Tendința de dezvoltare a pieselor turnate pentru automobile și tehnologia sa de fabricație
Turnarea este una dintre cele mai vechi metode de formare a metalelor. Aproximativ 15% până la 20% din piesele auto sunt piese turnate produse prin diferite metode de turnare. Aceste piese turnate sunt în principal componente cheie ale sistemului de alimentare și componente structurale importante. În prezent, tehnologia de producție a pieselor turnate pentru automobile în țările dezvoltate din industriile auto europene și americane este avansată, cu o bună calitate a produselor, eficiență ridicată a producției și poluare scăzută a mediului. Turnarea materiilor prime și auxiliare a fost serializată și standardizată, iar întregul proces de producție a fost mecanizat, automatizat și inteligent. Aceste țări folosesc în general tehnologia digitală pentru a îmbunătăți nivelul de proiectare a procesului de turnare. Rata de respingere a turnării este de aproximativ 2% până la 5% și a fost stabilit un sistem de servicii transnațional și a fost implementat suportul tehnic de rețea. În contrast, deși producția pieselor turnate pentru automobile în țara mea este relativ mare, cele mai multe dintre acestea sunt piese turnate negre cu valoare adăugată și conținut tehnic relativ scăzute și o structură relativ simplă, care este departe de nivelul străin. Acest articol discută în principal direcția de dezvoltare a pieselor turnate și a tehnologiei auto din nevoile de dezvoltare a economiei de energie și protecției mediului.
Proiectare integrată a pieselor turnate pentru automobile
Odată cu cerințele în creștere pentru conservarea energiei și protecția mediului înconjurător a automobilelor și reducerea costurilor de producție, vom folosi pe deplin avantajele turnării pentru a realiza turnarea pieselor integrate printr-o proiectare rezonabilă și optimizarea structurală a mai multor piese formate prin ștanțare, sudare, forjare și turnare. Formarea poate reduce în mod eficient greutatea pieselor și reduce procesele de prelucrare inutile, obținând astfel piese ușoare și performante.
Principala formă a carcasei comune a osiei monolitice este că țevile din oțel fără sudură sunt presate în cele două capete ale carcasei axului sub formă de manșoane cu jumătate de ax și fixate cu știfturi pentru a forma ansamblul carcasei axei. Pentru a îmbunătăți în continuare rezistența și rigiditatea carcasei osiei și a simplifica procesul, FAW Group a dezvoltat o carcasă integrată a axului în care manșoanele axelor (piesele de pe ambele părți ale carcasei axei din figura 1) sunt turnate direct pe carcasa osiei. Procesarea este dificilă, reducerea costurilor este mai mare, structura carcasei osiei tinde să fie simplă, iar rigiditatea carcasei osiei este mai bună, poate fi transformată într-o formă complexă și ideală, grosimea peretelui poate fi schimbată, se poate obține o distribuție ideală a tensiunii și rezistența și rigiditatea sunt amândouă mari, funcționează fiabil. Datorită integrării manșonului axului, dimensiunea turnării este semnificativ crescută. Lungimea turnării este de 2 258 mm, iar greutatea sa individuală depășește 200 kg. Având în vedere caracteristicile acestei piese turnate integrate, compania a stabilit o linie de producție dedicată pentru a asigura producția.
Tendința de dezvoltare a integrării pieselor turnate pentru automobile este mai evidentă în dezvoltarea pieselor turnate din aliaj neferos. Pentru a utiliza pe deplin caracteristicile procesului de turnare care pot realiza producția de piese turnate complexe, proiectarea integrată a pieselor turnate de înaltă presiune, cum ar fi panourile interioare ale ușilor, cadrele scaunelor, cadrele panourilor de instrumente, cadrele frontale și paravanele de protecție au a apărut. Dimensiunile sunt semnificativ mai mari decât cele produse în prezent. Pentru piese turnate, pentru producție este necesară o mașină de turnare sub presiune cu un tonaj de la 4 la 000 tone sau chiar mai mare.
