Controlul atmosferei în timpul procesului de sinterizare al oțelului sinterizat și performanța acestuia
Atmosfera sinterizată și selecția sa
Dacă se are în vedere doar sinterizarea oțelului cu conținut de carbon, atmosfera de sinterizare utilizată în industria metalurgiei pulberilor este hidrogen, azot, azot + hidrogen (potențial de carbon sau fără potențial de carbon), descompunerea amoniacului, gaz endotermic, gaz endotermic + azot, sinteză Pentru gaze și vid, alegerea corectă a atmosferei de sinterizare necesită înțelegerea caracteristicilor și performanțelor diferitelor atmosfere de sinterizare și selectarea în conformitate cu principiile asigurării calității și reducerii costurilor.
Hidrogenul este o atmosferă puternic reducătoare. Mulți oameni cred că hidrogenul are un anumit efect de decarburare, dar acest lucru depinde în mare măsură de puritatea hidrogenului utilizat, mai degrabă decât de hidrogenul însuși. În general, hidrogenul după electroliză sau conversie catalitică conține o anumită cantitate de gaz de impuritate, cum ar fi H2O, O2, CO și CH4 etc., uneori cantitatea totală poate ajunge la aproximativ 0.5%. Prin urmare, cel mai bine este să îl uscați și să îl purificați înainte de utilizare pentru a reduce conținutul de oxigen și punctul de rouă. Cu toate acestea, datorită prețului ridicat al hidrogenului, hidrogenul pur este rar folosit ca atmosferă de sinterizare, cu excepția cazului în care există motive speciale.
Azotul este un gaz inert sigur și ieftin, dar deoarece azotul pur nu are reducibilitate la temperatura de sinterizare, azotul pur este rar utilizat ca atmosferă de sinterizare în producția de oțel tradițional pentru metalurgia pulberilor. În ultimii ani, deoarece costul purificării azotului a scăzut și etanșeitatea la cuptorul de sinterizare s-a îmbunătățit, azotul a început să fie folosit și ca atmosferă de sinterizare pentru sinterizarea oțelului care conține carbon.
În ultimii ani, amestecul de azot-hidrogen a fost din ce în ce mai utilizat la sinterizarea oțelului carbon. Azotul / hidrogenul este de obicei utilizat între 95 / 5-50 / 50. Acest amestec are un anumit grad de reducibilitate și punctul de rouă poate ajunge sub -60 ℃, în general vorbind, trebuie adăugată o anumită cantitate de CH4 sau C3H8 pentru a menține un anumit potențial de carbon la utilizarea acestui gaz la 1050-1150 -1250, în timp ce sinterizează oțelul carbon peste 1120 ℃ nu trebuie să controleze potențialul de carbon. Acest amestec poate fi utilizat pentru sinterizarea aliajelor pe bază de fier care conțin crom sub XNUMX ° C fără oxidare.
Amoniacul descompus se face prin descompunerea amoniacului gazos printr-un catalizator încălzit, inclusiv 75% H2 și 25% N2. Dar, în general, o cantitate mică de molecule de amoniac nedescompuse rămân întotdeauna în amoniacul descompus. Când sunt în contact cu metalul fierbinte la temperaturi ridicate, se vor descompune în atomi de hidrogen și azot foarte activi, nitrurând astfel metalul. Studii recente au arătat că, dacă este controlat corespunzător, sinterizarea AstaloyCrM la 1120 ° C va descompune și amoniaca amestecul 90N2 / 10H2 cu o reducere mai puternică. Principalul motiv este că acești atomi de hidrogen activi care tocmai au fost descompuși în timpul procesului de sinterizare sunt mai eficienți decât 90N2 / hidrogenul din gazul mixt 10H2 are o reducere mai puternică și poate reduce în mod eficient stratul de oxid în afara particulelor AstaloyCrM. Pentru a purifica și descompune amoniacul, îl puteți trece prin apă și îl puteți usca sau puteți utiliza alumină activă sau sită moleculară pentru a îndepărta restul de amoniac.
