Diversi factori care afectează stabilitatea dimensională a pieselor turnate
Îmbunătățirea continuă a preciziei dimensionale a pieselor turnate de investiții și reducerea deșeurilor produse de supradimensionare a fost întotdeauna unul dintre principalele obiective urmărite de lucrătorii de turnare de investiții în țară și în străinătate.
1. Stabilitatea dimensională a pieselor turnate de investiții
1. Stabilitatea dimensională a modelului de ceară și factorii săi de influență
În majoritatea cazurilor, dimensiunea matriței de ceară fluctuează foarte mult atunci când dimensiunea turnării fluctuează și există câteva excepții. În general, fluctuația de dimensiune a formei de ceară reprezintă 10% până la 70% din fluctuația de dimensiune a turnării.
Parametrii procesului de turnare au o influență decisivă asupra stabilității dimensionale a matriței de ceară. Principalii factori sunt următorii:
(1) Temperatura de presare a cerii
Diferite materiale de turnare au performanțe diferite datorită influenței temperaturii de presare a cerii. Când se utilizează materiale de turnare pe bază de ceară, temperatura de presare a cearelor este foarte sensibilă la influența stabilității dimensionale a matriței de ceară, în timp ce materialele de turnare pe bază de rășină au o influență mai mică.
(2) Presiunea de injecție
Când presiunea este mică, rata de contracție a matriței de ceară scade semnificativ atunci când presiunea crește. Cu toate acestea, după ce presiunea este crescută într-o anumită măsură (≥1.6MPa), presiunea nu are aproape niciun efect asupra dimensiunii matriței de ceară. Nu este de mirare că rezultatele testelor străine concluzionează adesea că „presiunea nu are nimic de-a face cu dimensiunea matriței de ceară”, dar impresia multor companii naționale nu este pe deplin aceeași.
(3) Debit
Debitul materialului matriței poate fi modificat în următoarele două moduri, dar influența asupra dimensiunii matriței de ceară nu este aceeași:
· Prin modificarea setării vitezei de curgere a presei de ceară, această metodă are un efect redus asupra contracției matriței de ceară. Cu toate acestea, are o influență importantă asupra umplerii și calității suprafeței pieselor cu pereți subțiri cu forme complexe sau matrițelor de ceară cu miezuri.
· Această metodă are o mare influență prin schimbarea zonei secțiunii transversale a orificiului de injecție cu ceară, deoarece creșterea zonei secțiunii transversale a orificiului de injecție cu ceară nu numai că poate reduce temperatura de presare a ceară, ci și prelungi solidificarea timpul materialului matriței la orificiul de injecție cu ceară, crescând astfel compactarea matriței de ceară Gradul de contracție și contracția suprafeței sunt reduse.
(4) Timpul de injectare
Așa-numitul timp de injectare aici include trei perioade de timp de umplere, compactare și întreținere. Timpul de umplere se referă la timpul pentru materialul de turnare pentru a umple cavitatea de turnare; compactarea se referă la timpul de la umplerea turnării până la închiderea duzei de injecție cu ceară; și menținerea se referă la timpul de la închiderea duzei de injecție cu ceară până la ejecția matriței.
Timpul de injecție are un efect semnificativ asupra ratei de contracție a matriței de ceară. Acest lucru se datorează faptului că mai mult material de mucegai poate fi stors în cavitate prin creșterea timpului de injecție, iar matrița de ceară va fi mai compactă, reducând astfel rata de contracție. Greutatea modelului de ceară crește odată cu timpul de compactare prelungit. Timpul de compactare ar trebui să fie adecvat. Dacă timpul de compactare este prea lung, materialul matriței de la orificiul de injecție cu ceară s-a solidificat complet și compactarea nu va funcționa. Se poate observa și din Figura 4 că, atunci când timpul de injecție este scurt (15-25 secunde), temperatura de presare a cerii crește, iar rata de contracție crește; dar când timpul de injecție este extins la 25-35s (sub premisa că timpul de umplere rămâne constant, efectivul de mai sus este de a prelungi timpul de compactare) Influența temperaturii de presare a ceară devine mai mică; când timpul de injecție crește la peste 35 de secunde, va apărea situația opusă, adică, pe măsură ce crește temperatura de presare a ceară, rata de contracție a formei de ceară va scădea în schimb. Acest fenomen poate fi explicat ca creșterea temperaturii materialului matriței și prelungirea timpului de compactare au același efect ca și creșterea gradului de compactare a matriței de ceară.