Greutatea pieselor turnate pentru automobile
Pe premisa de a asigura rezistența și siguranța mașinii, reduceți greutatea la bord a mașinii cât mai mult posibil pentru a obține o greutate redusă, îmbunătățind astfel puterea mașinii, reducând consumul de combustibil și reducând poluarea evacuării. Pentru fiecare reducere de 100 kg a greutății bordului vehiculului, consumul de combustibil la 100 de kilometri poate fi redus cu 0.3 până la 0.6 L. Dacă greutatea vehiculului este redusă cu 10%, eficiența consumului de combustibil poate fi crescută cu 6% până la 8%. Având nevoie de protecție a mediului și de economisire a energiei, greutatea redusă a automobilelor a devenit tendința dezvoltării auto din lume, iar greutatea pieselor turnate a devenit, de asemenea, una dintre direcțiile importante de dezvoltare a pieselor turnate.
Design ușor al pieselor turnate pentru automobile
Datorită necesității factorului de siguranță general al pieselor turnate, proiectarea cu grosime egală este una dintre metodele principale de proiectare pentru piesele turnate pentru automobile. Cu toate acestea, principalul dezavantaj al designului cu grosime egală este că performanța structurală nu poate fi utilizată pe deplin, iar greutatea turnării este crescută. Utilizați analiza CAE, optimizarea topologiei și alte metode pentru a optimiza proiectarea pieselor, astfel încât valorile de solicitare ale părților pieselor să fie apropiate, adică grosimea peretelui fiecărei părți să fie inconsistentă și părțile cu dimensiuni mici forțele sunt subțiate sau inutile pentru a reduce piesele. greutatea. Având în vedere că formarea turnării poate realiza formarea turnărilor complexe, se pot realiza diverse secțiuni transversale de formă neregulată. Când proiectați, utilizați CAE sau optimizarea topologiei pentru a efectua analize de stres pe componente. În funcție de distribuția forței, determinați forma piesei și grosimea materialului piesei specifice. Prin armarea, săparea găurilor și îngroșarea pieselor turnate, greutatea pieselor poate fi redusă foarte mult.
Piese turnate din aliaj ușor
Utilizarea materialelor din aliaj ușor precum aluminiu și magneziu este în prezent principala măsură de reducere a greutății adoptată de producătorii de automobile din diferite țări. Densitatea aluminiului este doar 1/3 din cea a oțelului și are o rezistență excelentă la coroziune și ductilitate. Magneziul are o densitate mai mică, doar 2/3 din cea a aluminiului și are o fluiditate excelentă în condiții de turnare la presiune înaltă. Rezistența specifică (raportul rezistență la masă) al aluminiului și magneziului este destul de mare, ceea ce joacă un rol decisiv în reducerea greutății proprii și îmbunătățirea eficienței combustibilului. Competitivitatea crescândă a industriei auto din SUA în ultimii doi ani este strâns legată de adoptarea pe scară largă a pieselor turnate structurale din aluminiu-magneziu și a pieselor turnate integrate.
Noua serie 5 lansată de compania germană BMW este echipată cu cea mai recentă generație de blocuri compozite magneziu-aluminiu în linie cu șase cilindri, greutatea este redusă cu 10 kg față de generația anterioară, ceea ce îmbunătățește foarte mult performanța și combustibilul economie. Cu toate acestea, trebuie remarcat faptul că prețul materiilor prime pentru aliajele ușoare precum aluminiu și magneziu este mult mai mare decât cel al materialelor din oțel, ceea ce limitează aplicarea sa mai largă în industria auto. Cu toate acestea, în ciuda prețului relativ ridicat al materiilor prime, consumul actual de piese turnate din magneziu și aluminiu pentru biciclete a crescut an de an. Pe de o parte, progresul tehnologic a compensat creșterea costurilor. Pe de altă parte, concurența pe piață a forțat producătorii de automobile să reducă profiturile și să adopte mai multe aliaje ușoare. Cu toate acestea, pentru a crește considerabil cantitatea de aliaje ușoare și a reduce prețul de achiziție al lingourilor de magneziu și aluminiu, dezvoltarea unei tehnologii avansate de formare este una dintre chei.