Gazul endoterm este un tip de gaz amestecat obținut prin amestecarea gazului hidrocarbonat (CH4 sau C3H8) cu aer într-o anumită proporție, preîncălzire la 900-1000 ° C și transformare catalitică prin catalizator de oxid de nichel. În funcție de raportul dintre aer și gaz de cărbune, procesul de conversie este însoțit de reacții endoterme sau exoterme. Gazul mixt rezultat se numește gaz endoterm sau gaz exoterm și reacția poate fi după cum urmează:
CmHn+m(O2+3.774N2)—mCO+n/H2+1.887mN2
Dacă reacția de mai sus trebuie efectuată complet, adică toți C în CmHm tocmai au reacționat cu O2 în aer, aerul / gazul necesar ar trebui să fie m / 2 (1 + 3.774), care este 2.387m. De exemplu, dacă gazul hidrocarbonat utilizat este CH4, aerul / gazul necesar ar trebui să fie 2.387, iar gazul mixt produs în acest moment include 40.9% H2, 38.6% N2 și 20.5% CO. După reacție, gazul amestecat conține H2 Conținutul de CO și CO scade odată cu creșterea aerului / gazului, dar conținutul de H2O și CO2 crește. De asemenea, arată că potențialul de carbon din gazul mixt după reacție scade odată cu creșterea aerului / gazului, iar performanța de oxidare crește. Acesta este, de asemenea, principalul motiv pentru care gazul exoterm este rar utilizat la sinterizarea oțelului cu conținut de carbon, iar majoritatea gazului endoterm este utilizat.
În general, gazul mixt produs de aer / gaz între 2.0-3.0 se numește absorbție Gaz fierbinte, iar gazul mixt produs atunci când raportul este mai mare de 5.0 se numește gaz exoterm. Relația dintre punctul de rouă al gazului endoterm produs cu CH4 ca materie primă și aerul / gazul arată că aerul / gazul crește doar de la 2.4 la 2.5, iar punctul de rouă al gazului mixt produs crește de la -25 ° C la peste 0 ° C. Prin urmare, dacă utilizatorii produc singuri gaz endoterm, ar trebui să acorde o atenție specială controlului raportului aer / gaz din materiile prime (de preferință nu mai mult de 2.4) pentru a obține gaz endoterm cu un punct de rouă suficient de scăzut. În gazul mixt după reacție, raportul diferitelor gaze corespunde raportului de la sfârșitul reacției, care este în general (1000-1100 ° C).
După reacție, dacă temperatura gazului se schimbă, potențialul de carbon al gazului mixt, punctul de rouă și raportul diferitelor gaze se vor schimba. Mulți producători de metalurgie a pulberilor utilizează un generator de gaz exoterm pentru a furniza atmosfera de sinterizare necesară pentru mai multe cuptoare de sinterizare în același timp prin conductă. Temperatura atmosferei a fost redusă înainte de a ajunge la cuptorul de sinterizare. . Dacă izolația conductei nu este bună și temperatura peretelui conductei este mai mică de 800 ° C, atunci o parte din carbonul din gazul mixt va fi depus pe peretele conductei sub formă de negru de fum. Cu alte cuvinte, atunci când gazul mixt este reîncălzit la temperatura de sinterizare în cuptorul de sinterizare, căldura sa de carbon este mult mai mică decât potențialul de carbon pe care generatorul de gaz endoterm îl poate oferi.
În acest caz, ar trebui adăugată o cantitate adecvată de metan sau propan la cuptorul de sinterizare pentru a asigura potențialul de carbon din cuptor. Acum, unii producători străini de metalurgie a pulberilor au început să instaleze un mic generator de gaz endoterm lângă fiecare cuptor de sinterizare și să utilizeze gazul endoterm care tocmai a fost produs direct în cuptorul de sinterizare fără răcire, pentru a evita afectarea atmosferei de sinterizare din cauza schimbărilor de temperatură . . Un alt punct care trebuie reamintit este că, chiar și cu efectul catalitic al catalizatorului de oxid de nichel, o cantitate mică de hidrocarbură gazoasă (CH4 sau C3H8 etc.) rămâne în gazul mixt obținut după transport. În plus, între gazele de la 900-1100 ℃ După ce reacția atinge echilibrul, se va produce o cantitate mică de CO2 și H2O (gazos), care trebuie uscate înainte de utilizare.
Adăugarea de azot la gazul endoterm poate reduce conținutul relativ de CO, CO2 și H2O în gazul endoterm, astfel încât să tamponeze sensibilitatea atmosferei la potențialul de carbon și la punctul de rouă și să ușureze unii coeficienți de corelație în atmosfera de sinterizare. a controla.