(5) Echipament de presare a temperaturii de turnare și ceară
Temperatura de turnare este ridicată, matrița de ceară se răcește încet și rata de contracție crește. Acest lucru se datorează faptului că matrița de ceară se află încă în turnarea prin compresie înainte ca matrița să fie ejectată și contracția este limitată, dar după ce matrița este ejectată, devine liber să se micșoreze. Prin urmare, dacă temperatura matriței de ceară este ridicată atunci când matrița este eliberată, rata de contracție finală va fi mare și invers, rata de contracție va fi mică.
În același mod, sistemul de răcire al presei de ceară poate avea un impact de aproximativ 0.3% asupra dimensiunii matriței de ceară.
În cele din urmă, merită subliniat faptul că, atunci când se utilizează materiale de matriță pe bază de ceară, pasta de ceară este un sistem de coexistență trifazat de solid, lichid și gaz. Raportul de volum dintre cele trei faze are o mare influență asupra dimensiunii matriței de ceară. Relația proporțională dintre aceste trei nu poate fi controlată în producția reală, care este, de asemenea, un motiv important pentru stabilitatea dimensională slabă a matrițelor de ceară folosind materiale de turnare pe bază de ceară.
2. Influența materialului învelișului și a procesului de realizare a învelișului asupra stabilității dimensionale a pieselor turnate
Influența învelișului matriței asupra dimensiunii turnării este cauzată în principal de expansiunea termică și deformarea termică (fluare la temperatură ridicată) a învelișului matriței în timpul arderii și de restricționarea (obstrucția) învelișului matriței asupra contracției de răcire a turnare.
(1) Expansiunea termică a învelișului
Depinde în principal de materialul învelișului. Diferite materiale refractare au rate de expansiune diferite. Dintre refractarele utilizate în mod obișnuit, silica topită are cea mai mică rată de expansiune, urmată de silicatul de aluminiu, iar silica este cea mai mare și inegală. După testare, se determină că învelișul de silicat de aluminiu poate fi încălzit de la temperatura camerei până la 1000 ℃, învelișul poate produce o expansiune de aproximativ 0.25%, ceea ce reprezintă o mică proporție din contracția totală a dimensiunii turnării. Prin urmare, dacă se utilizează astfel de materiale refractare, învelișul Are o stabilitate dimensională mai bună, cum ar fi siliciu topit, fără îndoială, va fi mai bun. Cu toate acestea, dacă se utilizează silice, dimensiunea cojii fluctuează foarte mult.
(2) Deformare termică (fluare la temperatură ridicată)
De exemplu, o carcasă care folosește sticlă de apă ca liant are un grad de fluaj semnificativ mai mare la temperaturi ridicate peste 1000 ° C decât cel al solului de siliciu și al carcasei de silicat de etil. Deși corindonul fuzionat în sine are o refractare ridicată, din cauza prezenței impurităților, cum ar fi oxidul de sodiu, temperatura de ardere a coajei mai mare de 1000 ℃ poate provoca, de asemenea, fluare, rezultând o stabilitate dimensională slabă.
(3) Reținerea învelișului matriței pe contracția turnării - retragerea și pliabilitatea învelișului matriței Acest lucru depinde în principal de materialul învelișului matriței.