Performanță ridicată a materialelor de turnare pentru automobile
Îmbunătățirea performanței materialului, astfel încât greutatea unitară a piesei să reziste la sarcini mai mari, este una dintre metodele de reducere eficientă a greutății turnării. Piesele turnate structurale de tip consolă reprezintă o mare parte din piesele turnate pentru automobile, astfel încât dezvoltarea pieselor turnate a devenit unul dintre obiectivele de atenție. Prin tratamentul termic și alte măsuri, microstructura materialului este schimbată, îmbunătățind astfel rezistența, rigiditatea sau rezistența pieselor, care pot reduce în mod eficient greutatea pieselor.
Fierul ductil cu temperaturi ridicate nu numai că are o rezistență mai mare decât materialele obișnuite din oțel turnat, dar are și o densitate mai mică decât oțelul. Densitatea sa este de 7.1 g / cm3, în timp ce densitatea oțelului turnat este de 7.8 g / cm3, care este un material recomandat pe scară largă în ultimii ani. . Adoptă fontă ductilă cu temperaturi reduse, care este cu 10% mai ușoară decât piesele turnate din oțel sub aceeași dimensiune a pieselor turnate. Dongfeng Motor Corporation a efectuat o lucrare de verificare ușoară pe un anumit tip de vehicul utilitar, utilizând fontă ductilă austemperată în locul pieselor turnate din oțel. Având în vedere caracteristicile de rezistență ridicată ale pieselor din fontă ductilă austempered, 14 piese de suspensie au fost reproiectate în forul de experți. În general vorbind, înlocuirea materialului pieselor turnate pentru automobile însoțește adesea designul ușor al pieselor.
În piesele turnate din aliaj de aluminiu și aliaj de magneziu, se folosesc în schimb materiale de înaltă rezistență și rezistență ridicată. Pe baza reducerii greutății originale din aliaj ușor, sunt utilizate materiale performante pentru a reduce și mai mult greutatea. General Motors din Statele Unite folosește în schimb aliaj de înaltă performanță AE44 Aliajul original de aluminiu folosește turnarea la presiune înaltă pentru a produce sub-cadrul, reducând în continuare greutatea aliajului de aluminiu cu 6 kg.
Digitalizarea dezvoltării turnării auto
Combinația cuprinzătoare între dezvoltarea de turnare auto și tehnologia digitală poate îmbunătăți semnificativ nivelul tehnologiei de turnare și poate scurta proiectarea produsului și ciclul de producție de probă. În prezent, tehnologia de fabricație digitală a fost utilizată pe scară largă în dezvoltarea pieselor turnate pentru automobile. În etapa de proiectare a structurii de turnare și proiectarea procesului de turnare, software-ul de proiectare 3D, cum ar fi Pro / E, CATIA și UG, a fost utilizat pe scară largă, iar unele companii avansate de turnare au realizat un design fără hârtie. Software-uri precum MAGMA, ProCAST și Huazhu CAE au fost utilizate pe scară largă pentru a simula procesul de solidificare, microstructura, segregarea compoziției și proprietățile materiale ale pieselor turnate pentru automobile. De asemenea, poate analiza câmpul de viteză, câmpul de concentrare, câmpul de temperatură și faza în procesul de turnare. Simularea câmpurilor, câmpurilor de solicitare etc. poate asigura optimizarea planului de proces înainte de producția în masă.
Pentru a satisface nevoile de dezvoltare rapidă a pieselor turnate pentru automobile, pe baza proiectării și dezvoltării CAD / CAE, RP (tehnologia de prototipare rapidă) a fost utilizat pe scară largă pentru producția rapidă de piese turnate pentru automobile. După obținerea datelor CAD / CAE originale, se adoptă metoda strat cu strat pentru a obține prototipul turnării sau prototipul matriței necesare formării turnării prin lipire, sinterizare sau sinterizare. Primele pot fi probe de turnare produse prin încercare prin turnare investițională, turnare în ipsos și alte metode, în timp ce acestea din urmă pot fi utilizate direct ca matriță pentru fabricarea miezurilor de nisip, iar piesele turnate pot fi turnate prin modelarea ansamblului miezului. În plus, metoda de sinterizare cu pulbere cu laser (SLS) poate fi utilizată pentru a finaliza direct producția de miezuri de nisip și matrițe de nisip, astfel încât să se obțină matrițele de nisip necesare pentru producția de încercare a pieselor turnate. Pentru matrițele exterioare cu structuri relativ simple, mașinile-unelte CNC pot fi, de asemenea, utilizate pentru a prelucra CAM cu materiale plastice prelucrabile pentru a obține cutia miezului și modelul necesar pentru producția de încercare a pieselor turnate sau pentru a procesa direct blocul de nisip pentru a obține matrița de nisip a matriței exterioare direct.
