na2O rezidual din nisipul vechi de silicat de sodiu este prea mare, după adăugarea silicatului de sodiu în nisip, nisipul de turnare nu va avea suficient timp utilizabil, iar acumularea de prea mult Na2O va deteriora refractaritatea nisipului de cuarț. Prin urmare, Na2O rezidual trebuie îndepărtat cât mai mult posibil la regenerarea nisipului de silicat de sodiu folosit.
Vă rugăm să păstrați sursa și adresa acestui articol pentru reimprimare: Precauții pentru turnarea cu nisip a sticlei de apă
Minghe Compania de turnare sub presiune sunt dedicate fabricării și furnizează piese de turnare de calitate și de înaltă performanță (gama de piese turnate sub presiune din metal include în principal Turnare sub presiune cu perete subțire,Hot Cast casting sub presiune,Turnare sub presiune în cameră rece), Serviciu rotund (Serviciu de turnare sub presiune,Prelucrare Cnc,Fabricarea mucegaiului, Tratament de suprafață). Orice cerință personalizată de turnare sub presiune din aluminiu, magneziu sau turnare sub presiune din Zamak / zinc și alte cerințe de turnare sunt binevenite să ne contacteze.
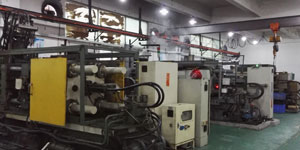
Sub controlul ISO9001 și TS 16949, toate procesele sunt efectuate prin sute de mașini avansate de turnare sub presiune, mașini cu 5 axe și alte facilități, variind de la blastere la mașini de spălat Ultra Sonic. Minghe nu numai că are echipamente avansate, dar are o echipă de ingineri cu experiență, operatori și inspectori pentru a face realitatea designul clientului.
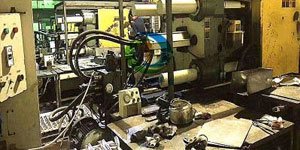
Producător contract de piese turnate sub presiune. Capacitățile includ piese de turnare sub presiune din aluminiu cu cameră rece de la 0.15 lbs. la 6 lbs., schimbare rapidă configurată și prelucrare. Serviciile cu valoare adăugată includ lustruire, vibrare, debavurare, sablare, vopsire, placare, acoperire, asamblare și scule. Materialele lucrate includ aliaje precum 360, 380, 383 și 413.
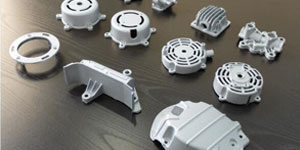
Asistență la proiectarea turnării sub presiune din zinc / servicii de inginerie simultană. Producător personalizat de piese turnate sub presiune din zinc. Pot fi fabricate piese turnate în miniatură, piese turnate sub presiune înaltă, piese turnate multi-glisante, piese turnate convenționale, piese turnate sub formă de unități și piese turnate independente și piese turnate sigilate în cavitate. Piesele turnate pot fi fabricate în lungimi și lățimi de până la toleranță de +/- 24 in.
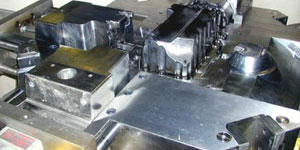
Producător certificat ISO 9001: 2015 de magneziu turnat sub presiune, capabilitățile includ turnare sub presiune cu magneziu de înaltă presiune de până la 200 tone cameră fierbinte și 3000 tone cameră rece, proiectare scule, lustruire, turnare, prelucrare, vopsire cu pulbere și lichide, QA complet cu capacități CMM , asamblare, ambalare și livrare.
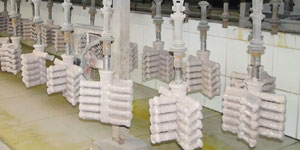
Certificat ITAF16949. Serviciul de turnare suplimentar include investiții de turnătorie,turnare cu nisip,Turnarea gravitației, Pierdere spumă turnare,Turnare centrifugă,Turnarea în vid,Turnare permanentă a matriței, .Capacitățile includ EDI, asistență tehnică, modelare solidă și procesare secundară.
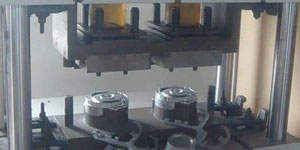
Industrii de turnare Părți Studii de caz pentru: Mașini, biciclete, aeronave, instrumente muzicale, ambarcațiuni, dispozitive optice, senzori, modele, dispozitive electronice, carcase, ceasuri, mașini, motoare, mobilier, bijuterii, jiguri, telecomunicații, iluminat, dispozitive medicale, dispozitive fotografice, Roboți, sculpturi, echipamente de sunet, echipamente sportive, scule, jucării și multe altele.
Ce vă putem ajuta să faceți în continuare?
∇ Accesați pagina principală pentru China turnare sub presiune
→Piese de turnare-Aflați ce am făcut.
→ Ralated Tips About Servicii de turnare sub presiune
By Producător de turnare sub presiune Minghe | Categorii: Articole utile |Material Etichete: Turnare din aluminiu, Turnarea zincului, Turnarea cu magneziu, Turnare cu titan, Turnare din oțel inoxidabil, Turnare din alamă,Turnarea bronzului,Distribuirea videoclipului,Istoricul companiei,Turnare din aluminiu | Comentarii dezactivate