Pe scurt, materialele refractare joacă un rol major în influența cochiliei asupra fluctuației de dimensiune a turnării, dar rolul liantului nu poate fi ignorat. În schimb, impactul procesului de fabricare a cochiliilor este mic.
3. Influența stresului cauzată de răcirea neuniformă a pieselor turnate asupra stabilității dimensionale
Rata de răcire a fiecărei părți a turnării (inclusiv a sistemului de închidere) este diferită, ceea ce generează stres termic și deformează turnarea, afectând astfel stabilitatea dimensională. Acest lucru este adesea întâlnit în producția efectivă. Reducerea ratei de răcire a pieselor turnate și îmbunătățirea combinației de alergători sunt măsuri preventive eficiente.
2. Cheia îmbunătățirii ratei de contracție a mucegaiului de precizie este atribuită corect
„Stabilitatea dimensională” menționată mai sus este diferită de „precizia dimensională” și „precizia (precizia)”. Stabilitatea dimensională (adică precizia) este sinonimă cu consistența dimensională, reflectând gradul de fluctuație dimensională sau dispersie și este de obicei măsurată prin deviația standard σ. Principala cauză a instabilității dimensionale este controlul procesului lax, care este o eroare aleatorie. Acuratețea se referă la gradul în care media aritmetică a multor valori măsurate se abate de la dimensiunea nominală pentru o anumită dimensiune pe turnare, adică dimensiunea abaterii medii. Pentru turnarea investiției, principalul motiv pentru precizia dimensională slabă este atribuirea necorespunzătoare a ratei de contracție în timpul proiectării profilării, care este o eroare sistematică, care este de obicei ajustată prin repararea repetată a matriței. Precizia dimensională (precizia) este o combinație a celor două de mai sus. Prin urmare, pentru a îmbunătăți precizia dimensională a pieselor turnate și a rezolva problema toleranțelor la dimensiunea produsului, nu numai că procesul trebuie controlat strict pentru a reduce fluctuațiile dimensionale, ci și rata de contracție a fiecărei dimensiuni a piesei turnate trebuie atribuită corect la proiectarea profilului .
Este bine cunoscut faptul că contracția finală totală a pieselor turnate de precizie este o combinație de matriță de ceară, contracție din aliaj și o cantitate mică de expansiune a carcasei. Coaja se umflă cu aproximativ 0.25%, iar efectul său este limitat. Deși rata de contracție liniară a aliajului este adesea mai mare decât cea a matriței de ceară, fluctuația dimensională cauzată de procesul de presare a ceară are un impact mai mare. Pentru a reduce costul reparării matriței și a reduce fluctuația dimensiunii turnării, este foarte important să se controleze rata de contracție a matriței de ceară.
1. Contracția matriței de ceară
Contracția matriței de ceară trebuie măsurată după ce dimensiunea matriței de ceară este complet stabilizată. Acest lucru se datorează faptului că contracția matriței de ceară nu se oprește complet după ce matrița este ejectată. Mărimea matriței de ceară se stabilizează uneori doar la câteva zile după ce matrița este ejectată. Cu toate acestea, cea mai mare parte a contracției materialului matriței este practic finalizată în decurs de una până la câteva ore după ce matrița este evacuată. Rata de contracție a formei de ceară are în principal următorii factori de influență:
(1) Tipul de material al matriței;
(2) Dimensiunea secțională a modelului de ceară;
Merită subliniat faptul că dimensiunea secțiunii transversale a matriței de ceară are un efect semnificativ asupra ratei de contracție. De exemplu, rata de contracție a unui material tipic de matriță neumplut la presarea matrițelor de ceară de diferite grosimi. Grosimea secțiunii matriței de ceară nu trebuie să depășească, în general, 13 mm. Când grosimea este mai mare de 13 mm, grosimea peretelui poate fi redusă utilizând blocuri de ceară reci sau miezuri metalice pentru a atinge scopul de a reduce contracția, ceea ce este deosebit de important pentru materialele care nu sunt de umplutură.