În general vorbind, tehnologia digitală a pătruns în toate aspectele proiectării, dezvoltării și producției de testare, îmbunătățind în mod eficient viteza și eficiența dezvoltării turnării. Principala problemă în prezent este că tehnologiile digitale de proiectare, analiză și fabricare rapidă sunt independente una de cealaltă. Când procesul de dezvoltare este transformat de la o etapă la alta, este necesară și o muncă destul de obositoare de conversie a datelor. Se speră că, în viitor, o platformă unificată de interfață de date poate fi dezvoltată pentru tehnologia digitală aplicată în toate aspectele dezvoltării turnării și pot fi stabilite standarde standardizate de conversie a datelor pentru a realiza o conversie de date fără probleme între diferite software-uri, astfel încât să crească în continuare viteza de dezvoltare a pieselor turnate.
Tehnologia de producție a pieselor turnate cu structură complexă cu pereți subțiri
Odată cu dezvoltarea industriei auto și a cererii de economisire a energiei și de reducere a emisiilor, piesele auto devin din ce în ce mai ușoare. Prin designul cu pereți subțiri, reducerea greutății este o direcție importantă de dezvoltare pentru blocurile de motor. Luați ca exemplu FAW Casting Co., Ltd. pentru producția de blocuri de cilindri din fontă de la FAW-Volkswagen. Blocul cilindric 06A produs timpuriu are o grosime a peretelui de 4.5 mm ± 1.5 mm, iar blocul cilindru EA111 are grosimea peretelui de 4 mm ± 1 mm. Blocul cilindric actual EA888Evo2 produs în masă are o grosime a peretelui de 4 mm ± 1 mm. 3.5 mm ± 0.8 mm, structura produsului blocului cilindric EA888Gen.3 de nouă generație este mai complexă, grosimea peretelui este de doar 3 mm ± 0.5 mm, în prezent este cel mai subțire bloc cilindru din fontă gri. Deși există probleme cu miezurile rupte, miezurile plutitoare și fluctuațiile mari ale grosimii pereților în producția de masă, prin controlul calității miezurilor de nisip și a turnării nisipului, procesul de turnare orizontal utilizat pe scară largă poate îndeplini în continuare cerințele de producție ale cilindrilor EA888Evo2. Dar nu poate îndeplini cerințele de producție ale blocului de cilindri EA888Gen.3, deci trebuie adoptat întregul proces de turnare verticală a ansamblului central.
Tehnologia de fabricație a pieselor structurale mari din aliaj de aluminiu-magneziu
Odată cu creșterea cerințelor de economisire a energiei, protecție a mediului și reducerea costurilor componentelor, piesele turnate structurale pe scară largă din aliaj de aluminiu-magneziu au devenit o tendință importantă de dezvoltare, iar tehnologia lor de fabricație a devenit, de asemenea, un focus actual de dezvoltare. În prezent, principalele tehnologii de producție pentru piese structurale din aliaj de aluminiu-magneziu pe scară largă includ turnarea la presiune înaltă, turnarea prin presare și turnarea la presiune scăzută. Datorită eficienței ridicate a producției de turnare la presiune înaltă și a bunei calități a produsului, acesta a devenit principalul proces de producție în prezent. Dezvoltarea tehnologiei sale de fabricație se concentrează în principal pe antrenarea ușoară a gazului în timpul procesului de turnare la presiune înaltă și pe formarea de pori în interiorul pieselor turnate, care nu pot îmbunătăți problema tratamentului termic.