Gazul sintetic este o metodă propusă de producătorii străini de cuptoare de sinterizare în ultimii ani pentru a genera direct (dilua) gaz endoterm în cuptorul de sinterizare (fără a fi nevoie de un generator de gaz endoterm în afara cuptorului). Amestecă alcool metilic gazos și azot într-o anumită proporție și apoi îl trece direct în cuptorul de sinterizare. Următoarele reacții vor apărea în zona de sinterizare la temperatură înaltă:
CH3OH — CO + 2H2
Deoarece raportul CO și H2 din gazul descompus este egal cu raportul gazului endoterm produs prin metoda obișnuită cu CH4, iar azotul mixt poate fi combinat pentru a sintetiza o atmosferă mixtă cu aceeași compoziție ca și gazul endoterm (1L Metanul corespunde azotului 1.05nm3). Cel mai mare avantaj al său este că nu necesită un generator de gaz endoterm în afara cuptorului. În plus, utilizatorii pot amesteca diferite cantități de azot gazos pentru a produce gaz endoterm diluat în funcție de propriile cerințe.
Vidul este, de asemenea, un fel de atmosferă de sinterizare, care este utilizată în principal pentru sinterizarea oțelului inoxidabil și a altor materiale, dar nu este utilizată în mod obișnuit pentru sinterizarea oțelului carbon.
Proprietățile fizice ale atmosferei de sinterizare
Majoritatea lucrărilor și rapoartelor privind atmosfera de sinterizare discută în principal despre comportamentul chimic dintre diferite atmosfere de sinterizare și corpul sinterizat în timpul procesului de sinterizare, dar rareori discută influența proprietăților fizice ale diferitelor atmosfere asupra sinterizării, deși acest efect este în multe cazuri. să fie ignorat. De exemplu, diferența de vâscozitate a gazului va determina gradientul de concentrație chimică a corpului sinterizat de la suprafață la interior de-a lungul deschiderii, afectând astfel proprietățile de suprafață ale corpului sinterizat. Pentru un alt exemplu, capacitatea termică și conductivitatea termică a diferitelor gaze au o mare influență asupra timpului de sinterizare și a ratei de răcire. Această secțiune listează principalele proprietăți fizice ale unor atmosfere de sinterizare la diferite temperaturi (în jurul temperaturii de sinterizare) pentru referința cititorilor.
Exemple de probleme legate de atmosferă în timpul sinterizării
1 Exemple de crăpături pe suprafața pieselor în timpul depilării
Când se folosește un cuptor de sinterizare cu bandă de plasă și se folosește gaz endoterm ca atmosferă de sinterizare, dacă rata de creștere a temperaturii și atmosfera din zona de depilare nu sunt bine controlate, va apărea fisurarea suprafeței. Mulți oameni cred că acest fenomen se datorează descompunerii rapide a lubrifiantului. Este cauzat, dar nu este cazul. Motivul real este că monoxidul de carbon din gazul endoterm este descompus în carbon solid și dioxid de carbon în intervalul de temperatură de 450-700 ℃ sub cataliza fierului, nichelului și a altor metale. Carbonul solid nou depus în porii corpului sinterizat este cel care își extinde volumul și provoacă fenomenul de fisurare a suprafeței menționat mai sus.
Calitatea pieselor variază în funcție de temperatură în timpul procesului de sinterizare în diferite atmosfere. Dintre acestea, atmosfera 3 este gaz de cărbune endoterm uscat, iar atmosferele 4 și 5 sunt gaz de cărbune endoterm adăugat cu cantități diferite de vapori de apă. Se poate observa că în timpul procesului de sinterizare, calitatea pieselor începe să scadă la aproximativ 200 ° C, ceea ce înseamnă că lubrifiantul solid din interiorul acestuia este descompus continuu și revarsă corpul de sinterizare, reducându-i calitatea. Desigur, dacă nu există lubrifiant solid în pulberea amestecată, fenomenul de mai sus nu există. Dacă se utilizează cele trei atmosfere de mai sus, cu cât atmosfera este mai uscată de calitatea corpului sinterizat la aproximativ 450 ° C, cu atât acest fenomen va fi mai grav.