Notă: 1. Rata de contracție a materialului de mucegai solubil în apă este de aproximativ 0.25%;
2. Când se utilizează miezuri solubile, miezuri ceramice sau tuburi din sticlă de cuarț, nu există contracție liniară a matriței de ceară în contact cu miezul;
(3) Tipuri de bază
Dimensiunea cavității matriței de ceară este, fără îndoială, compatibilă cu forma miezului. Prin urmare, utilizarea miezurilor a devenit o modalitate de a îmbunătăți precizia dimensională a cavității matriței de ceară.
2. Contracția aliajului
Contracția aliajului depinde în principal de următorii factori:
· Tipul aliajului turnat și compoziția chimică;
· Geometria turnării (inclusiv starea de constrângere și dimensiunea secțiunii);
· Parametrii de turnare, cum ar fi temperatura de turnare, temperatura învelișului, rata de răcire a turnării etc .;
· Utilizarea miezurilor ceramice, tuburilor de sticlă de cuarț etc.
Deoarece temperatura de turnare, temperatura învelișului, viteza de răcire a turnării și alți parametri de proces sunt în general strict controlați de carduri de proces standard în timpul procesului de producție, fluctuațiile de dimensiune cauzate de aceasta nu sunt mari între diferitele loturi de producție. Chiar dacă temperatura de turnare depășește domeniul cerut de specificațiile procesului, fluctuația dimensiunii turnării nu este de obicei mare. Similar cu matrița de ceară, dimensiunea secțiunii turnării și constrângerile învelișului matriței sunt principalii factori care afectează contracția aliajului. Experiența arată că rata de contracție a dimensiunii complet constrânse este de 85% până la 89% din rata de contracție liberă; dimensiunea semi-constrânsă este de 94% până la 95%.
3. Numărul minim al primului lot de probe pentru măsurare
Rata de contracție enumerată mai sus reprezintă date empirice bazate pe experiența din trecut, nu rata reală de contracție. Proiectați și fabricați matrițe conform acestor date, reparația este inevitabilă. Pentru a îmbunătăți acuratețea și rata de succes a reparațiilor și pentru a reduce numărul de reparații, o legătură cheie este să verificați cu atenție dimensiunea unui număr suficient de probe de turnare. Deoarece dimensiunea pieselor turnate pe care le producem nu poate fi exact aceeași, deci numai atunci când numărul de probe măsurate este suficient de mare, valoarea medie obținută poate fi apropiată de media aritmetică reală. Din aceasta, nu este dificil să se vadă că numărul minim de eșantioane de măsurare este direct legat de capacitatea procesului procesului de producție de a controla consistența mărimii produsului (Capacitatea procesului). Dacă piesele turnate au aceeași dimensiune, atunci este necesară testarea unui singur eșantion; În schimb, dacă dimensiunea turnării variază foarte mult,
Este necesar să se măsoare o mulțime de probe pentru a obține date de contracție mai precise. După cum sa menționat mai devreme, capacitatea procesului de producție de a controla dimensiunea poate fi reprezentată de 6σ din dimensiunea de turnare produsă prin acest proces. Din nivelul tehnologic actual al majorității turnătorilor de investiții, Hp este în mare parte peste 0.5, astfel încât primul lot de probe de măsurare necesită în general cel puțin 11 probe.