Compania Germania Fulai a dezvoltat procesul de turnare prin aspirare sub presiune negativă, întregul proces de turnare sub presiune se realizează sub vid ridicat (mai puțin de 30 mbar). Metalul topit trece prin matriță, camera de presiune și conducta de aspirație în stare de vid și este aspirat din cuptor de conducta de aspirație fără oxidare, iar vaporii agentului de eliberare sunt, de asemenea, descărcați de sistemul de vid. Principalele caracteristici ale procesului de turnare prin aspirare sub presiune negativă menționat mai sus sunt: atunci când se începe turnarea cantitativă, întregul sistem se află într-o stare de vid ridicată; în procesul de turnare cantitativă, gazul din cavitate și metalul topit pot fi evacuate eficient; în timpul procesului de turnare Nu există oxidare a topiturii metalului; nu există pierderi de căldură în timpul procesului de turnare și o temperatură de turnare mai mică poate fi utilizată pentru turnare, iar umplerea fluxului laminar ne-perturbat poate fi efectuată sub monitorizare în timp real. Procesul de mai sus a fost aplicat cu succes producției de masă a pieselor turnate structurale auto din cadrul Forumului Auto Expert, oferind metode avansate de formare și procese pentru aplicarea pieselor turnate din aliaj ușor de înaltă calitate.
Compania elvețiană Buhler a dezvoltat un sistem de vid cu două circuite pentru producerea pieselor turnate structurale. Această tehnologie de producție se numește tehnologie de producție structurală. Utilizarea tehnologiei de producție structurală poate crește viteza de aspirare, obținând astfel condiții de producție stabile și îmbunătățind semnificativ turnarea sub presiune Calitatea pieselor. Așa cum se arată în Fig. 5, orificiul de extracție a aerului unui circuit din sistemul de vid cu două circuite este dispus la capătul superior al camerei de presiune și este utilizat în principal pentru a extrage aerul din camera de presiune. Începe când pistonul de injecție se deplasează înainte pentru a sigila orificiul de turnare și se închide când pistonul este pe punctul de a sigila orificiul de aspirație. Cealaltă setare a circuitului este aceeași cu procesul tradițional de vid și este utilizată în principal pentru a extrage aerul din cavitate. În prezent, tehnologia a fost aplicată cu succes la fabricarea turnurilor de amortizare a șocurilor integrate din aliaj de aluminiu, a panourilor interioare ale ușilor și a șinelor caroseriei autoturismelor.
Tehnologie de formare a turnării de precizie pentru piese turnate
Denumirea obișnuită de turnare de precizie a pieselor turnate pentru automobile se referă în principal la spuma pierdută și tehnologia de turnare prin investiții. Odată cu dezvoltarea tehnologiei de formare a turnării automobilelor, formarea de precizie a turnării se referă la un tip de metodă de turnare a turnării. Piesele turnate produse prin acest tip de metodă de formare pot fi utilizate direct fără tăiere sau mai puțin tăiere. Odată cu cerințele în creștere pentru precizia dimensională a pieselor turnate, tehnologia turnării de precizie s-a dezvoltat rapid în ultimii ani și au apărut o serie de noi metode de turnare, cum ar fi turnarea cu nisip de precizie, turnarea cu spumă pierdută, turnarea sub presiune controlată și turnarea sub presiune. Metoda de turnare Cosworth este o metodă dezvoltată de Regatul Unit care utilizează ansamblul miezului de nisip de zirconiu și pompa electromagnetică pentru a controla turnarea. A fost utilizat cu succes în producția de masă a blocurilor de cilindri din aliaj de aluminiu și au apărut multe variante de proces, cum ar fi utilizarea turnării la presiune scăzută în locul proceselor electromagnetice, cum ar fi turnarea pompei. Acest tip de metodă de turnare poate produce cilindri din aliaj de aluminiu cu grosimea peretelui de 3.5 până la 4.0 mm, care este procesul reprezentativ actual al turnării cu nisip de precizie.