Dar ceea ce este interesant este că, atunci când se folosește gazul 3 (gaz endotermic uscat), crăparea de suprafață are loc indiferent de prezența lubrifianților solizi, ceea ce indică faptul că nu este direct legată de depilare, iar gazul bogat în carbon este găsit în fisuri. Fenomen, putem afirma corectitudinea explicației de mai sus.
Există mai multe modalități de a evita apariția fenomenului de cracare menționat mai sus. Cel mai direct este să schimbăm atmosfera de sinterizare din gaz endoterm în amestec de hidrogen-azot fără a sparge liniile rupte. Dacă atmosfera de sinterizare nu poate fi schimbată, există două metode. Unul este să suflați o parte din gazul endotermic care conține vapori de apă în zona de depilare a cuptorului de sinterizare. Cu toate acestea, această metodă este dificil de obținut un control stabil în funcționarea efectivă.
Controlul fluxului de aer al cuptorului de sinterizare nu este bun, iar fenomenul atmosferei cu punct de rouă ridicat care intră în zona de sinterizare poate afecta calitatea sinterizării. A doua și cea mai bună metodă este de a crește viteza de încălzire a pieselor din zona de depilare a cuptorului de sinterizare pentru a face să treacă 450 cât mai curând posibil. În zona în care apare fisurarea la -600 ° C, așa-numita depilare rapidă este de obicei concepută pentru acest fenomen.
2 Exemplu de sinterizare AstaloyCrM
Cromul metalic este utilizat pe scară largă în oțelurile aliate datorită prețului său scăzut și a efectului bun de întărire. Cu toate acestea, oțelul sinterizat care conține crom va întâmpina multe probleme în procesul său de producție. Una dintre acestea este producerea de pulbere de fier care conține crom, care trebuie supusă unui proces strict de reducere a atomizării și de recoacere pentru a obține pulbere de materie primă cu un conținut mai mic de oxigen și carbon. .
Honganas AB din Suedia este în prezent singurul producător din lume care poate produce această pulbere de materie primă la un cost redus. Al doilea este că, chiar dacă se poate obține pulbere de fier cu conținut de crom de înaltă calitate, dacă sinterizarea și temperatura medie, în special atmosfera de sinterizare, nu pot fi bine controlate, va fi mai probabil să se oxideze în timpul sinterizării și oxidării, iar performanța de sinterizare va fi redusă.
Calculele termodinamice și un număr mare de experimente au dovedit că, dacă gazul endoterm este utilizat ca atmosferă de sinterizare a AsaloyCrM, cerințele de sinterizare nu pot fi îndeplinite chiar dacă punctul de rouă este foarte scăzut.
Cu alte cuvinte, pentru sinterizarea AsaloyCrM se poate utiliza numai hidrogen pur sau amestec de hidrogen-azot. În prezent, cele mai multe dintre acestea din urmă sunt utilizate. , Proporția de hidrogen reprezintă 5% -20%. Cititorului trebuie să i se reamintească nu numai pentru a asigura compoziția atmosferei de sinterizare, ci și pentru a asigura calitatea atmosferei de sinterizare.
Așa-numita calitate de aici se referă la gradul de oxidare din atmosfera de sinterizare, care este în general calibrat de presiunea parțială a oxigenului din atmosferă. La sinterizare la 1120 ℃, dacă presiunea parțială a oxigenului în atmosferă este mai mică de 1 × 10-14Pa, oxidarea nu va avea loc în timpul procesului de sinterizare.
Când temperatura este redusă, pentru a preveni oxidarea, presiunea parțială a oxigenului în atmosferă trebuie să fie chiar scăzută. De asemenea, se poate asigura că AsaloyCrM sinterizat la 1125 ℃ nu se va oxida la 1 × 10-14Pa. Calculul de mai sus a fost confirmat de date experimentale.
Vă rugăm să păstrați sursa și adresa acestui articol pentru reimprimare: Controlul atmosferei în timpul procesului de sinterizare al oțelului sinterizat și performanța acestuia
Minghe Compania de turnare sub presiune sunt dedicate fabricării și furnizează piese de turnare de calitate și de înaltă performanță (gama de piese turnate sub presiune din metal include în principal Turnare sub presiune cu perete subțire,Hot Cast casting sub presiune,Turnare sub presiune în cameră rece), Serviciu rotund (Serviciu de turnare sub presiune,Prelucrare Cnc,Fabricarea mucegaiului, Tratament de suprafață). Orice cerință personalizată de turnare sub presiune din aluminiu, magneziu sau turnare sub presiune din Zamak / zinc și alte cerințe de turnare sunt binevenite să ne contacteze.