Trei. Analiza sistemului de măsurare
Atunci când analizăm și rezolvăm problemele legate de dimensiunea produsului, trebuie să fim atenți la acuratețea și fiabilitatea sistemului de măsurare utilizat. În plus față de calibrarea frecventă a instrumentelor și echipamentelor de măsurare în sine, este important, de asemenea, să minimizați erorile de măsurare. Dacă sistemul de măsurare (inclusiv operatorul și metoda de funcționare) are o eroare mare, nu numai respingerile pot fi considerate produse calificate, ci și multe produse calificate pot fi considerate greșite ca respingeri, ambele putând provoca accidente majore sau probleme economice inutile. pierderi. Cel mai simplu mod de a determina dacă un sistem de măsurare este potrivit pentru o sarcină de măsurare specifică este efectuarea testelor de calificare a reproductibilității și repetabilității. Așa-numita repetabilitate înseamnă că același inspector folosește același instrument (sau echipament) și metodă pentru a inspecta aceeași parte și pentru a obține consistența rezultatelor. Reproductibilitatea se referă la consistența rezultatelor obținute de diferiți operatori folosind instrumente diferite pentru a verifica aceeași parte. American Automotive Industry Action Group (Automotive Industry Action Group) stipulează că procentul abaterii standard integrate a repetabilității și reproductibilității R&R în abaterea standard a fluctuațiilor măsurate ale dimensiunii turnării este ≤ 30% ca standard pentru sistemul de măsurare pentru a îndeplini cerințe [5]. În măsurarea unor piese turnate de dimensiuni mari și complexe, nu toate sistemele de măsurare pot îndeplini această cerință. Eroarea de măsurare admisibilă la măsurarea matrițelor ar trebui să fie mai mică, de obicei 1/3.
patru. Structura matriței și nivelul de procesare
Este bine cunoscut faptul că structura matriței și calitatea procesării au o influență importantă asupra dimensiunii și geometriei matriței de ceară. De exemplu, dacă mecanismul de poziționare și prindere este precis și fiabil, dacă jocul de potrivire a pieselor mobile (cum ar fi blocuri mobile, șuruburi etc.) este adecvat, dacă metoda de desen este benefică pentru a asigura precizia dimensională a pieselor turnate , etc. Inutil să spunem, pentru un număr considerabil de fabrici de turnare pe piața internă, nivelul de proiectare și fabricație a matriței trebuie îmbunătățit în continuare de urgență.
Cinci. in concluzie
Din analiza de mai sus, nu este dificil să se vadă că îmbunătățirea preciziei dimensionale a pieselor turnate este un proiect sistematic care implică toate aspectele procesului de producție a turnării investiției. Principalele puncte pot fi rezumate după cum urmează:
1) Controlați strict parametrii procesului de turnare, în special parametrii care au un impact semnificativ asupra dimensiunii turnării.
2) Alegeți materialul adecvat pentru coajă.
3) Colectați, numărați și analizați datele referitoare la contracție într-o metodă corectă care este conformă cu principiile statistice pentru a îmbunătăți acuratețea atribuirii contracției.
4) Monitorizați frecvent sistemul de măsurare (inclusiv echipamentele, personalul de inspecție și tehnologia) pentru a vă asigura că erorile de repetabilitate și reproductibilitate îndeplinesc cerințele specificate.
5) Îmbunătățiți continuu nivelul de proiectare și fabricație a matriței.
6) Măsuri precum corecția turnării și tratamentul termic de stabilizare sunt încă indispensabile în multe ocazii
Vă rugăm să păstrați sursa și adresa acestui articol pentru reimprimare: Diversi factori care afectează stabilitatea dimensională a pieselor turnate
Minghe Compania de turnare sub presiune sunt dedicate fabricării și furnizează piese de turnare de calitate și de înaltă performanță (gama de piese turnate sub presiune din metal include în principal Turnare sub presiune cu perete subțire,Hot Cast casting sub presiune,Turnare sub presiune în cameră rece), Serviciu rotund (Serviciu de turnare sub presiune,Prelucrare Cnc,Fabricarea mucegaiului, Tratament de suprafață). Orice cerință personalizată de turnare sub presiune din aluminiu, magneziu sau turnare sub presiune din Zamak / zinc și alte cerințe de turnare sunt binevenite să ne contacteze.