Procesul de turnare a spumei pierdute a fost inventat în 1965, iar principalele piese turnate auto sunt blocuri de cilindri, chiulase, conducte de admisie și evacuare și alte produse și au format o producție la scară largă. De la introducerea tehnologiei de turnare a spumei pierdute în anii 1990, în secolul al XX-lea, țara mea a început să prindă contur și a fost promovată de stat ca cea mai folosită tehnologie înaltă și nouă pentru transformarea industriei tradiționale de turnătorie. În prezent, există trei procese de turnare cu precizie de investiții în țara mea: învelișul de silicat de sodiu, învelișul compozit și învelișul de siliciu. Dintre acestea, calitatea suprafeței turnării utilizate la producerea învelișului de siliciu pentru produsele auto poate atinge Ra 20 μm, iar precizia dimensională poate atinge CT1.6. Grad, grosimea minimă a peretelui poate fi de 4 ~ 0.5 mm. Dongfeng Motor Precision Casting Co., Ltd. adoptă procesul de fabricare a carcasei compuse din silicat sol + sticlă de apă pentru a produce piese turnate integrate complexe, ceea ce reduce semnificativ costurile de producție. Tendința de dezvoltare a procesului de turnare a tehnologiei de turnare prin investiții este că piesele turnate se apropie din ce în ce mai mult de produsul final, iar complexitatea și calitatea produselor sunt din ce în ce mai mari. Aplicarea CAD, CAM și CAE a devenit principala tehnologie de dezvoltare a produselor, iar cooperarea profesională a început să apară.
Turnarea sub vid, turnarea sub presiune cu oxigen, turnarea sub presiune reologică sau tixotropă a metalelor semi-solide și alte metode de proces dezvoltate pe baza procesului de turnare la presiune înaltă sunt concepute pentru a elimina defectele turnării, pentru a îmbunătăți calitatea internă și pentru a extinde gama de aplicații a turnărilor sub presiune. . În timpul procesului de turnare prin presare, topitura este umplută și solidificată sub presiune, ceea ce are avantajele netezii, fără stropi de metal, mai puține pierderi de oxidare a lichidului metalic, economisire de energie, funcționare sigură și reducerea găurilor de turnare și a altor defecte. Este utilizat în sub-cadre din aliaj de aluminiu etc. Dezvoltarea și aplicarea pieselor turnate din aliaj de aluminiu de înaltă performanță au fost utilizate pe scară largă.
Creșterea continuă a producției de automobile necesită urgent dezvoltarea producției de turnare în direcția de înaltă calitate, performanță excelentă, aproape de formă netă, varietăți multiple, consum redus și cost redus. Deoarece aproximativ 15% până la 20% din piesele unui vehicul complet sunt piese turnate. Acest lucru necesită ca industria de turnare să aplice continuu diverse tehnologii noi și materiale noi pentru a îmbunătăți nivelul general al turnării. Tehnologia de formare a pieselor turnate de precizie poate îndeplini cerințele menționate mai sus ale pieselor turnate pentru automobile, iar aplicația sa va acoperi, de asemenea, diferite procese de producție a pieselor turnate.
Concluzie
Pentru a se adapta la cerințele din ce în ce mai stricte ale reglementărilor privind protecția mediului, automobilele se dezvoltă în direcția unei greutăți mai mici. Pentru fiecare reducere de 10% a greutății vehiculului, consumul de combustibil poate fi redus cu 5.5%, consumul de combustibil poate fi crescut cu 3% până la 5%, iar emisiile pot fi reduse cu aproximativ 10%. Aplicarea pieselor turnate din aluminiu-magneziu și a altor elemente neferoase, dezvoltarea pieselor turnate integrate la scară largă și aplicarea pe scară largă a tehnologiei de formare de precizie a turnării sunt principalele modalități de realizare a pieselor turnate ușoare pentru automobile. Prin urmare, este necesar să se realizeze cercetarea, dezvoltarea și producția pieselor turnate pentru automobile prin intermediul materialelor de turnare de înaltă performanță și a aplicării extinse a echipamentelor de automatizare pe baza utilizării extinse a tehnologiei digitale pentru a satisface nevoile industriei automobilelor moderne.
Vă rugăm să păstrați sursa și adresa acestui articol pentru reimprimare: Tendința de dezvoltare a pieselor turnate pentru automobile și tehnologia sa de fabricație
Minghe Compania de turnare sub presiune sunt dedicate fabricării și furnizează piese de turnare de calitate și de înaltă performanță (gama de piese turnate sub presiune din metal include în principal Turnare sub presiune cu perete subțire,Hot Cast casting sub presiune,Turnare sub presiune în cameră rece), Serviciu rotund (Serviciu de turnare sub presiune,Prelucrare Cnc,Fabricarea mucegaiului, Tratament de suprafață). Orice cerință personalizată de turnare sub presiune din aluminiu, magneziu sau turnare sub presiune din Zamak / zinc și alte cerințe de turnare sunt binevenite să ne contacteze.