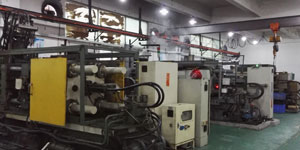
Sub controlul ISO9001 și TS 16949, toate procesele sunt efectuate prin sute de mașini avansate de turnare sub presiune, mașini cu 5 axe și alte facilități, variind de la blastere la mașini de spălat Ultra Sonic. Minghe nu numai că are echipamente avansate, dar are o echipă de ingineri cu experiență, operatori și inspectori pentru a face realitatea designul clientului.
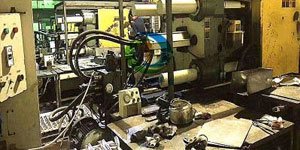
Producător contract de piese turnate sub presiune. Capacitățile includ piese de turnare sub presiune din aluminiu cu cameră rece de la 0.15 lbs. la 6 lbs., schimbare rapidă configurată și prelucrare. Serviciile cu valoare adăugată includ lustruire, vibrare, debavurare, sablare, vopsire, placare, acoperire, asamblare și scule. Materialele lucrate includ aliaje precum 360, 380, 383 și 413.
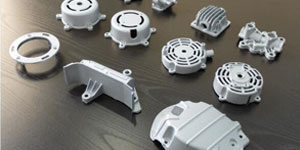
Asistență la proiectarea turnării sub presiune din zinc / servicii de inginerie simultană. Producător personalizat de piese turnate sub presiune din zinc. Pot fi fabricate piese turnate în miniatură, piese turnate sub presiune înaltă, piese turnate multi-glisante, piese turnate convenționale, piese turnate sub formă de unități și piese turnate independente și piese turnate sigilate în cavitate. Piesele turnate pot fi fabricate în lungimi și lățimi de până la toleranță de +/- 24 in.
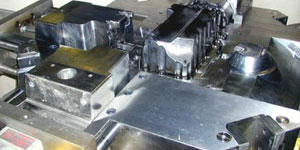
Producător certificat ISO 9001: 2015 de magneziu turnat sub presiune, capabilitățile includ turnare sub presiune cu magneziu de înaltă presiune de până la 200 tone cameră fierbinte și 3000 tone cameră rece, proiectare scule, lustruire, turnare, prelucrare, vopsire cu pulbere și lichide, QA complet cu capacități CMM , asamblare, ambalare și livrare.
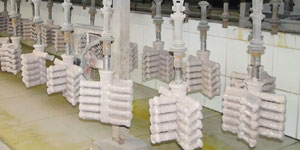
Certificat ITAF16949. Serviciul de turnare suplimentar include investiții de turnătorie,turnare cu nisip,Turnarea gravitației, Pierdere spumă turnare,Turnare centrifugă,Turnarea în vid,Turnare permanentă a matriței, .Capacitățile includ EDI, asistență tehnică, modelare solidă și procesare secundară.
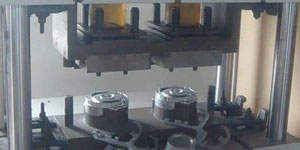
Industrii de turnare Părți Studii de caz pentru: Mașini, biciclete, aeronave, instrumente muzicale, ambarcațiuni, dispozitive optice, senzori, modele, dispozitive electronice, carcase, ceasuri, mașini, motoare, mobilier, bijuterii, jiguri, telecomunicații, iluminat, dispozitive medicale, dispozitive fotografice, Roboți, sculpturi, echipamente de sunet, echipamente sportive, scule, jucării și multe altele.
Ce vă putem ajuta să faceți în continuare?
∇ Accesați pagina principală pentru China turnare sub presiune
→Piese de turnare-Aflați ce am făcut.
→ Ralated Tips About Servicii de turnare sub presiune
By Producător de turnare sub presiune Minghe | Categorii: Articole utile |Material Etichete: Turnare din aluminiu, Turnarea zincului, Turnarea cu magneziu, Turnare cu titan, Turnare din oțel inoxidabil, Turnare din alamă,Turnarea bronzului,Distribuirea videoclipului,Istoricul companiei,Turnare din aluminiu | Comentarii dezactivate