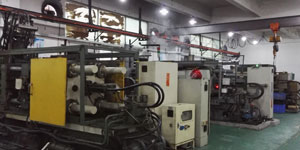
Sub controlul ISO9001 și TS 16949, toate procesele sunt efectuate prin sute de mașini avansate de turnare sub presiune, mașini cu 5 axe și alte facilități, variind de la blastere la mașini de spălat Ultra Sonic. Minghe nu numai că are echipamente avansate, dar are o echipă de ingineri cu experiență, operatori și inspectori pentru a face realitatea designul clientului.
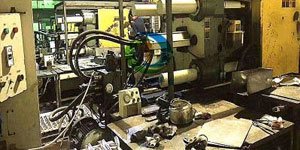
Producător contract de piese turnate sub presiune. Capacitățile includ piese de turnare sub presiune din aluminiu cu cameră rece de la 0.15 lbs. la 6 lbs., schimbare rapidă configurată și prelucrare. Serviciile cu valoare adăugată includ lustruire, vibrare, debavurare, sablare, vopsire, placare, acoperire, asamblare și scule. Materialele lucrate includ aliaje precum 360, 380, 383 și 413.
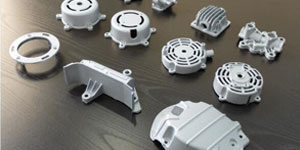
Asistență la proiectarea turnării sub presiune din zinc / servicii de inginerie simultană. Producător personalizat de piese turnate sub presiune din zinc. Pot fi fabricate piese turnate în miniatură, piese turnate sub presiune înaltă, piese turnate multi-glisante, piese turnate convenționale, piese turnate sub formă de unități și piese turnate independente și piese turnate sigilate în cavitate. Piesele turnate pot fi fabricate în lungimi și lățimi de până la toleranță de +/- 24 in.
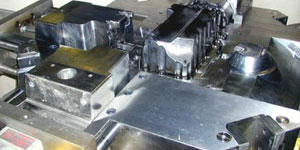
Producător certificat ISO 9001: 2015 de magneziu turnat sub presiune, capabilitățile includ turnare sub presiune cu magneziu de înaltă presiune de până la 200 tone cameră fierbinte și 3000 tone cameră rece, proiectare scule, lustruire, turnare, prelucrare, vopsire cu pulbere și lichide, QA complet cu capacități CMM , asamblare, ambalare și livrare.
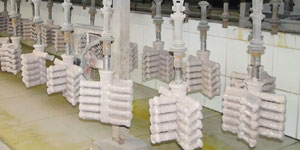
Certificat ITAF16949. Serviciul de turnare suplimentar include investiții de turnătorie,turnare cu nisip,Turnarea gravitației, Pierdere spumă turnare,Turnare centrifugă,Turnarea în vid,Turnare permanentă a matriței, .Capacitățile includ EDI, asistență tehnică, modelare solidă și procesare secundară.
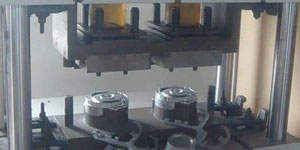
Industrii de turnare Părți Studii de caz pentru: Mașini, biciclete, aeronave, instrumente muzicale, ambarcațiuni, dispozitive optice, senzori, modele, dispozitive electronice, carcase, ceasuri, mașini, motoare, mobilier, bijuterii, jiguri, telecomunicații, iluminat, dispozitive medicale, dispozitive fotografice, Roboți, sculpturi, echipamente de sunet, echipamente sportive, scule, jucării și multe altele.
Ce vă putem ajuta să faceți în continuare?
∇ Accesați pagina principală pentru China turnare sub presiune
→Piese de turnare-Aflați ce am făcut.
→ Ralated Tips About Servicii de turnare sub presiune
By Producător de turnare sub presiune Minghe | Categorii: Articole utile |Material Etichete: Turnare din aluminiu, Turnarea zincului, Turnarea cu magneziu, Turnare cu titan, Turnare din oțel inoxidabil, Turnare din alamă,Turnarea bronzului,Distribuirea videoclipului,Istoricul companiei,Turnare din aluminiu | Comentarii dezactivate