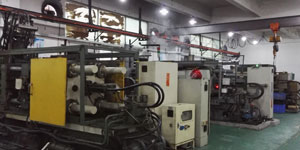
Sub controlul ISO9001 și TS 16949, toate procesele sunt efectuate prin sute de mașini avansate de turnare sub presiune, mașini cu 5 axe și alte facilități, variind de la blastere la mașini de spălat Ultra Sonic. Minghe nu numai că are echipamente avansate, dar are o echipă de ingineri cu experiență, operatori și inspectori pentru a face realitatea designul clientului.
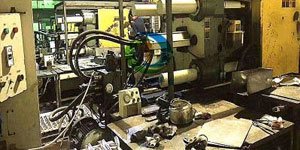
Producător contract de piese turnate sub presiune. Capacitățile includ piese de turnare sub presiune din aluminiu cu cameră rece de la 0.15 lbs. la 6 lbs., schimbare rapidă configurată și prelucrare. Serviciile cu valoare adăugată includ lustruire, vibrare, debavurare, sablare, vopsire, placare, acoperire, asamblare și scule. Materialele lucrate includ aliaje precum 360, 380, 383 și 413.
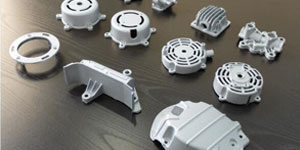
Asistență la proiectarea turnării sub presiune din zinc / servicii de inginerie simultană. Producător personalizat de piese turnate sub presiune din zinc. Pot fi fabricate piese turnate în miniatură, piese turnate sub presiune înaltă, piese turnate multi-glisante, piese turnate convenționale, piese turnate sub formă de unități și piese turnate independente și piese turnate sigilate în cavitate. Piesele turnate pot fi fabricate în lungimi și lățimi de până la toleranță de +/- 24 in.
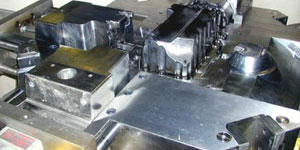
Producător certificat ISO 9001: 2015 de magneziu turnat sub presiune, capabilitățile includ turnare sub presiune cu magneziu de înaltă presiune de până la 200 tone cameră fierbinte și 3000 tone cameră rece, proiectare scule, lustruire, turnare, prelucrare, vopsire cu pulbere și lichide, QA complet cu capacități CMM , asamblare, ambalare și livrare.
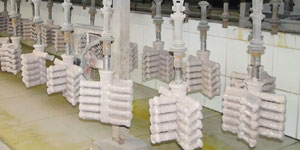
Certificat ITAF16949. Serviciul de turnare suplimentar include investiții de turnătorie,turnare cu nisip,Turnarea gravitației, Pierdere spumă turnare,Turnare centrifugă,Turnarea în vid,Turnare permanentă a matriței, .Capacitățile includ EDI, asistență tehnică, modelare solidă și procesare secundară.
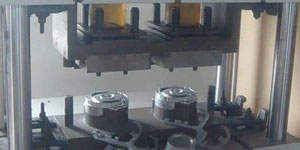
Industrii de turnare Părți Studii de caz pentru: Mașini, biciclete, aeronave, instrumente muzicale, ambarcațiuni, dispozitive optice, senzori, modele, dispozitive electronice, carcase, ceasuri, mașini, motoare, mobilier, bijuterii, jiguri, telecomunicații, iluminat, dispozitive medicale, dispozitive fotografice, Roboți, sculpturi, echipamente de sunet, echipamente sportive, scule, jucării și multe altele.
Ce vă putem ajuta să faceți în continuare?
∇ Accesați pagina principală pentru China turnare sub presiune
→Piese de turnare-Aflați ce am făcut.
→ Ralated Tips About Servicii de turnare sub presiune
By Producător de turnare sub presiune Minghe | Categorii: Articole utile |Material Etichete: Turnare din aluminiu, Turnarea zincului, Turnarea cu magneziu, Turnare cu titan, Turnare din oțel inoxidabil, Turnare din alamă,Turnarea bronzului,Distribuirea videoclipului,Istoricul companiei,Turnare din aluminiu | Comentarii dezactivate